Share this
What Is the Multi Echelon Inventory Optimization (MEIO) Strategy?
by Rin Mosher on May. 22, 2024
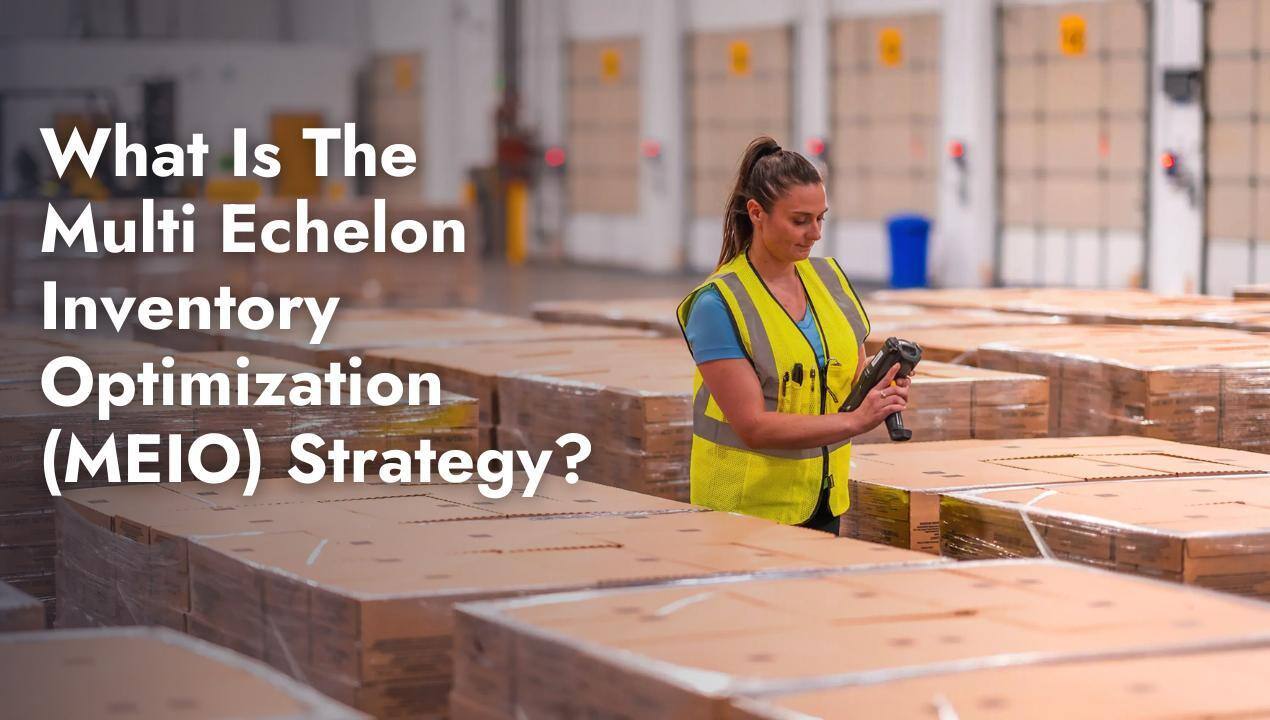
Multi Echelon Inventory Optimization (MEIO) is a supply chain optimization strategy that makes handling the inventory complexities of a growing ecommerce business much more manageable. However, MEIO isn’t just about keeping products in stock – it's a strategy that enhances coordination across all levels of the supply chain through demand planning and analytics, and may be exactly what your business needs to improve efficiency and profitability as it grows.
In this article, we explain what multi echelon inventory optimization is, how it synchronizes your supply chain, and when implementing this strategy can be most beneficial for your ecommerce business.
What Is Multi Echelon Inventory Optimization (MEIO)?
Multi echelon inventory optimization is a strategy that aims to minimize total inventory costs while ensuring service levels are maintained. It addresses inventory at various points across the supply chain, from its state with suppliers, at manufacturing plants, and finished goods at distribution centers and retail outlets.
Key aspects of MEIO include:
- Inventory Positioning: Determining where to hold inventory within the supply chain to optimally balance costs and service levels.
- Demand Forecasting: Using advanced forecasting techniques to predict customer demand more accurately and plan inventory requirements at each echelon.
- Service Level Optimization: Ensuring that inventory levels at each stage of the supply chain are sufficient to prevent stockouts and maintain customer satisfaction.
- Cost Minimization: Reducing the overall costs associated with holding and moving inventory, including warehousing costs, transportation costs, and costs related to stockouts or overstocking.
- Coordination Across Echelons: Ensuring that decisions made at one stage of the supply chain take into account the impact on other stages.
- Advanced Analytics and Technology: Utilizing software and data to make well-informed decisions on inventory management in real time.
Implementing MEIO can lead to several benefits, including reduced inventory costs, improved service levels, enhanced supply chain efficiency, and greater responsiveness to market changes. It's particularly useful for complex supply chains with multiple interconnected stages and where demand variability and lead times can significantly impact inventory decisions.
Multi Echelon Inventory Optimization vs. Single Echelon Inventory Optimization
MEIO has become a popular alternative to Single Echelon Inventory Optimization (SEIO), a system that focuses on optimizing inventory at a single stage of the supply chain. Both strategies aim to manage inventory efficiently and cost-effectively but differ in scope, complexity, and objectives.
SEIO focuses on inventory at one specific point within the supply chain, such as a single warehouse, distribution center, or retail outlet. It uses simpler models like Economic Order Quantity (EOQ) and reorder point calculations to minimize holding costs, prevent stockouts, and meet local demand on a granular level.
While straightforward and easy to manage, this approach does not account for the broader implications of inventory decisions across multiple echelons of the supply chain. SEIO provides quick wins in terms of cost savings and efficiency improvements but may fall short in addressing the complexities and interdependencies of a more extensive supply network.
MEIO is intended to avoid these issues by communicating inventory levels across the entire supply chain rather than treating each stage individually. It recognizes that although each link has its own job, every part is interdependent in some way. For example, a business’ decision to purchase more product from suppliers will affect the inventory levels of both the warehouse and distribution center, depending on where inventory is moved – a decision that may not be communicated clearly with SEIO.
MEIO involves the real-time sharing of information. Keeping each part of the supply chain informed of changes allows for better planning and ultimately increased supply chain resiliency. For example, consider a mid-size ecommerce company that sells seasonal sports equipment. Using MEIO, they can redistribute inventory from warehouses with lower demand to those in regions where a specific sport is in peak season, ensuring that stock levels are optimized to meet regional demands. This not only reduces the risk of stockouts in high-demand areas but also minimizes overstock in slower regions, leading to more efficient operations and reduced holding costs.
Benefits of Multi Echelon Inventory Optimization
At its core, MEIO is about making strategic improvements in inventory management and allocation across the supply chain. The following are a few examples of the benefits that can come with implementing this strategy:
Cost-Efficiency and Cost-Savings
Cost-efficiency and cost-savings in supply chain management are highly dependent on stock planning. It might seem like a good thing to have plenty of shelved inventory ready for customer orders, but storing excess stock means tying up capital that could be used elsewhere. In the case of perishable items like consumer packaged goods, holding more inventory than necessary can also lead to spoilage.
Multi echelon inventory optimization helps businesses strike the right balance between stocking enough inventory to meet demand and avoiding excess stock by using advanced forecasting techniques and real-time data reporting. It dynamically adjusts inventory levels based on actual demand patterns and supply chain conditions. Software combines the reorder point formula with supply chain KPIs to calculate how much should be ordered and when. MEIO also allows for better inventory placement, ensuring that products are located in the right distribution centers to reduce transportation costs.
Enhanced Agility and Responsiveness
Well-informed stock level plans don't just have the capacity to save businesses money – they can help them weather unexpected challenges as well.
MEIO can help companies maintain agility by taking into account various factors such as supplier lead times, seasonality, and demand. This is a major competitive advantage during times of turbulence. Ecommerce businesses that are prepared are best positioned to meet customer expectations and come out of hard times stronger.
Our Inventory Management Calculator offers a quick and easy way to determine ideal stock levels, even as conditions change. Enable your business to become more agile by using the automatic formulas it comes equipped with.
Free Inventory Management Calculator
Improved Lead Time Management
Lead times can impact ecommerce businesses in several ways. They're key to the customer experience, especially as more consumers would now rather delivery be faster (48%) than cheaper (43%). While shipping carriers are often pointed to as the culprit for delays, upstream stages of the supply chain have a role to play as well.
For instance, poor inventory management can affect how much inventory an ecommerce fulfillment center has available to fulfill orders and push order ready dates back.
Using MEIO to communicate current levels of inventory, production schedules, and supplier capabilities makes it easier to anticipate potential bottlenecks and take corrective action. Meeting customers’ expectation of consistent delivery timelines can also boost their perception of and trust in a brand.
When to Use Multi Echelon Inventory Optimization
Multi echelon inventory optimization is commonly used in multi-channel distribution retail. Companies with complex supply chains involving multiple echelons, such as suppliers, manufacturers, distribution centers, and retail outlets, benefit from MEIO’s ability to keep large networks of independently operating facilities on the same page. Without an integrated system in place, coordinating delivery schedules and inventory allocation is much more difficult. The same argument applies to B2B and wholesale distribution, which impose unique requirements on everything from order packing and pickup to delivery.
Another symptom warranting the use of MEIO is an excess amount of deadstock. Consistently high levels of deadstock indicate ineffective demand forecasting and inventory planning. MEIO uses data from multiple sources to make well-informed decisions on inventory allocation, reducing the risk of overstocking while maintaining essential safety stock.
MEIO is also useful in situations where there is high variability in demand or lead times. Real-time visibility into inventory levels allows for accurate forecasts, even as conditions change.
How to Implement MEIO Effectively
Complex supply chain management strategies require thoughtful planning and execution to work. MEIO specifically calls for robust technology, consistent data reporting, and strong relationships with suppliers.
Robust Supply Chain Technology
The first of those three must-haves, technology, facilitates the communication that makes MEIO possible. Real-time data reporting tools and centralized ecommerce inventory management systems play key roles in keeping everyone on the same page. Upgrading from legacy systems costs money but is more than worthwhile for the cohesiveness it can create.
Partnering with a third-party logistics (3PL) company is another way to obtain the advanced inventory management technology needed for MEIO. Logistics providers that offer their own proprietary systems already have the right infrastructure in place to integrate with your business to maximize efficiency and communication between supply chain stakeholders.
Accurate and Comprehensive Data
Inventory optimization strategies are always at their most effective when based on accurate and comprehensive data. The multi-echelon approach is particularly complex and requires data from multiple channels, suppliers, and distribution centers. Reporting tools can consolidate information from these sources to provide a more complete picture of inventory levels and demand patterns in one place.
The main hurdle in this process is usually data integrity – ensuring that the data is accurate, consistent, and up-to-date. Once this hurdle has been overcome, MEIO tools can use the consolidated data to generate more accurate demand forecasts and optimize inventory levels accordingly.
Buy-In from Partners
Another part of implementing an effective MEIO system is buy-in. Not only will your business need to make technology-enabled processes part of its workflow, but partners as well. Suppliers, warehouses, fulfillment centers, and shipping carriers don’t necessarily have to use the same software – that software simply needs to be able to communicate with other parts of the supply chain.
Need a 3PL Provider?
Ecommerce operations in 2024 are complex, which means that inventory management strategies of the past can’t guarantee you a competitive edge. Implementing an integrated logistics system based on multi echelon inventory optimization is a great first step in improving process efficiency and cost savings.
Shipfusion’s 3PL services make it easy to benefit from MEIO without all the extra work. Our proprietary software with real-time reporting capabilities facilitates the flow of information across the supply chain while providing you with more control. Our dedicated Account Managers are on-site in the warehouse, ready to personally address concerns should they arise. Learn how we can streamline your inventory management.
Share this
You May Also Like
These Related Articles
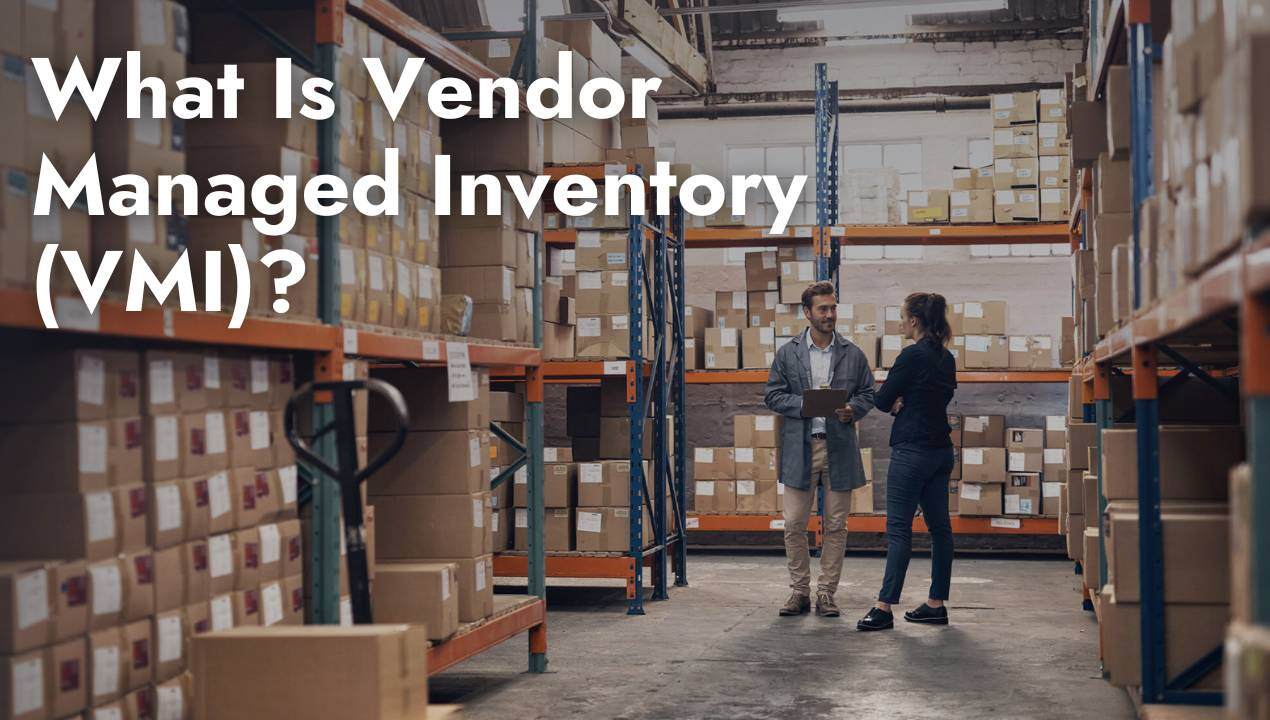
Comparing the Pros and Cons of Vendor Managed Inventory
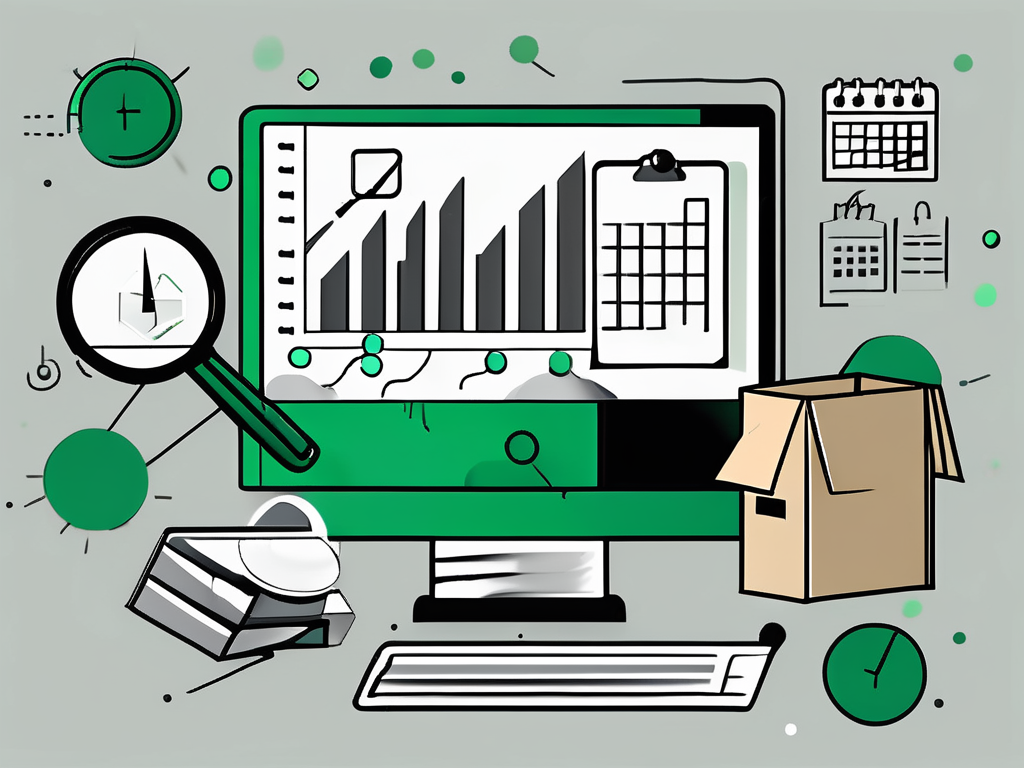
7 Lesser-Known Inventory Forecasting Hacks for Wholesale Orders
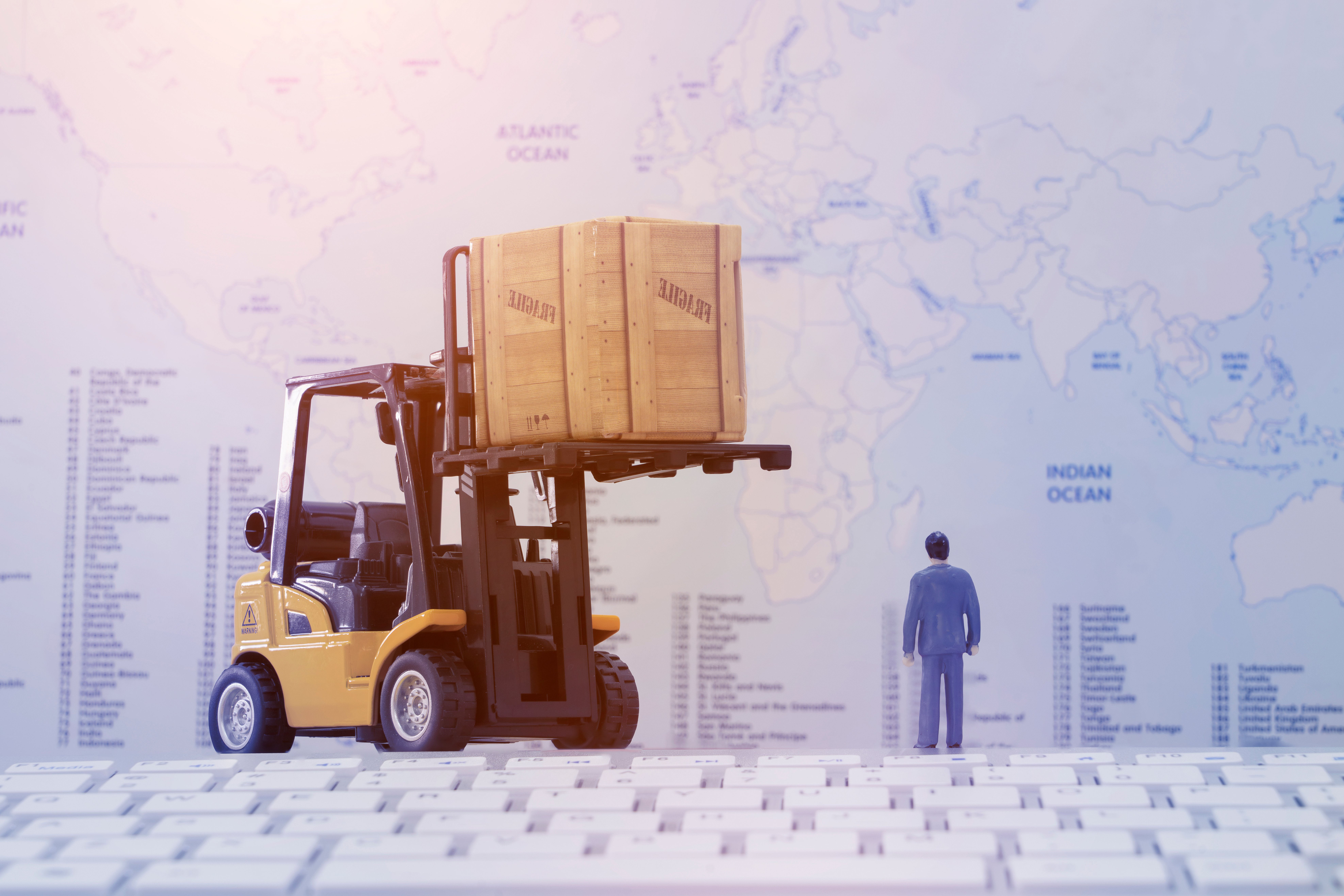
What Is Lot Tracking for Ecommerce Retailers?
- July 2025 (2)
- June 2025 (22)
- May 2025 (27)
- April 2025 (27)
- March 2025 (26)
- February 2025 (26)
- January 2025 (35)
- December 2024 (16)
- November 2024 (22)
- October 2024 (22)
- September 2024 (27)
- August 2024 (9)
- July 2024 (8)
- June 2024 (5)
- May 2024 (8)
- April 2024 (8)
- March 2024 (6)
- February 2024 (6)
- January 2024 (5)
- December 2023 (3)
- November 2023 (3)
- October 2023 (5)
- September 2023 (4)
- August 2023 (2)
- July 2023 (1)
- June 2023 (4)
- March 2023 (2)
- October 2022 (1)
- September 2022 (5)
- August 2022 (4)
- July 2022 (7)
- June 2022 (4)
- May 2022 (4)
- April 2022 (6)
- March 2022 (2)
- February 2022 (1)
- January 2022 (3)
- December 2021 (2)
- November 2021 (4)
- October 2021 (2)
- September 2021 (5)
- August 2021 (4)
- July 2021 (4)
- June 2021 (3)
- May 2021 (2)
- April 2021 (3)
- March 2021 (3)
- February 2021 (3)
- January 2021 (2)
- December 2020 (4)
- November 2020 (2)
- October 2020 (4)
- September 2020 (2)
- July 2020 (5)
- June 2020 (4)
- May 2020 (2)
- April 2020 (2)
- March 2020 (4)
- February 2020 (1)
- December 2019 (1)
- May 2018 (1)
- March 2018 (2)
- February 2018 (3)
- January 2018 (3)
- November 2017 (3)
- July 2017 (4)
- March 2017 (3)
- February 2017 (5)
- January 2017 (3)
- December 2016 (4)
- November 2016 (6)
- October 2016 (6)
- October 2015 (1)
- September 2015 (1)
- June 2015 (3)
- May 2015 (3)
- August 2014 (1)
- July 2014 (1)
- March 2014 (1)
- February 2014 (1)