Share this
What Is Cycle Counting In Ecommerce Inventory Management?
by Rin Mosher on May. 6, 2024
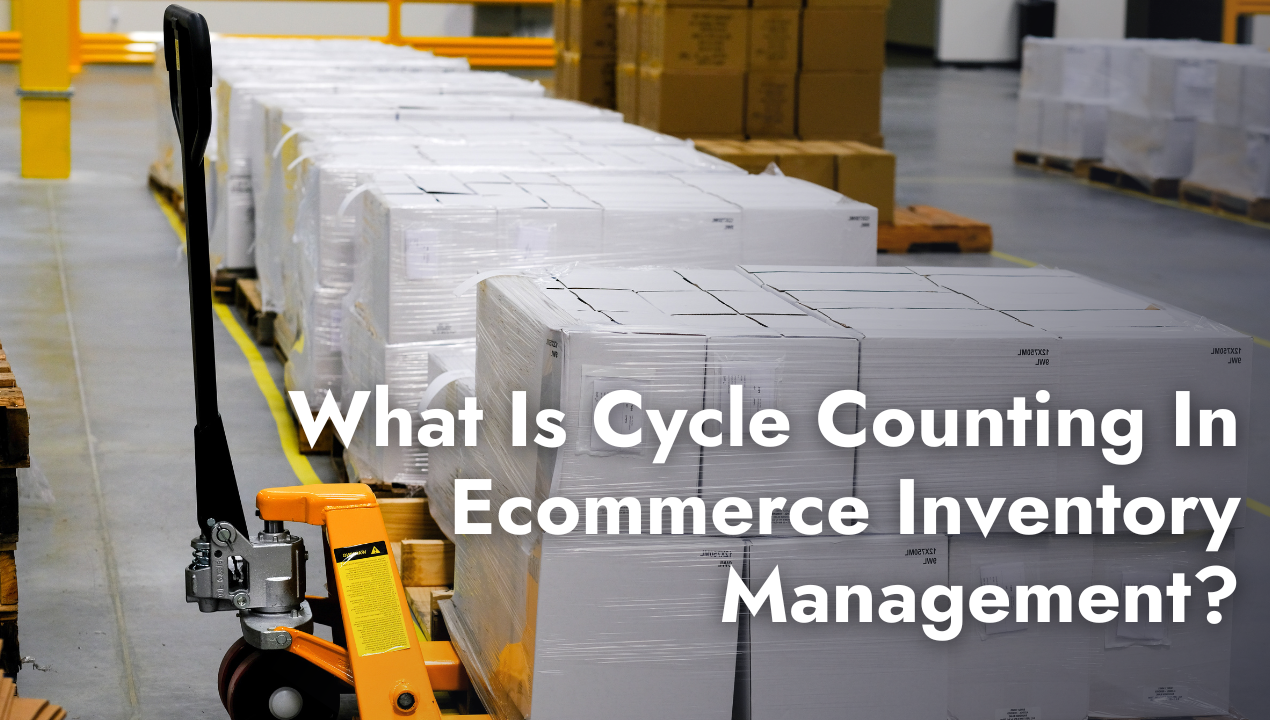
When it comes to ecommerce inventory management, there’s more than one way to make sure your stock count is accurate. With the full process of counting inventory being both time and resource-intensive and disruptive to everyday operations, many ecommerce businesses use the cycle counting method as a way to stay on top of inventory totals while maintaining operational productivity. But what is cycle counting, and how does it fit in with inventory management as a whole? Should it be used as a stand-alone strategy, or in tandem with full inventory counts?
This article will discuss what cycle counting is, why ecommerce businesses use this method, the different types of cycle counting that exist, and how it can optimize your current inventory management practices.
What Is Cycle Counting?
Cycle counting is a continuous process that involves regularly counting small portions of inventory at a time. Where full physical inventory counts usually require entire operations to shut down for the day, the piece-by-piece approach of cycle counting allows businesses to maintain regular operations while still keeping track of inventory accuracy.
Cycle Counting vs. Physical Inventory Counting
It’s important to recognize that cycle counting is different from a traditional full physical inventory count. Both methods are used to ensure the accuracy and integrity of inventory records, but they differ in their approach.
As we’ve already established, cycle counting is a piece-by-piece process that occurs continuously over an extended period of time. For example, a business may choose to count 10% of its inventory every week or rotate through different sections each cycle, depending on which cycle counting method is used (which we’ll discuss further on in this article). Doing so allows for some visibility into stock without causing the same large-scale disruption as a full physical inventory count.
In contrast, full physical inventory counts involve stopping most, if not all, warehouse operations in order to count every single item in stock. These counts are typically conducted annually or biannually and require significant planning and manpower. While they provide a complete snapshot of inventory at a specific point in time, this method can be very disruptive to daily operations and may lead to temporary reductions in productivity.
Full counts are necessary for comprehensive data on stock levels but must be managed carefully to minimize their impact on business continuity. Without an interim measure like cycle counting, you would need to either bear the operational implications of frequent full counts or conduct them less often and risk having inaccurate inventory data.
Why Cycle Counting Is Beneficial to Inventory Management
Cycle counting is intended to complement existing inventory counting practices. Implementing it alongside less frequent full counts can have many benefits in terms of both time and cost savings, and combining these methods results in more accurate inventory records. Scheduled checks are an opportunity to consistently monitor inventory for overreported or underreported quantities. The sooner discrepancies are identified, the sooner they can be fixed, and the less of an impact they have on overall inventory accuracy every time a full count is conducted.
Putting a little extra time and effort into frequent cycle counting enables businesses to take action on problems before they grow into larger issues with larger financial implications. For instance, cycle counting can catch surpluses in actual stock from what’s recorded in a warehouse management system. If left unaddressed, this could lead to higher holding costs, tied-up capital, and wasted storage space.
By proactively identifying this example issue through cycle counting, a business is able to adjust its ordering process to prevent excess stock and save money in the long run. On the other side of the coin, cycle counting can also improve warehouse processes by uncovering patterns in shrinkage.
Types of Cycle Counting
There are actually multiple different methods of cycle counting that ecommerce businesses can use to optimize their inventory management, depending on their needs and operations. Some of the most common methods include:
ABC Cycle Counting
The ABC cycle counting method reviews items based on their value. All inventory is placed into one of three categories – A, B, and C – based on their value and demand, and how often products are audited is dependent on their category. This method is guided by the Pareto principle, which asserts that approximately 80% of effects come from 20% of the causes. In the context of inventory, this often means that a small percentage of items accounts for the majority of the inventory’s value.
Class A Inventory
Class A inventory items are those that have the highest dollar value or demand, aligning with the Pareto principle by accounting for the majority of the inventory’s value. Because these items are usually the most popular and financially significant, discrepancies in their stock levels can quickly lead to significant operational and financial impacts. With each individual unit holding such high importance, SKUs in this top class are counted on a monthly or even weekly basis.
Class B Inventory
Class B inventory consists of products with average-to-high dollar values or levels of demand. This category usually consists of a higher number of individual SKUs than the ‘A’ group, but items in this category aren’t quite as in demand or financially significant (but are still important to revenue). Class B inventory is counted less frequently – usually every quarter – to ensure accuracy while optimizing resource use.
Class C Inventory
Class C consists of products that make up the bulk of total inventory and are characterized by the lowest demand and sales frequency. While each individual Class C item may not be counted as frequently as more valuable items, the large volume of these items means that inventory counts still need to be conducted to prevent overstocking and underutilization. Reviews typically occur once or twice a year, although this can vary based on operational requirements and inventory turnover rates.
Usage-Based Cycle Counting
Every time a pallet of inventory is handled or moved, there's a risk of accidental miscounts, misplaced items, or damage — any of which can lead to inaccurate stock counts. Usage-based cycle counting, also known as frequency cycle counting, addresses this by focusing on items that are frequently moved and accessed throughout the supply chain. This method uses sales data, picking history, and product velocity to identify which items are accessed most frequently and should be re-counted accordingly.
Usage-based inventory cycle counting works well in situations where a relatively small number of products make up the majority of sales. It allows for more frequent and accurate counting of these high-demand items, reducing the risk of stockouts or overstocking as well as the time and resources that might be spent counting less popular products. For these high-demand products, counts might occur as often as monthly or even weekly, depending on the business.
There are some challenges with this method, though, as it may overlook slower-moving SKUs that are still important for maintaining overall inventory levels. It also relies heavily on accurate and up-to-date sales data, which can be difficult to obtain in real-time.
Random Sample Cycle Counting
Random sample cycle counting selects inventory items for counting at random, without considering their value, frequency of use, or other distinguishing characteristics. This method is particularly effective in reducing selection bias, a common issue in other cycle counting methods where specific items are counted more or less frequently based on predefined criteria. For example, in ABC cycle counting, higher-value items are counted more often, potentially leading to outdated data for items that are valued less. Similarly, usage-based counting may overlook less frequently accessed items that are still important.
By giving each item an equal chance to be counted, random sampling ensures a more representative sample of the overall inventory. This method is particularly useful for businesses whose inventory includes many similar items — meaning they are alike in type, usage, size, or value. In these settings, missing an item during one count has minimal impact because each item is quite similar to others and serves a similar function. This interchangeability makes the counting process more forgiving and helps ecommerce businesses maintain an accurate picture of stock levels without the need for perfect count accuracy on every single item.
While random sample cycle counting minimizes bias and simplifies inventory checks, it can introduce challenges in accuracy when dealing with a diverse range of products instead of similar items. The random nature of item selection means there's no guarantee of evenly distributed counts over time, which might lead to certain SKUs being counted more frequently than others. This inconsistency can result in a skewed representation of stock levels within a diverse inventory, where some items are overrepresented and others underrepresented.
Two techniques can be used in random sample cycle counting: constant population counting and diminished population counting.
Constant Population Counting
With constant population counting, the same number of items are counted each time a count is performed – if 500 items are counted during the first cycle, then 500 items will also be counted during the second cycle. No record is kept of which specific products have and haven’t been reviewed, which keeps things truly random. But it also risks counting some items more frequently than others by plain chance.
Diminished Population Counting
Diminished population counting aims to prevent the overcounting risk posed by constant population counting by excluding items after they’ve been counted once. The items that will be audited are still randomly selected, but from a gradually decreasing pool of inventory that hasn't been counted yet. This method ensures a more equitable distribution of counts over time. The main drawback of this method is that it requires a lot of planning and coordination, particularly in managing the decreasing inventory pool, which can be time-consuming and difficult to implement without the right ecommerce inventory management technology.
Our inventory management calculator comes equipped with relevant formulas you’ll need to stay on top of inventory accuracy. Download it here:
Free Inventory Management Calculator
Best Practices for Cycle Counting
Cycle counting is an exact science that requires diligence to work. Rushing it can compromise the accuracy – and reliability – of your results. Follow the best practices outlined below to ensure everything you invest in the process proves worthwhile.
Choose the Right Counting Method
Each cycle counting method comes with its own set of benefits, risks, and ideal use cases. ABC cycle counting is generally the most popular approach with ecommerce businesses, as it recognizes the cost stakes that drive businesses to implement inventory management processes in the first place. Prioritizing 'A' SKUs with higher dollar values and levels of demand won't eliminate inaccuracy, but it can lessen the impact that inventory mistakes can have on your ability to fulfill orders for popular items, and, ultimately, your revenue.
With that being said, the other counting methods may better suit your business, depending on your specific needs. Start by considering the inventory itself – how much you have, how frequently it moves, and how quickly it needs to be replenished.
For example, ecommerce stores that focus on selling lower-cost items with even popularity might have a hard time making the ABC counting method work.
Also consider your current operational bandwidth. Do you have the means to organize and count inventory based on usage? Will your team be able to reliably track which products have and haven’t been counted using the diminished population system? Both of these strategies have value in given use cases but are ultimately only worthwhile if their specific benefits are needed.
Use the Inventory Accuracy Rate to Track Changes
Tracking data in the form of key performance indicators can illustrate whether you’ve established the right cycle counting system for your warehouse, and inventory accuracy rate is among the most telling supply chain KPIs to watch. The inventory accuracy rate highlights discrepancies in inventory by considering the total quantity of products in stock against the quantity counted. The sum is expressed as a percentage, with 100% indicating a perfect match between recorded and actual inventory.
Inventory Accuracy Rate = (Matched Inventory / # of Items Counted) x 100
Most businesses maintain less-than-perfect, but steady inventory accuracy rates between 65% and 90%. Inventory accuracy rates can provide insight into how your fulfillment and warehouse management operations compare to industry averages and against your own business goals. While this rate can be calculated manually, partnering with a reliable ecommerce fulfillment services provider that has comprehensive inventory reporting tools makes doing so unnecessary, as you’d be able to view your inventory data in real-time. Use this KPI and other reporting metrics to gauge the effectiveness and consistency of your counting process on an ongoing basis.
Count Consistently
Cycle counting isn’t just a one-time window into inventory totals – it’s a tool capable of ongoingly informing warehouse management practices. You’ll get the most value by conducting regular cycle counts, ideally on a set schedule. Count frequency depends on how many unique SKUs are to be audited every year, as well as the specific cycle counting system you use. For instance, if a company had 100 SKUs and wanted to count each one once a year, they would need to count 8-9 SKUs per month or 2-3 per week.
Considerations should also be made for the seasonality of certain products and their demand fluctuations.
Reconcile Discrepancies
If your business has only been performing annual physical counts, it’s likely that cycle counting will uncover inconsistencies in some form, such as incorrect SKU locations or misreported unit quantities. What you choose to do with this information will determine the value you get from cycle counting. Use it to identify operational flaws and make changes accordingly. If large discrepancies are consistently uncovered, for example, it might be worth taking further action, like auditing processes for human error, reviewing policies, or reassessing relationships with manufacturers and shipping carriers.
Simplify Your Inventory Management With Shipfusion
While it requires less time than a full physical count, cycle inventory counting is still a burdensome process. If you’re looking to minimize the resources it drains from your team, Shipfusion offers a stress-free solution.
As an industry-leading third-party logistics (3PL) company, we’re well-equipped to streamline this aspect of inventory management for you. Partnering with Shipfusion means benefiting from real-time visibility and transparency into stock levels, including SKU continuity reports, back order notifications, count/adjustment entries, and so much more. Reach out to a member of sales today to learn more about what Shipfusion can do for your ecommerce business.
Share this
You May Also Like
These Related Articles
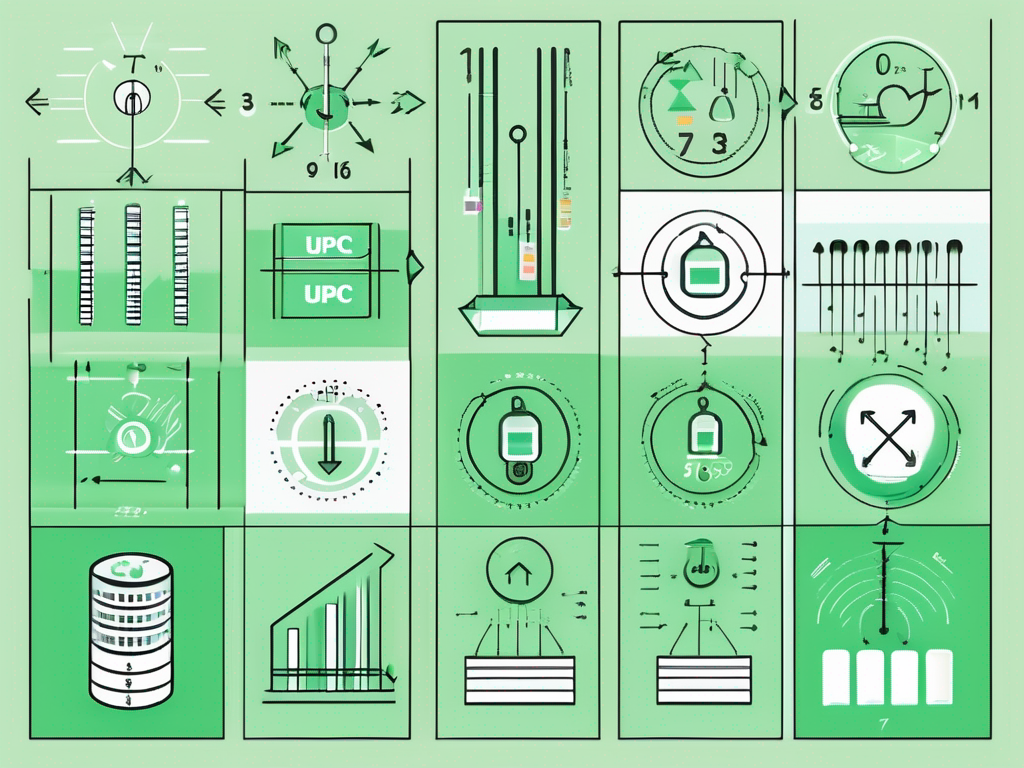
UPC Symbols Decoded: What They Are and Why They’re Essential
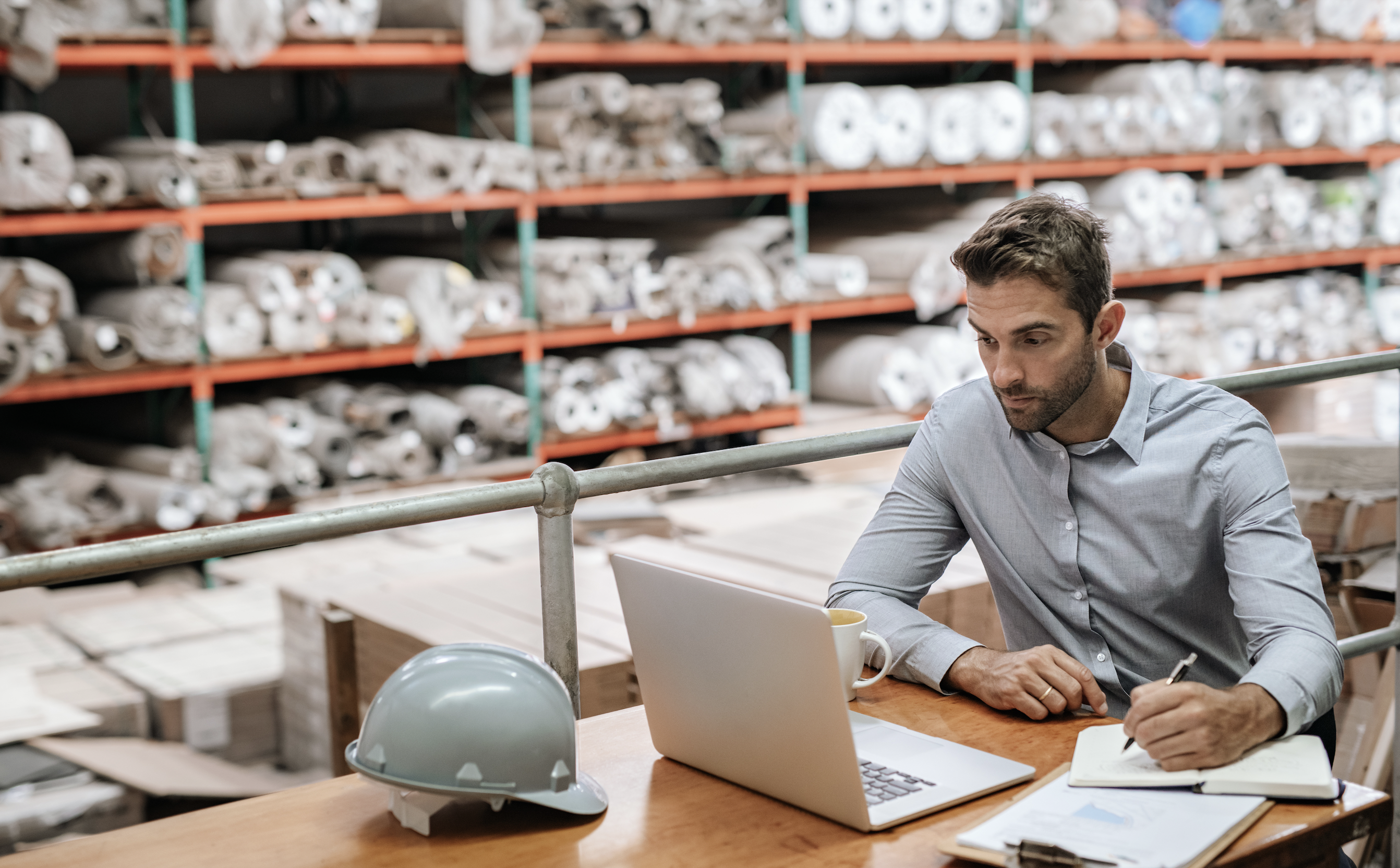
Your Guide on How to Create an Inventory Strategy
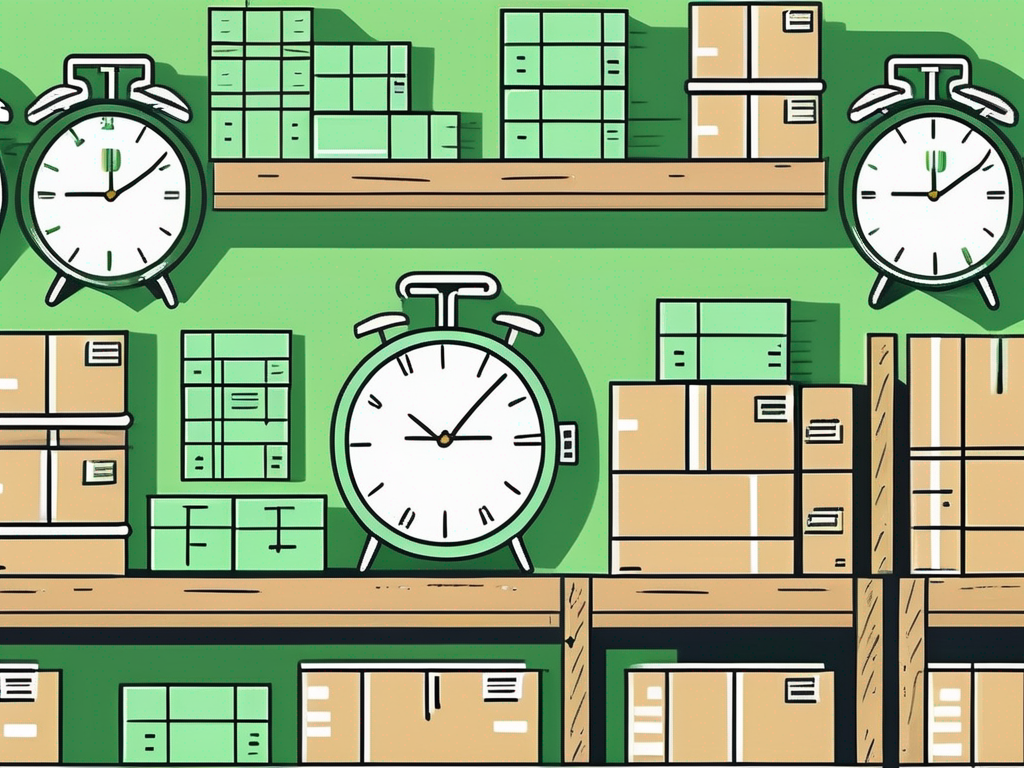
Lowering Carrying Costs Associated with Investments In Inventory
- April 2025 (18)
- March 2025 (26)
- February 2025 (26)
- January 2025 (37)
- December 2024 (16)
- November 2024 (23)
- October 2024 (22)
- September 2024 (27)
- August 2024 (9)
- July 2024 (8)
- June 2024 (5)
- May 2024 (8)
- April 2024 (8)
- March 2024 (6)
- February 2024 (6)
- January 2024 (5)
- December 2023 (3)
- November 2023 (3)
- October 2023 (5)
- September 2023 (4)
- August 2023 (2)
- July 2023 (1)
- June 2023 (4)
- March 2023 (2)
- October 2022 (1)
- September 2022 (5)
- August 2022 (4)
- July 2022 (7)
- June 2022 (4)
- May 2022 (4)
- April 2022 (6)
- March 2022 (2)
- February 2022 (1)
- January 2022 (3)
- December 2021 (2)
- November 2021 (4)
- October 2021 (2)
- September 2021 (5)
- August 2021 (4)
- July 2021 (4)
- June 2021 (3)
- May 2021 (2)
- April 2021 (3)
- March 2021 (3)
- February 2021 (3)
- January 2021 (2)
- December 2020 (4)
- November 2020 (2)
- October 2020 (4)
- September 2020 (2)
- July 2020 (5)
- June 2020 (4)
- May 2020 (2)
- April 2020 (2)
- March 2020 (4)
- February 2020 (1)
- December 2019 (1)
- May 2018 (1)
- March 2018 (2)
- February 2018 (3)
- January 2018 (3)
- November 2017 (3)
- July 2017 (4)
- March 2017 (3)
- February 2017 (5)
- January 2017 (3)
- December 2016 (4)
- November 2016 (6)
- October 2016 (6)
- October 2015 (1)
- September 2015 (1)
- June 2015 (3)
- May 2015 (3)
- August 2014 (1)
- July 2014 (1)
- March 2014 (1)
- February 2014 (1)