Share this
7 Ecommerce Warehouse Best Practices You Can Implement Right Now
by Shipfusion Team on Feb. 10, 2025
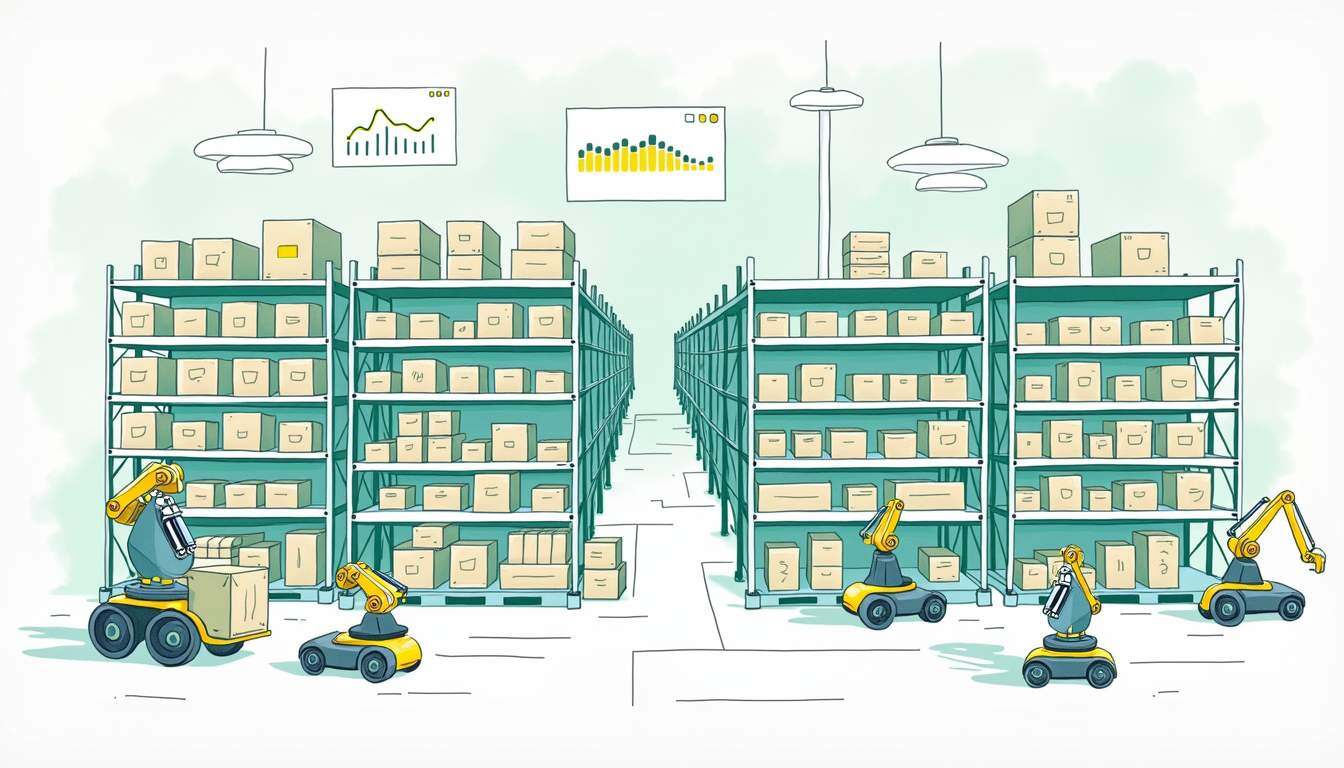
Efficient warehouse operations make all the difference in ecommerce fulfillment. A well-optimized warehouse reduces errors, improves order accuracy, and speeds up shipping times. Implementing the right best practices can enhance efficiency and create a seamless experience for both businesses and customers. Here are seven ecommerce warehouse best practices you can apply today.
1. Optimize Warehouse Layout
A disorganized warehouse leads to wasted time and inefficiencies. Optimizing your layout improves picking speed, reduces congestion, and enhances safety. Start by analyzing order patterns and placing high-demand SKUs closer to packing stations. Create clearly defined zones for picking, packing, and receiving to avoid bottlenecks. Aisles should be wide enough for equipment like forklifts but not so wide that they reduce storage capacity.
Consider implementing slotting techniques such as ABC analysis, where high-demand products are placed in easily accessible locations, while slower-moving items are stored further away. Additionally, use vertical space efficiently by installing high-density shelving or mezzanines to maximize storage capacity without increasing the warehouse or fulfillment center footprint. Regularly review and adjust your layout to match evolving inventory and order volume.
While optimizing your warehouse layout, consider making use of used shelving to maximize efficiency. Such shelves not only provide a cost-effective solution but also offer durability for high-density shelving systems, enhancing overall storage capacity without expanding the warehouse footprint.
2. Implement a Barcode System
Manual inventory tracking is slow and prone to errors. A barcode system automates tracking by ensuring every product is scanned at key touchpoints—when it enters the warehouse, moves between zones, and ships out. Barcodes reduce picking and packing errors while speeding up cycle counts. They also allow for real-time stock visibility, minimizing the risk of miscounts or misplaced inventory.
Using barcodes alongside a scanning system improves inventory accuracy and expedites order processing. Consider integrating 2D barcodes or QR codes, which hold more data than traditional 1D barcodes, providing detailed product information. Additionally, RFID technology can complement barcode systems by allowing bulk scanning of inventory, further reducing manual labor and increasing efficiency.
3. Use Real-Time Inventory Tracking
Real-time inventory tracking prevents stockouts, overstocking, and delays. Using a system that updates stock levels automatically allows for accurate demand forecasting and better inventory control. It also ensures that customers see accurate stock levels on your ecommerce store, preventing overselling or backorders. Real-time data can highlight slow-moving products, enabling better restocking and discounting strategies. Additionally, integrating package tracking software with inventory management can provide end-to-end visibility, ensuring seamless order fulfillment and delivery updates for customers.
To improve accuracy, integrate inventory tracking with automated alerts that notify managers of low stock levels or discrepancies in real-time. Cycle counting, a method where inventory is counted in small sections regularly instead of performing full-scale stock audits, can help maintain ongoing accuracy without disrupting warehouse operations.
4. Prioritize Warehouse Organization
Disorganized warehouses lead to misplaced items, inefficient workflows, and fulfillment errors. Keeping inventory well-organized ensures faster order processing. Use clear labeling for storage locations, maintain a standardized bin system, and keep high-turnover items easily accessible. Implement a routine cleaning and organization schedule to ensure that everything remains in its designated place.
Introduce lean warehousing principles such as the 5S methodology (Sort, Set in Order, Shine, Standardize, Sustain) to improve efficiency and reduce waste. Implementing digital tools like warehouse location mapping can further enhance organization by allowing employees to quickly locate inventory via handheld scanners or mobile apps.
5. Adopt a Warehouse Management System (WMS)
A Warehouse Management System (WMS) streamlines warehouse operations by automating key tasks such as inventory tracking, order fulfillment, and data reporting. A good WMS integrates with ecommerce platforms, ensuring seamless communication between sales and fulfillment. It also provides insights into inventory turnover, picking accuracy, and labor efficiency. By automating processes, businesses can reduce human error, increase productivity, and scale more efficiently.
An effective WMS should include batch tracking capabilities to manage products with expiration dates or lot codes. Features like AI-powered demand forecasting can also optimize stock levels by predicting future sales trends. Integrating WMS with shipping carriers can further enhance operational efficiency by automating label printing and shipment tracking.
6. Train Staff on Best Practices
Technology and organization are only as effective as the people using them. Regular training ensures that warehouse staff follow best practices for picking, packing, scanning, and inventory management. Employees should understand safety protocols, equipment handling, and the importance of accurate data entry. Continuous training also helps workers stay updated on new processes and systems, ensuring the warehouse operates smoothly even as it evolves.
Incorporate cross-training programs to ensure employees can handle multiple tasks, improving flexibility during peak seasons or staff shortages. Providing access to digital training modules and hands-on workshops can reinforce learning and help maintain high operational standards.
7. Monitor and Improve KPIs
Tracking Key Performance Indicators (KPIs) helps identify areas for improvement. Common ecommerce warehouse KPIs include:
- Order Accuracy Rate: Measures how many orders are shipped correctly without errors.
- Picking Efficiency: Evaluates how quickly and accurately items are retrieved from inventory.
- Inventory Turnover: Assesses how often stock is sold and replaced within a given period.
- Fulfillment Speed: Tracks the time taken from order receipt to shipment.
- Return Rate: Analyzes the number of returned items due to incorrect fulfillment or product defects.
Regularly reviewing these metrics highlights inefficiencies, allowing for proactive adjustments. For example, a high order error rate might indicate the need for better scanning technology or additional training. Data-driven decision-making ensures continuous optimization of warehouse operations.
Shipfusion Employs These Ecommerce Warehouse Best Practices and More
Effective warehouse management requires the right combination of strategy, technology, and execution. Shipfusion applies all these best practices—and more—to ensure fast, accurate, and scalable fulfillment for ecommerce businesses. With a proprietary WMS, barcode-enabled tracking, real-time inventory visibility, and expertly trained staff, Shipfusion optimizes warehouse operations at every level.
Shipfusion’s fulfillment solutions include advanced automation, custom warehouse projects, and real-time analytics to help businesses streamline logistics and improve supply chain efficiency. Get a fulfillment partner that prioritizes accuracy and efficiency by contacting us today.
Share this
You May Also Like
These Related Articles
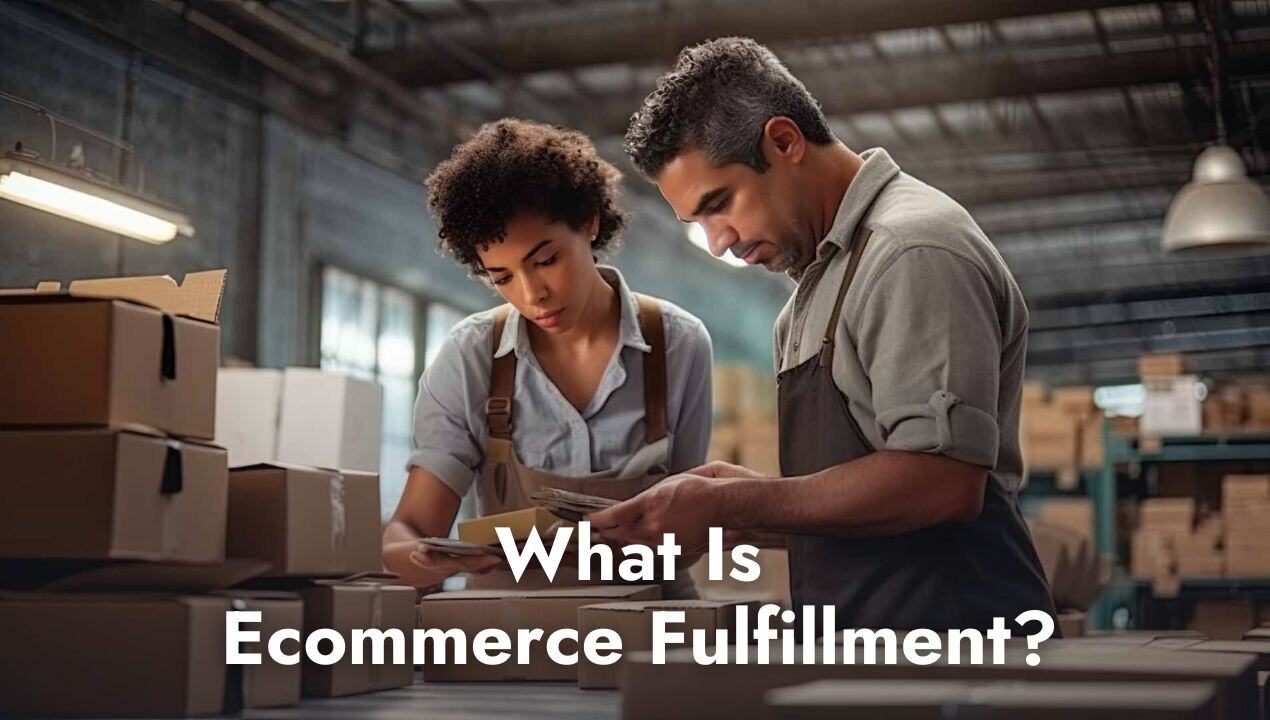
What Is Ecommerce Fulfillment?
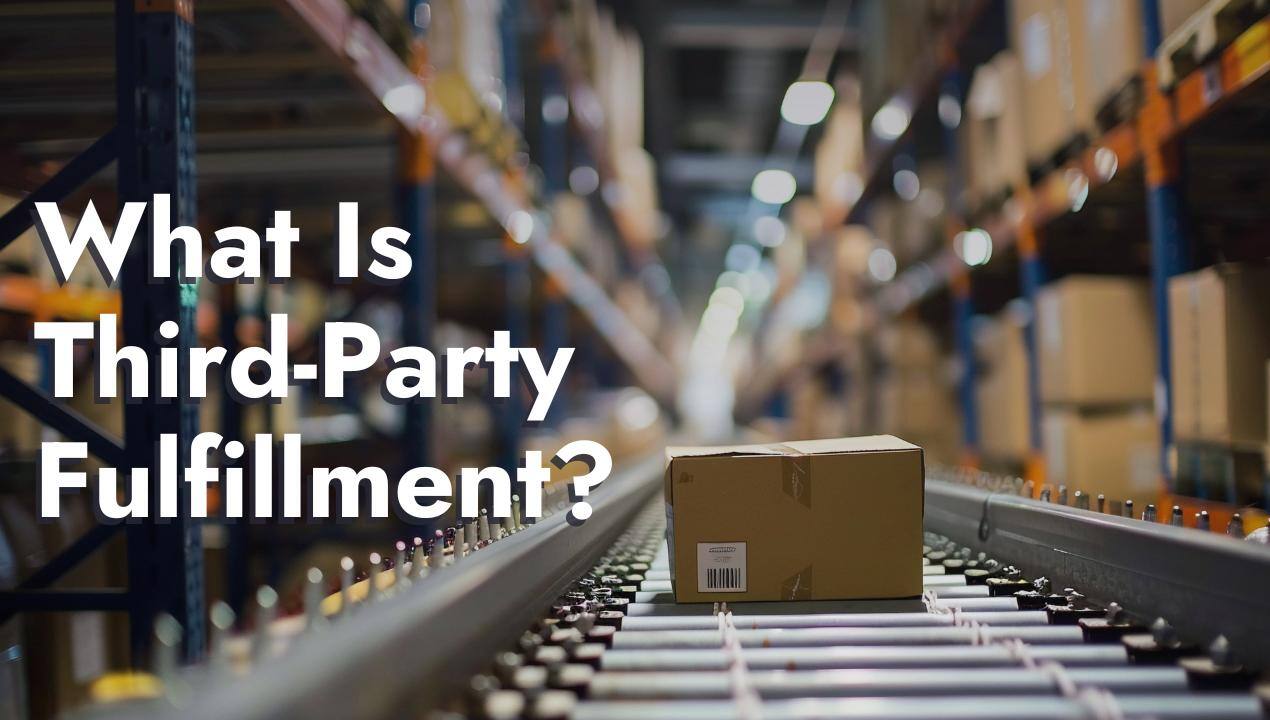
What Is Third Party Fulfillment?
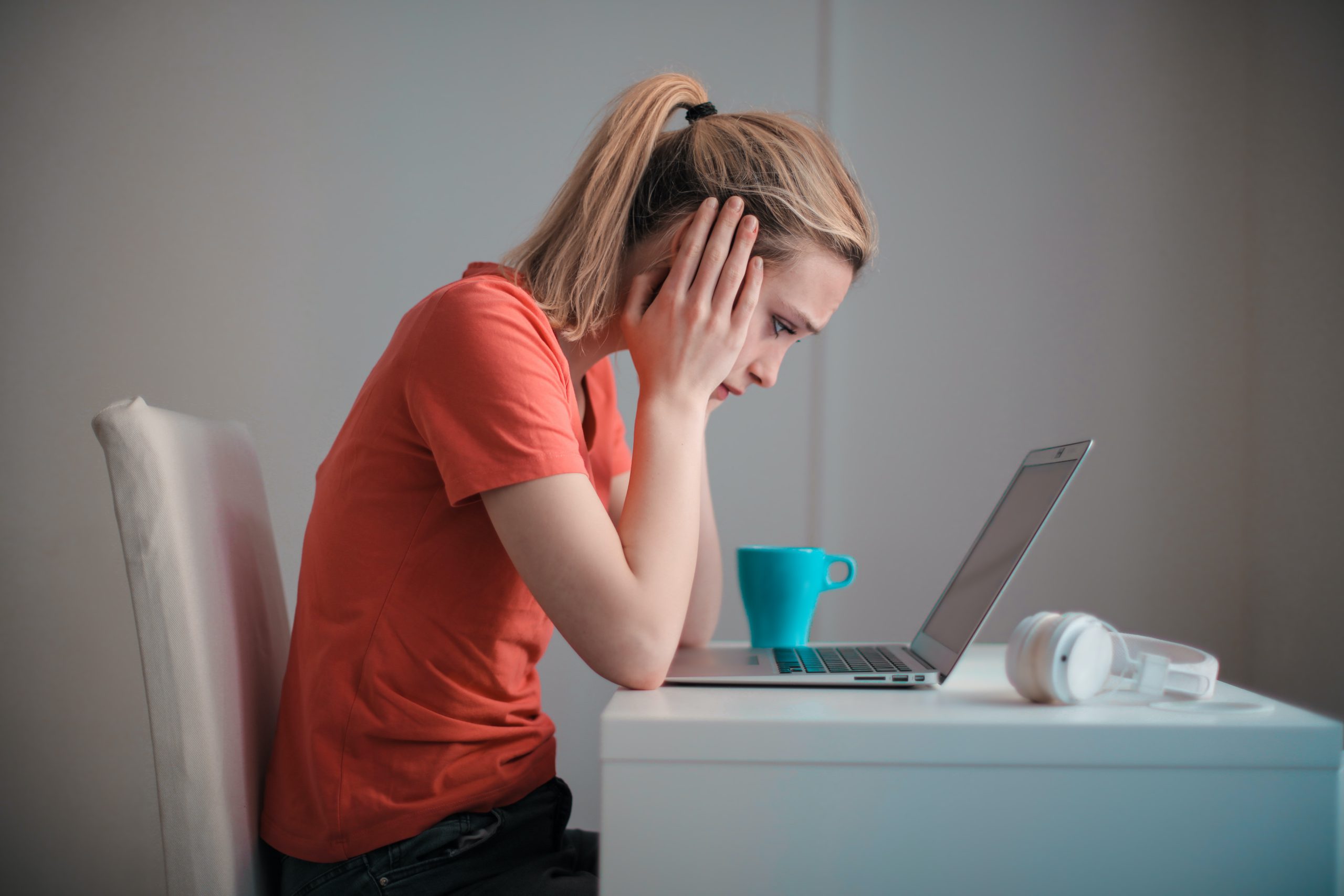
Common Order Fulfillment Issues and How to Solve Them
- April 2025 (19)
- March 2025 (26)
- February 2025 (26)
- January 2025 (37)
- December 2024 (16)
- November 2024 (23)
- October 2024 (22)
- September 2024 (27)
- August 2024 (9)
- July 2024 (8)
- June 2024 (5)
- May 2024 (8)
- April 2024 (8)
- March 2024 (6)
- February 2024 (6)
- January 2024 (5)
- December 2023 (3)
- November 2023 (3)
- October 2023 (5)
- September 2023 (4)
- August 2023 (2)
- July 2023 (1)
- June 2023 (4)
- March 2023 (2)
- October 2022 (1)
- September 2022 (5)
- August 2022 (4)
- July 2022 (7)
- June 2022 (4)
- May 2022 (4)
- April 2022 (6)
- March 2022 (2)
- February 2022 (1)
- January 2022 (3)
- December 2021 (2)
- November 2021 (4)
- October 2021 (2)
- September 2021 (5)
- August 2021 (4)
- July 2021 (4)
- June 2021 (3)
- May 2021 (2)
- April 2021 (3)
- March 2021 (3)
- February 2021 (3)
- January 2021 (2)
- December 2020 (4)
- November 2020 (2)
- October 2020 (4)
- September 2020 (2)
- July 2020 (5)
- June 2020 (4)
- May 2020 (2)
- April 2020 (2)
- March 2020 (4)
- February 2020 (1)
- December 2019 (1)
- May 2018 (1)
- March 2018 (2)
- February 2018 (3)
- January 2018 (3)
- November 2017 (3)
- July 2017 (4)
- March 2017 (3)
- February 2017 (5)
- January 2017 (3)
- December 2016 (4)
- November 2016 (6)
- October 2016 (6)
- October 2015 (1)
- September 2015 (1)
- June 2015 (3)
- May 2015 (3)
- August 2014 (1)
- July 2014 (1)
- March 2014 (1)
- February 2014 (1)