Share this
How to Calculate Work In Process Inventory In Ecommerce
by Rin Mosher on Jul. 24, 2024
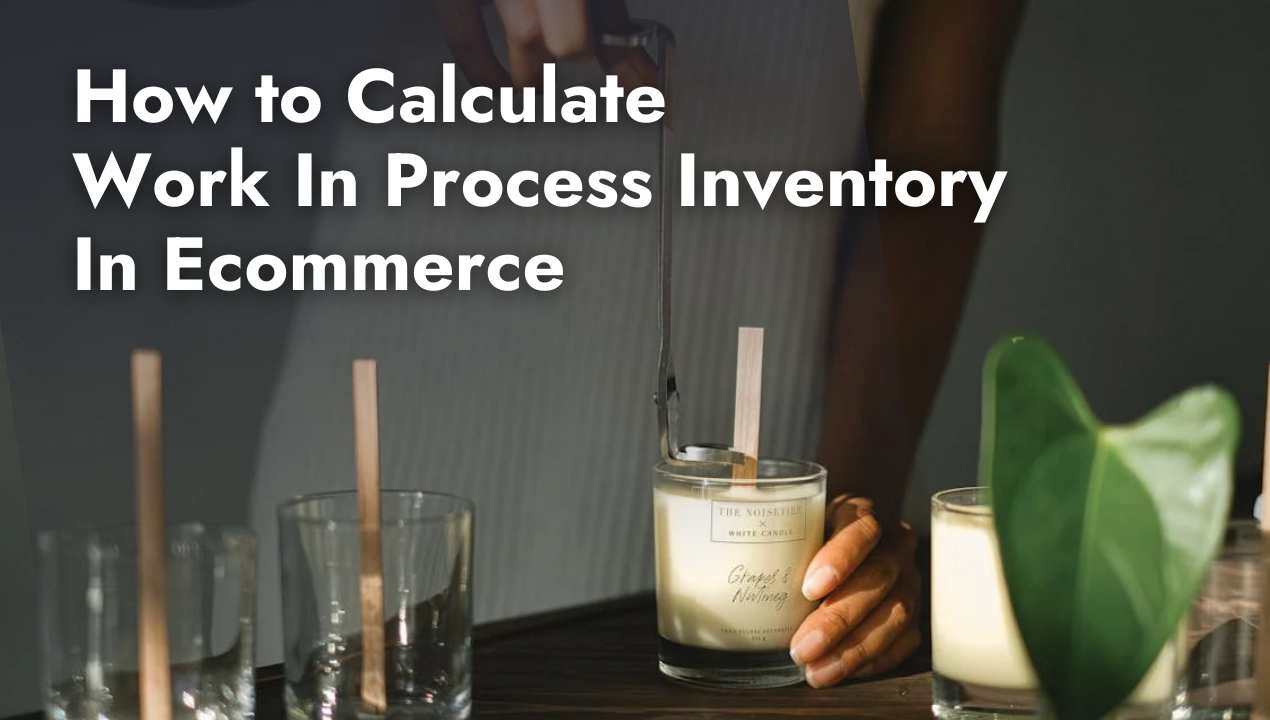
Handmade, custom, or otherwise unique ecommerce products require careful assembly and meticulous inventory tracking. Before these products are fully assembled, they're known as Work In Process (WIP) inventory. Failing to keep track of this type of stock can impact warehouse space, holding costs, and overall operational efficiency and profitability – and knowing how to calculate the value of work in process inventory is key to managing these factors effectively.
This article will provide a comprehensive guide to understanding WIP inventory levels. We'll break down the concept, explore its importance in ecommerce operations, and explain how to calculate work in process inventory for your own production process.
What Is Work In Process (WIP) Inventory?
Work In Process (WIP) inventory is an accounting designation used to define products midway through the manufacturing process. WIP represents the combined value of all materials, labor, and overhead costs associated with the unfinished products and is classified as a current asset on the company's balance sheet.
For ecommerce businesses, it provides a way to account for the investments in materials and labor that have not yet resulted in finished goods ready for sale. Proper WIP ecommerce inventory management is crucial for optimizing production workflows, controlling costs, and improving overall operational efficiency.
WIP inventory accounting is worthwhile if you procure raw materials to:
- Assemble products yourself
- Source materials from multiple suppliers for assembly by a manufacturer
- Partner with a single supplier/manufacturer that sources and assembles materials on your behalf
Work In Process vs. Work In Progress Inventory
If you've been exploring web results for “How to calculate work in process inventory,” you've probably noticed an inconsistency in terminology. Some articles use "work in process," while others refer to "work in progress." This might leave you wondering if there's a difference between the two terms. The short answer is: not really.
Both “work in process” and “work in progress” refer to partially completed goods. It is worth noting, however, that the term “work in progress inventory” is sometimes preferred for projects or products with longer production cycles. For instance, construction projects or custom-made machinery might be referred to as “work in progress inventory” due to their extended timelines.
On the other hand, “work in process” is more commonly used in manufacturing contexts where goods move through production stages relatively quickly. The key is to be consistent in your usage within your organization to avoid confusion.
What Is Included In WIP Inventory?
Although businesses have the final say over which factors they want to consider in the WIP inventory calculation process, most include raw materials, direct labor costs, and manufacturing overhead in their calculations. Overhead can be similarly broad in scope – it may include costs such as equipment depreciation, utilities, and facility maintenance, or it may be limited to specific production-related expenses.
Some businesses may include other factors, such as subcontractor costs for outsourced work or quality control expenses. The inclusion of these elements depends on the nature of the production process and the company's accounting policies.
Let’s illustrate with an example:
A cosmetics company manufactures a popular line of lipsticks from its assembly plant in South Carolina. The raw materials required to make every unit – wax, pigments, and packaging – are sourced from various suppliers across the country.
The manufacturing process involves several stages, from melting and mixing the wax and pigments to molding and packaging the final product. This necessitates the consideration of overhead costs such as equipment maintenance, utilities, and factory rent. The company also factors in direct labor costs, which include wages for workers directly involved in the production process.
This lipstick company’s WIP inventory management is particularly important because its production cycle isn't instantaneous. It takes time to transform raw materials into finished lipsticks, and during this process, value is continuously added to the product.
How WIP Fits In With Other Types of Inventory
Inventory is generally classified into three groups: raw materials inventory, WIP inventory, and finished goods inventory, which are defined as follows.
Raw Materials Inventory: Raw materials are the unprocessed components and substances used to create finished products. These include items like wood, metal, fabric, or chemicals that have not yet been altered or incorporated into the manufacturing process.
Work In Process Inventory: Any products between the stages of raw materials and finished goods can be considered work in process inventory. WIP includes partially finished goods, components in various stages of assembly, and products awaiting final touches or quality control checks.
Finished Goods Inventory: Finished goods have gone through every stage of the manufacturing process and are ready to be stored as inventory until sale.
No product can be in more than one of the above categories at the same time. An item's progress to completion may influence its value in WIP calculations. It ultimately comes down to the specific accounting method used – we'll go into more detail on this later on.
How to Calculate Work In Process Inventory
Calculating work in process inventory is a multi-step process that involves considering several business-specific inputs. To use the WIP formula, you'll need balance sheets and expense records from this accounting period and the one before it.
Work In Process Inventory Formula
Beginning WIP Inventory + Manufacturing Costs – Cost of Goods Manufactured = Ending WIP Inventory
1. Find Beginning Work In Process Inventory
Beginning WIP inventory encompasses all inventory from the prior accounting period. It is simply the last cycle’s ending WIP inventory carried over, representing what the business is beginning its new period with.
2. Determine Manufacturing Costs
Work in process inventory manufacturing costs can be valued in different ways depending on the product, production process, and business at hand. In every case, it’s meant to account for the resources tied up in partially completed goods. Here are two of the most common methods used to measure manufacturing costs for items considered WIP:
Percentage of Completion
WIP is often quantified by the percentage of completion an item has reached in production. Total raw material, labor, and overhead costs incurred to date are adjusted so that units closer to completion have more value added to them compared to those just starting the production process. This nuanced approach allows for a more accurate representation of the true value of WIP inventory at any given time.
Back to the lipstick example from earlier, a percentage of completion-based system would consider batches of lipsticks ready for packaging worth more than the batches still being mixed.
The percentage of completion method works well for standardized products with consistent production steps. It's easy to establish increments like 25%, 50%, 75%, and 100% completion based on where an item is in production, where 100% represents the total manufacturing cost, inclusive of raw materials, labor, and overhead.
Job Order Costing
WIP manufacturing costs can also be calculated using a job-based system, which involves tracking the costs used to create individual products. It’s far more in-depth and, therefore, less common than the percentage of completion method.
Granular expense calculations like these make the most sense for custom offerings. A maker of custom phone cases, for instance, might use job-based costing to track the expenses for and maintain the profitability of each of its personalized orders.
3. Calculate COGM
It’s important to note that manufacturing costs and Cost of Goods Manufactured (COGM) aren’t the same thing. Manufacturing costs, the structuring of which we explained in the section above, include the cost of raw materials, labor, and overhead allocated to production. Cost of Goods Manufactured represents the total cost of goods completed during a specific period.
In other words, only the costs associated with completed goods are included in COGM, while manufacturing costs encompass all production-related expenses, regardless of whether the goods are finished or still in progress. Manufacturing costs and COGM will only ever be the same value when there is no WIP inventory left at the end of the accounting period.
Determine your COGM using the formula below:
Cost of Goods Manufactured (COGM) = Manufacturing Costs + Beginning WIP Inventory – Ending WIP Inventory
How to Find Ending Work In Process Inventory Using Work In Process Inventory Formula
With beginning WIP inventory, manufacturing costs, and COGM identified, you’ll have everything you need to calculate work in process inventory for the end of this accounting period.
Plug each value into the work in process inventory formula shared earlier:
Beginning WIP Inventory + Manufacturing Costs – COGM = Ending WIP Inventory
Keep in mind that this calculation isn’t exact. The above formula doesn’t consider factors such as waste, spoilage, scrap, or normal production losses. It's also worth noting that this method relies on the accuracy of the beginning WIP inventory level, manufacturing costs, and COGM figures recorded. Any errors in these inputs will result in an inaccurate ending WIP inventory calculation, which is why maintaining meticulous records and regular cycle counting is pivotal.
How to Find Work In Process Inventory With Examples
Let's walk through practical examples to illustrate how to calculate ending Work In Process (WIP) inventory in an ecommerce setting:
Example 1: Online Clothing Retailer
Suppose you run an online clothing retailer specializing in handmade dresses. At the beginning of the month, you had the following balances.
Beginning WIP Inventory: $40,000 (existing fabric, thread, buttons, and partially sewn dresses)
Manufacturing Costs for the Month: $150,000 (expenses for additional materials, labor costs for tailors, and overhead costs such as utilities and rent)
COGM: $130,000 (cost of completed dresses that were moved to finished goods inventory)
Applying our formula:
Ending WIP Inventory = $40,000 + $150,000 - $130,000 = $60,000
This $60,000 represents the value of partially completed dresses still in production at month's end. This might include dresses that are cut but not sewn, dresses that are sewn but not yet fitted, and dresses awaiting final touches like buttons or zippers.
Example 2: Custom Jewelry Ecommerce Store
Consider a custom jewelry ecommerce store that creates bespoke necklaces and bracelets. The store wants to calculate its ending WIP inventory for the quarter with the following figures.
Beginning WIP Inventory: $25,000 (includes raw materials like gold, silver, gemstones, and partially completed jewelry pieces)
Manufacturing Costs for the Quarter: $200,000 (expenses for additional materials, skilled labor for artisans, and overhead costs such as workshop rent and utility bills)
COGM: $180,000 (cost of completed jewelry pieces that were moved to finished goods inventory)
Calculating ending WIP:
Ending WIP Inventory = $25,000 + $200,000 - $180,000 = $45,000
The sum of this WIP inventory calculation indicates that at the quarter's end, the business had $45,000 worth of unfinished jewelry items in various stages of production. This might include necklaces that are strung but not clasped, bracelets that are half-assembled, and jewelry pieces awaiting polishing or engraving.
Why Is Work In Process Inventory Important?
WIP inventory isn’t necessarily a supply chain KPI, but it can similarly enhance operational health when tracked consistently. Tracking WIP inventory can help your ecommerce business in the following areas:
Flexibility and Liquidity
WIP inventory management is important because WIP inventory represents unfinished goods taking up space that could otherwise be used for products that are ready to be sold. An excess amount of WIP generally means higher carrying costs and excess unrealized capital.
Managing WIP inventory is important because unfinished goods take up space that could otherwise be used for inventory ready to sell. More WIP generally means higher carrying costs and excess unrealized capital, which is why you want to minimize excess amounts as much as possible.
Production Efficiency
Monitoring WIP gives you the opportunity to identify and address manufacturing bottlenecks head-on. For instance, excess partially finished goods in one particular product line may indicate a unique assembly challenge that needs to be addressed or a need for more resources at a particular stage of production. Early detection of issues like these can make a big difference in long-term efficiency – and supply chain resilience as a result.
More Detailed Financial Reporting
The additional bookkeeping associated with WIP inventory tracking pays off in attaining greater financial insight. It inclines businesses to scrutinize their accounting process and provides a more granular view of production costs. This detailed understanding can lead to more accurate pricing strategies and better-informed business decisions.
Less Exposure to Risk
High levels of WIP inventory represent not only production inefficiency but also greater exposure to unnecessary liabilities and costs. WIP inventory is essentially an unrealized investment. The longer businesses wait to convert WIP into finished goods, the greater the risk of obsolescence, damage, or market shifts that could render the investment less valuable.
Speedy manufacturing cycles are particularly important for Consumer Packaged Goods (CPG) with expiration dates like food products, beverages, and pharmaceuticals. Adopting a FIFO over LIFO inventory valuation method can help mitigate these risks by ensuring older inventory is sold first, but the shelf life warehouses and fulfillment centers have to work with is first determined by production speed.
Work In Process Inventory On Your Balance Sheet
The balance sheet is where work in process inventory starts to confuse most business owners. As we’ve already established, WIP products aren’t finished inventory because they haven’t been completed yet. But they’re also beyond the stage of being just raw materials. It makes the most sense to split the “inventory” section of the balance sheet in two, with one section for goods still in production and one for those that are finished and ready for storage and sale.
You then debit the WIP account and credit the raw materials as goods move from one stage to the next. When production is complete, items are considered “finished goods” under inventory. Companies generally want to convert products to this final stage as efficiently as possible because it is where prior investments become realized with profit.
The manufacturing costs of finished goods are attributed to Cost of Goods Sold (COGS) after sale.
Don't Stop at Learning How to Calculate Work In Process Inventory
Now that you know how to calculate Work In Process Inventory, you're one step closer to effectively managing inventory at large. The right third-party logistics (3PL) partner can make all the difference in that endeavor. So why go with anything short of five-star service from Shipfusion?
Our software-enabled solutions streamline storage and fulfillment processes, providing real-time visibility into inventory levels, order status, and shipping rates. Set up custom reporting, forecasting, and inventory stock level alerts to stay up to date on what matters and let us handle the rest. Learn why we're the best 3PL in North America and contact a team member today.
Share this
You May Also Like
These Related Articles
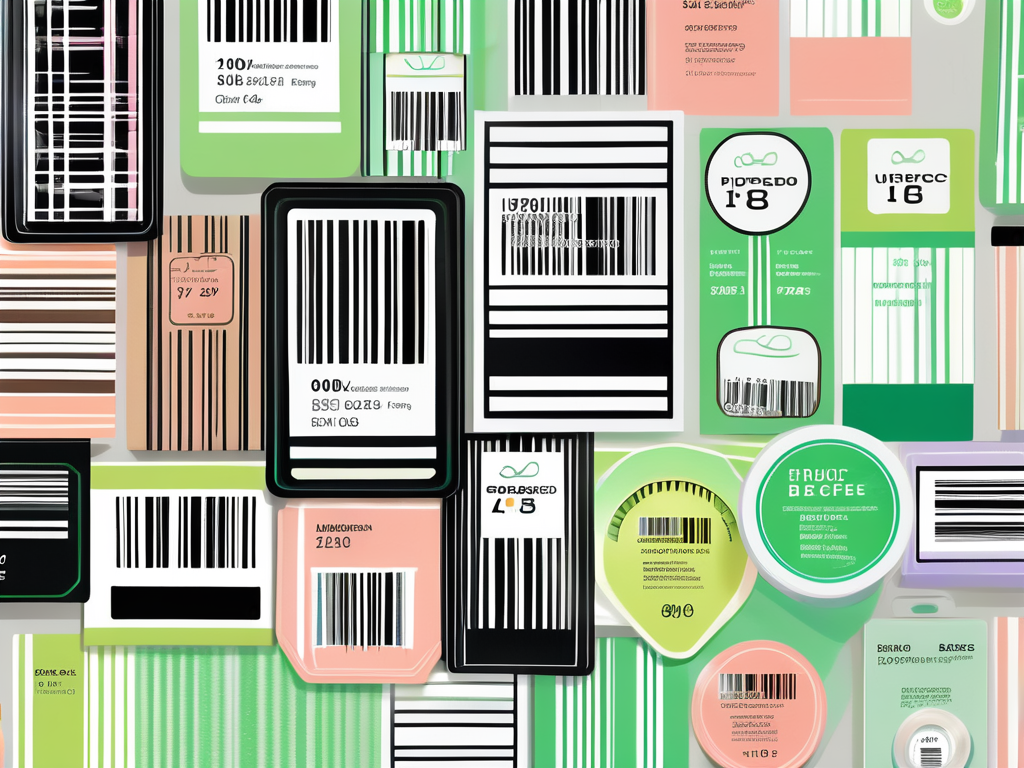
Product UPC Barcode: What It Is and Why It Matters In Ecommerce
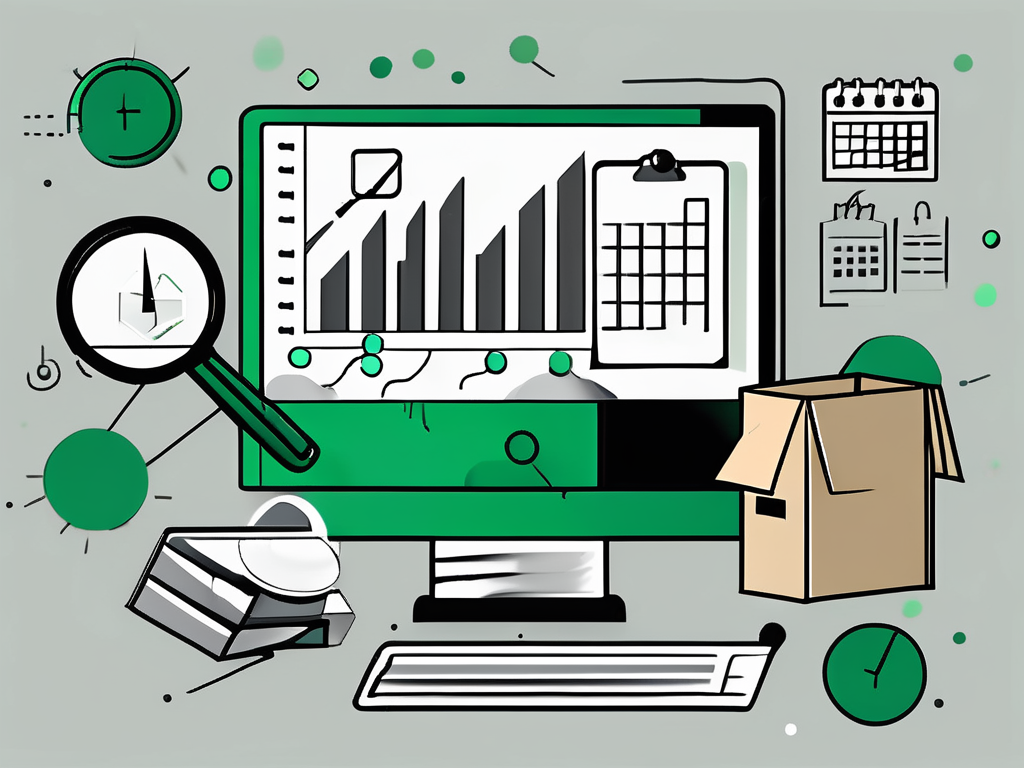
7 Lesser-Known Inventory Forecasting Hacks for Wholesale Orders
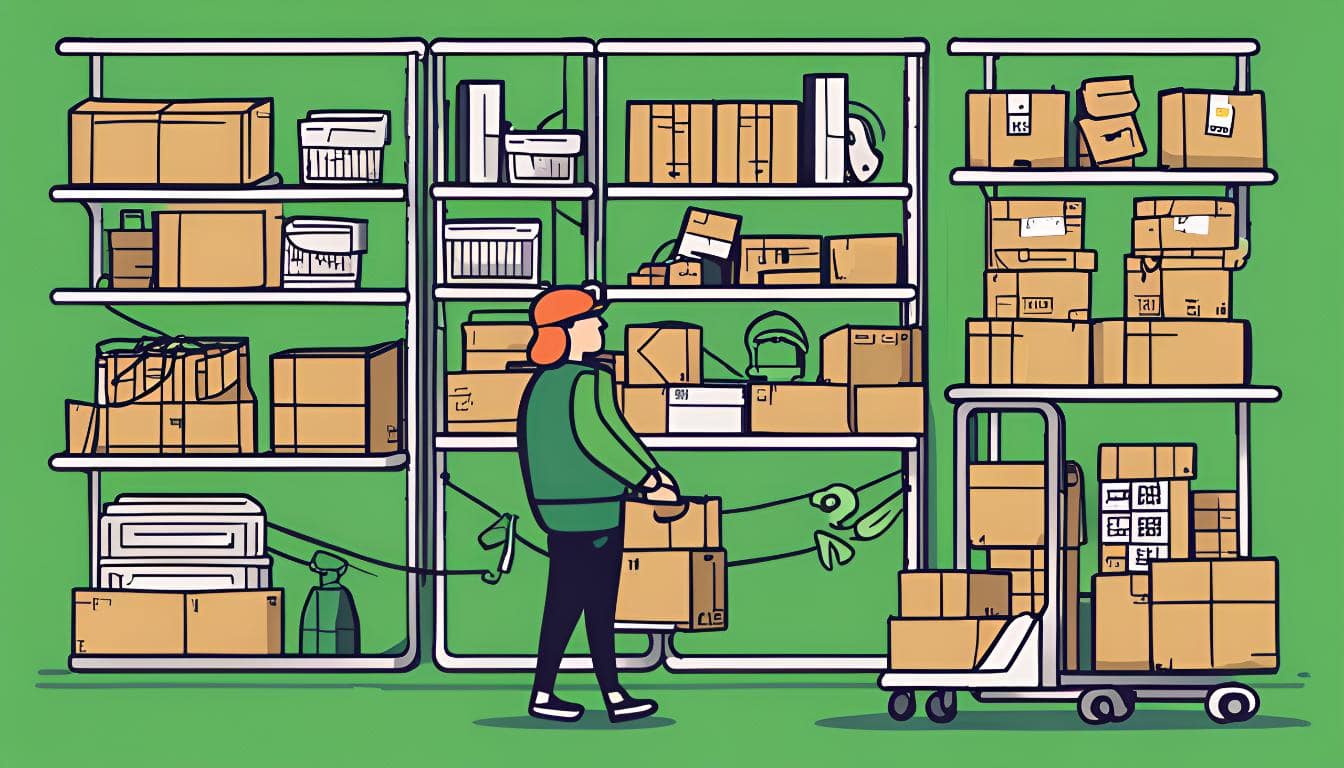
How to Calculate Inventory Carrying Cost In Ecommerce
- June 2025 (22)
- May 2025 (27)
- April 2025 (27)
- March 2025 (26)
- February 2025 (26)
- January 2025 (35)
- December 2024 (16)
- November 2024 (22)
- October 2024 (22)
- September 2024 (27)
- August 2024 (9)
- July 2024 (8)
- June 2024 (5)
- May 2024 (8)
- April 2024 (8)
- March 2024 (6)
- February 2024 (6)
- January 2024 (5)
- December 2023 (3)
- November 2023 (3)
- October 2023 (5)
- September 2023 (4)
- August 2023 (2)
- July 2023 (1)
- June 2023 (4)
- March 2023 (2)
- October 2022 (1)
- September 2022 (5)
- August 2022 (4)
- July 2022 (7)
- June 2022 (4)
- May 2022 (4)
- April 2022 (6)
- March 2022 (2)
- February 2022 (1)
- January 2022 (3)
- December 2021 (2)
- November 2021 (4)
- October 2021 (2)
- September 2021 (5)
- August 2021 (4)
- July 2021 (4)
- June 2021 (3)
- May 2021 (2)
- April 2021 (3)
- March 2021 (3)
- February 2021 (3)
- January 2021 (2)
- December 2020 (4)
- November 2020 (2)
- October 2020 (4)
- September 2020 (2)
- July 2020 (5)
- June 2020 (4)
- May 2020 (2)
- April 2020 (2)
- March 2020 (4)
- February 2020 (1)
- December 2019 (1)
- May 2018 (1)
- March 2018 (2)
- February 2018 (3)
- January 2018 (3)
- November 2017 (3)
- July 2017 (4)
- March 2017 (3)
- February 2017 (5)
- January 2017 (3)
- December 2016 (4)
- November 2016 (6)
- October 2016 (6)
- October 2015 (1)
- September 2015 (1)
- June 2015 (3)
- May 2015 (3)
- August 2014 (1)
- July 2014 (1)
- March 2014 (1)
- February 2014 (1)