Share this
Making Warehouse Performance Tracking Software a Worthwhile Investment
by Shipfusion Team on Apr. 9, 2025
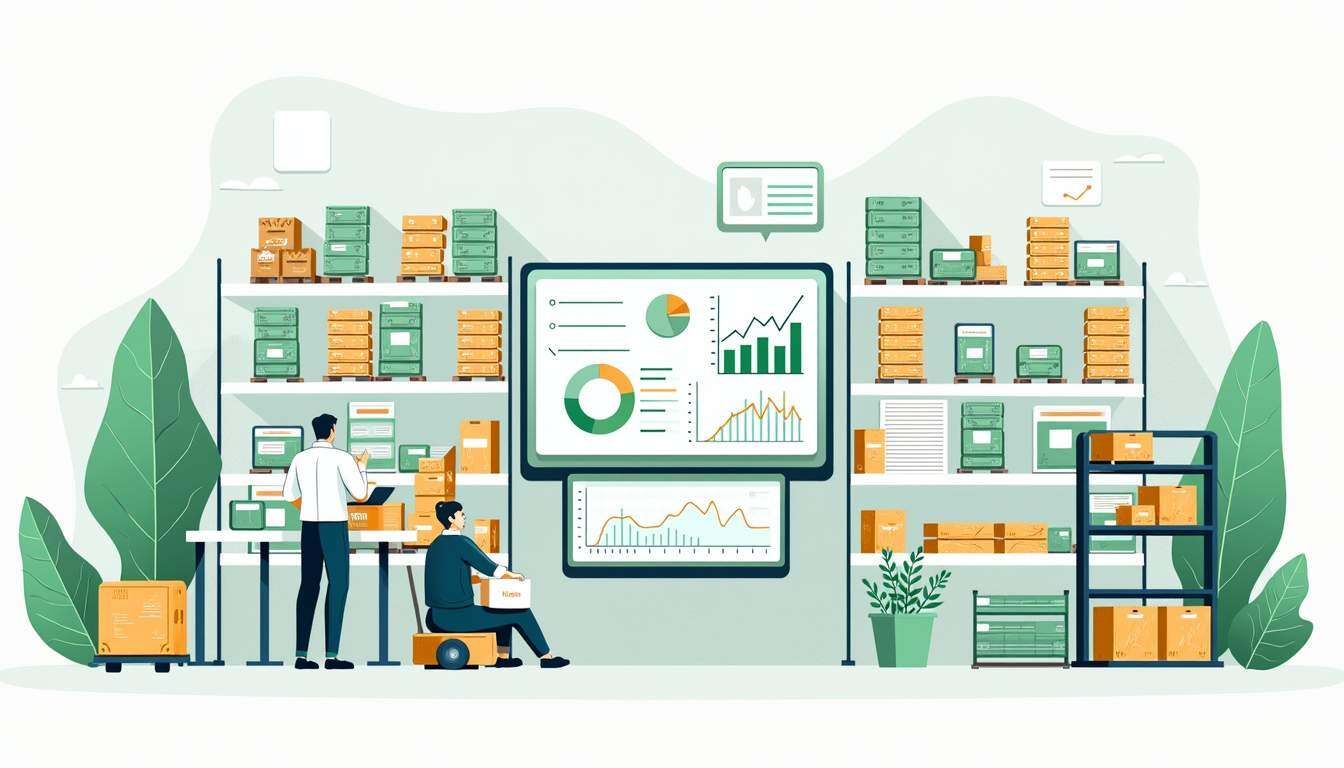
As ecommerce businesses scale, so do their fulfillment challenges. Without the right tools, businesses risk stock discrepancies, order delays, and inefficient workflows that can hurt profitability and customer satisfaction. Warehouse performance tracking software provides the real-time data and automation needed to optimize every aspect of fulfillment.
From monitoring inventory levels to improving order accuracy, the right software not only reduces errors and inefficiencies but also strengthens customer trust through faster, more reliable deliveries. Selecting the best system requires an understanding of its key features, benefits, and integration capabilities. This guide explores how warehouse performance tracking software can transform warehouse management, helping businesses optimize their fulfillment strategies and scale with confidence.
What Is Warehouse Performance Tracking Software?
Warehouse performance tracking software is a digital solution designed to monitor, analyze, and optimize warehouse operations in real time. It provides visibility into key performance metrics such as inventory accuracy, order fulfillment speed, and labor efficiency. For ecommerce businesses handling high order volumes, investing in a robust tracking system is essential for maintaining operational efficiency and meeting customer expectations.
Core Features of Warehouse Performance Tracking Software
Selecting the right warehouse performance tracking software requires a careful assessment of its features to ensure it aligns with your operational goals. A solution with robust capabilities can streamline processes, enhance efficiency, and prevent costly inventory mismanagement.
Real-Time Inventory Tracking
Maintaining up-to-the-minute visibility into inventory levels is essential for avoiding costly stockouts and overstock situations. For businesses dealing with seasonal demand, such as apparel retailers, this feature ensures inventory levels adjust in real-time to prevent unsold stock from accumulating. A system that provides accurate stock updates across multiple locations also ensures that products are replenished efficiently, keeping fulfillment seamless across warehouses.
Order Management
Efficient order processing is the backbone of warehouse operations, and the right software should automate and optimize every stage, from receipt to fulfillment. Implementing features like batch and wave picking helps businesses reduce fulfillment time by grouping similar orders together. This is particularly beneficial for high-demand products, where frequent shipments require rapid processing without overwhelming warehouse staff or delaying deliveries.
Data Analytics and Reporting
Data-driven decision-making is vital in modern warehouse management. Analytics tools provide valuable insights into supply chain Key Performance Indicators (KPIs) such as order accuracy, inventory turnover rates, and picking efficiency. Predictive analytics further enable businesses to prepare for peak sales periods, helping them optimize inventory levels and avoid over-purchasing, a critical advantage for industries where seasonal fluctuations dictate sales cycles.
Integration Capabilities
A warehouse management system should seamlessly integrate with existing business tools, including ERP and CRM platforms, to ensure data consistency and operational fluidity. For businesses managing complex distribution networks, this integration allows automated stock updates and smooth coordination between departments, reducing errors and increasing operational agility.
Benefits of Implementing Warehouse Performance Tracking Software
Implementing the right software can have a profound impact on warehouse productivity, cost management, and customer satisfaction, making it a critical investment for growing businesses.
Here’s more on those benefits:
Increased Productivity
Automation eliminates the need for repetitive manual tasks, allowing employees to focus on higher-value activities. Businesses processing high order volumes benefit significantly from automated systems that prioritize fulfillment speed while maintaining accuracy. For example, AI-driven workflows optimize task assignments, ensuring workloads are evenly distributed and warehouse teams operate at peak efficiency.
Cost Savings
By optimizing warehouse layouts, reducing waste, and improving space utilization, businesses can significantly cut operational expenses. Implementing automated slotting software helps arrange inventory based on demand frequency, ensuring that fast-moving products remain accessible. This reduces unnecessary labor and storage costs, improving the warehouse’s overall efficiency.
Enhanced Customer Satisfaction
When fulfillment operations run smoothly, businesses can maintain high service standards, fostering customer loyalty and repeat business. Accurate tracking and optimized fulfillment processes lead to fewer shipping errors and delays, ultimately improving customer experience. Barcode scanning verification is just one example of a feature capable of reducing inaccuracies, increasing order reliability and minimizing customer complaints.
Choosing the Right Warehouse Performance Tracking Software for Your Business
There’s a variety of warehouse performance tracking solutions available today. Businesses should prioritize scalability, usability, and vendor support to ensure long-term success.
Here’s what that means:
Scalability and Flexibility
Your warehouse operations will evolve over time, and your software must be able to keep up. A growing business moving from a single warehouse to multiple regional fulfillment centers benefits from a scalable solution that centralizes inventory and order management. The ability to integrate new automation technologies as business needs grow is equally crucial, ensuring that operational expansions do not compromise efficiency.
User-Friendly Interface
Overly complex software can slow down adoption and reduce productivity. An intuitive system with a clear dashboard and easily navigable features ensures quick onboarding and minimal disruptions. Mobile-compatible interfaces also provide warehouse staff with real-time access to inventory updates, reducing delays in stock tracking and order processing.
Vendor Support and Reliability
A software provider should offer strong customer support, regular updates, and ongoing training resources. Evaluating vendor reliability – especially during high-volume sales periods – ensures that businesses can maintain uninterrupted warehouse operations. Proactive support and system maintenance help mitigate the risks of downtime during peak demand.
Integrating Warehouse Performance Tracking Software with Existing Systems
To maximize efficiency, warehouse tracking software should function as part of a connected ecosystem rather than a standalone tool.
ERP and CRM Integration
Integrating with ERP and CRM platforms enhances coordination between warehouse and fulfillment center teams, sales departments, and customer service representatives. Providing customer service teams with real-time inventory visibility reduces order cancellations and improves response times. Seamless integration between systems ensures that stock levels are updated automatically, minimizing discrepancies in order fulfillment.
IoT and Automation
Leveraging IoT technologies can further enhance warehouse efficiency. RFID tags, smart shelving systems, and automated guided vehicles (AGVs) streamline tracking and movement of goods, reducing reliance on manual processes. These technologies improve warehouse accuracy by ensuring inventory records are continuously updated, reducing misplaced stock and fulfillment errors.
API Connectivity
A flexible API structure enables seamless integration with third-party applications, such as shipping carriers and accounting software, reducing manual data entry and improving operational efficiency. Automated shipping selection based on weight, distance, and service level ensures cost-effective logistics management, optimizing warehouse-to-customer delivery speeds.
Eliminate Your Need for Warehouse Performance Tracking Software
With Shipfusion's expert inventory management and cutting-edge real-time technology, there’s no need to invest in warehouse performance tracking software. As the top choice for ecommerce brands, we ensure seamless order processing, shipping, and returns with comprehensive technology and well-established processes. Benefit from our competitive shipping rates and a fulfillment process that guarantees accuracy and punctuality with every order. Real-time reporting will keep you in the loop and in control 24/7.
Contact us today and experience the difference with Shipfusion.
Share this
You May Also Like
These Related Articles
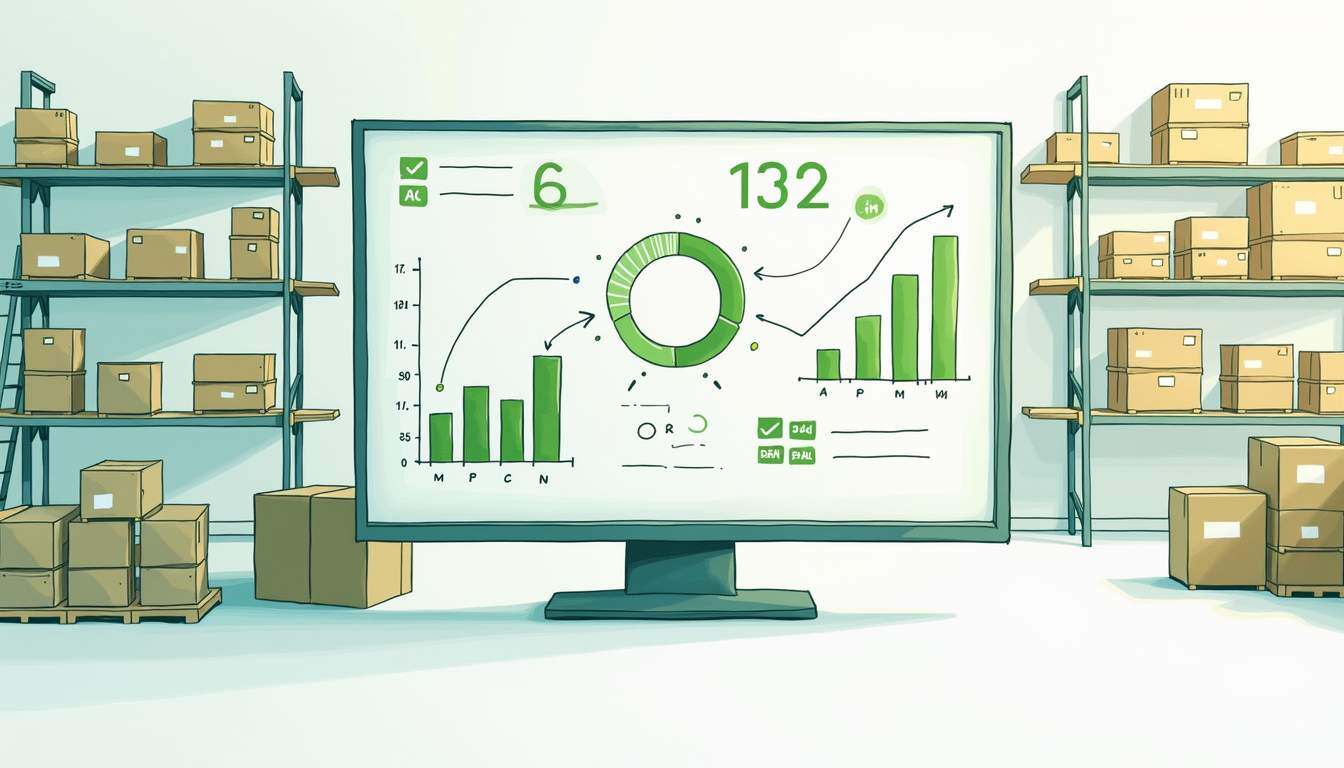
The ROI of an Inventory Management System for Warehouse Operations
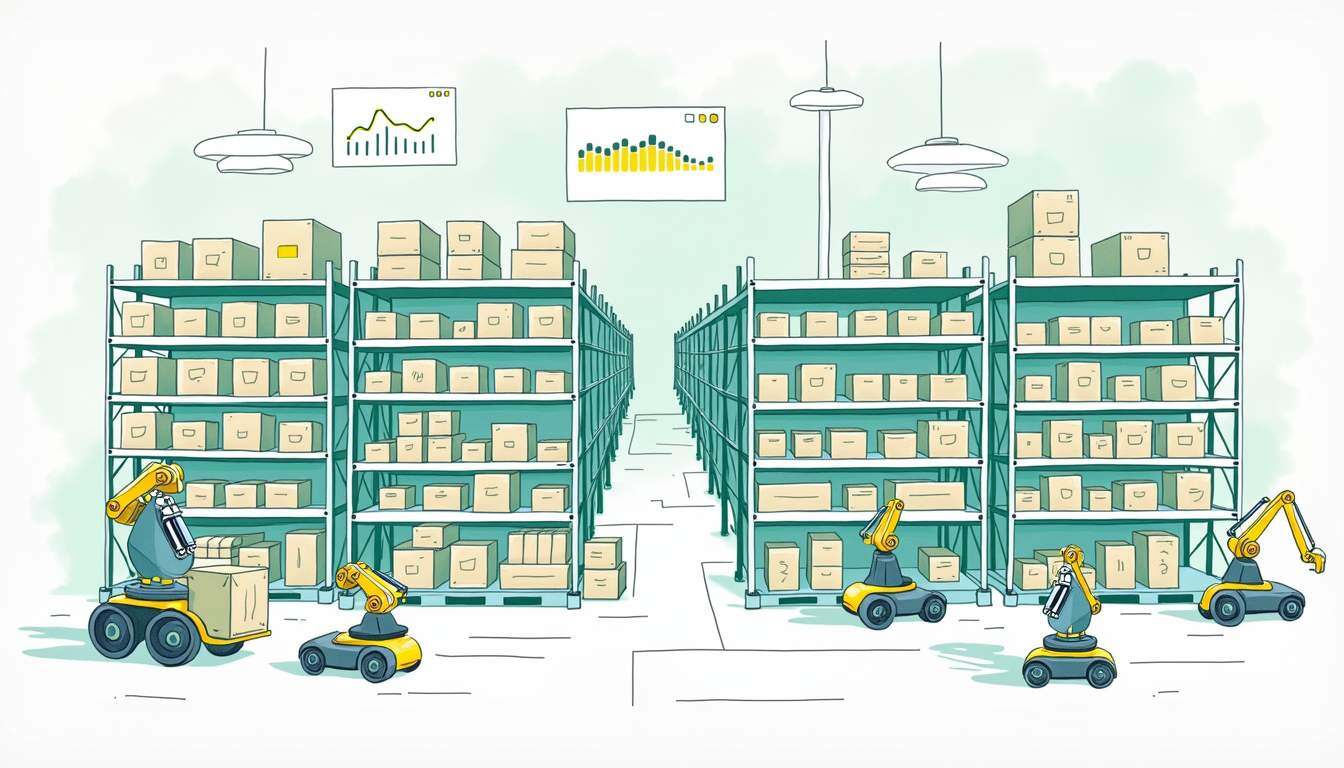
7 Ecommerce Warehouse Best Practices You Can Implement Right Now
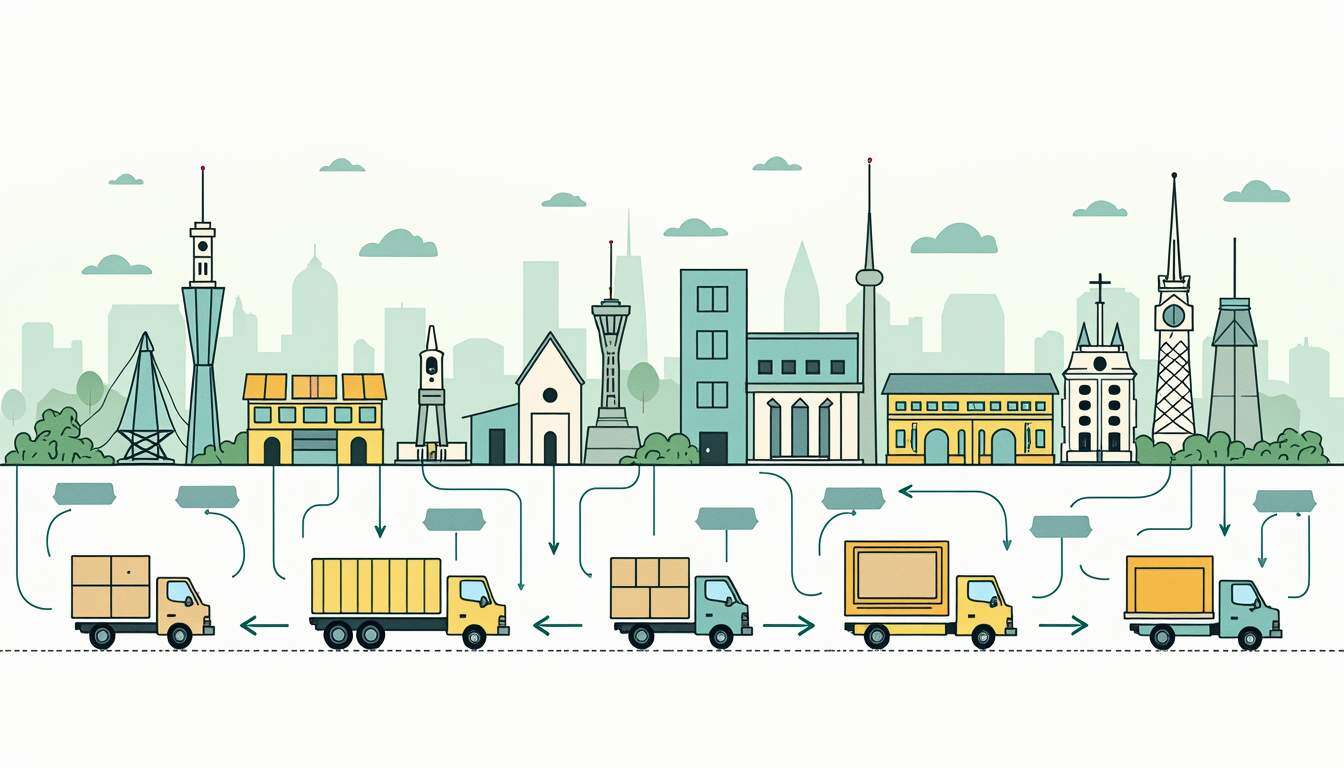
Shipping and Fulfillment In Ecommerce, Decoupled
- April 2025 (10)
- March 2025 (26)
- February 2025 (26)
- January 2025 (37)
- December 2024 (16)
- November 2024 (23)
- October 2024 (22)
- September 2024 (27)
- August 2024 (9)
- July 2024 (8)
- June 2024 (5)
- May 2024 (8)
- April 2024 (8)
- March 2024 (6)
- February 2024 (6)
- January 2024 (5)
- December 2023 (3)
- November 2023 (3)
- October 2023 (5)
- September 2023 (4)
- August 2023 (2)
- July 2023 (1)
- June 2023 (4)
- March 2023 (2)
- October 2022 (1)
- September 2022 (5)
- August 2022 (4)
- July 2022 (7)
- June 2022 (4)
- May 2022 (4)
- April 2022 (6)
- March 2022 (2)
- February 2022 (1)
- January 2022 (3)
- December 2021 (2)
- November 2021 (4)
- October 2021 (2)
- September 2021 (5)
- August 2021 (4)
- July 2021 (4)
- June 2021 (3)
- May 2021 (2)
- April 2021 (3)
- March 2021 (3)
- February 2021 (3)
- January 2021 (2)
- December 2020 (4)
- November 2020 (2)
- October 2020 (4)
- September 2020 (2)
- July 2020 (5)
- June 2020 (4)
- May 2020 (2)
- April 2020 (2)
- March 2020 (4)
- February 2020 (1)
- December 2019 (1)
- May 2018 (1)
- March 2018 (2)
- February 2018 (3)
- January 2018 (3)
- November 2017 (3)
- July 2017 (4)
- March 2017 (3)
- February 2017 (5)
- January 2017 (3)
- December 2016 (4)
- November 2016 (6)
- October 2016 (6)
- October 2015 (1)
- September 2015 (1)
- June 2015 (3)
- May 2015 (3)
- August 2014 (1)
- July 2014 (1)
- March 2014 (1)
- February 2014 (1)