Share this
Set Up a Warehouse Barcode System Using This Ready-Made Roadmap
by Shipfusion Team on Feb. 11, 2025
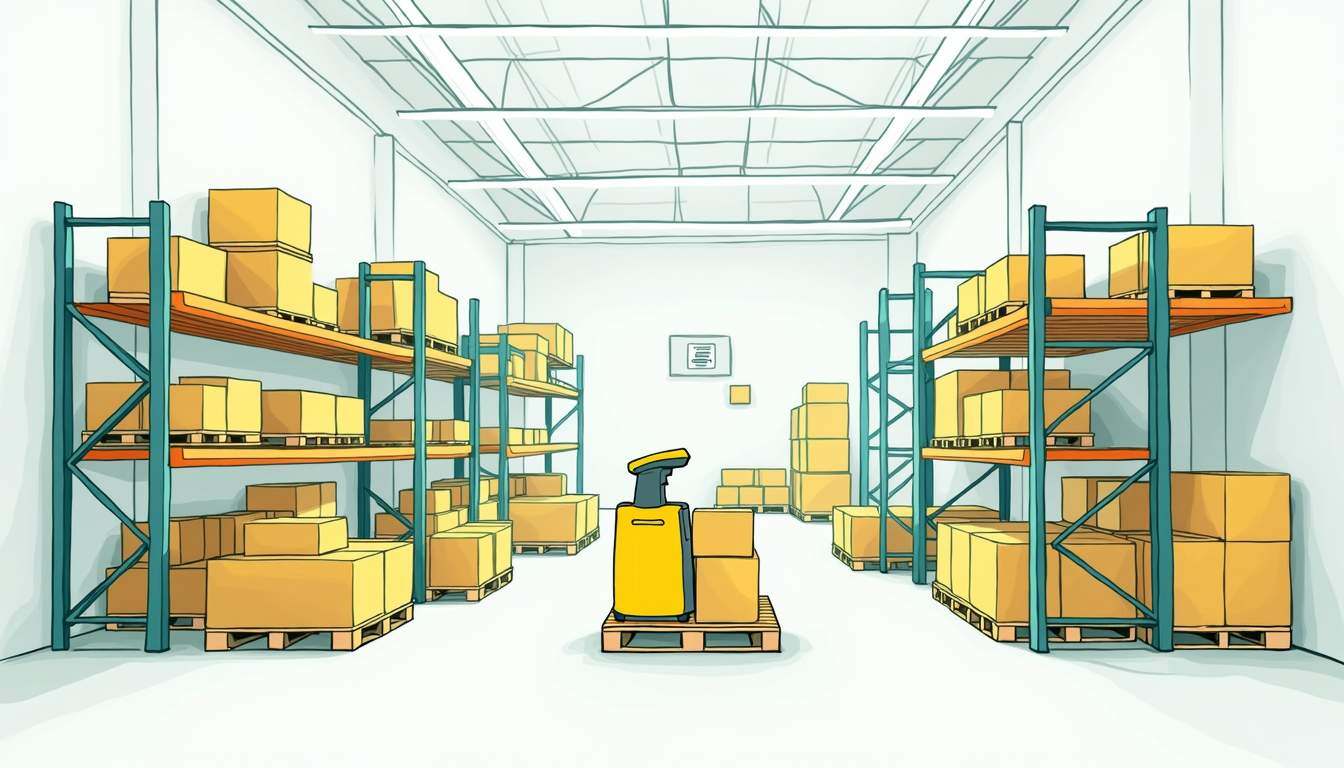
A warehouse barcode system enhances accuracy, speeds up operations, and improves inventory tracking. Whether you're transitioning from manual processes or upgrading an outdated system, implementing barcode technology streamlines workflows and reduces errors. A well-executed barcode system not only eliminates human error but also enhances warehouse productivity, optimizes inventory management, and improves order accuracy. Follow this step-by-step roadmap to set up a warehouse barcode system efficiently.
Assess Your Needs
Before implementing a barcode system, evaluate your warehouse's specific requirements. Identify pain points such as inventory mismanagement, slow order fulfillment, or high error rates. Consider factors like warehouse size, the number of SKUs, and operational complexity. Understanding these needs will help you select the right barcode technology and avoid unnecessary expenses.
Additionally, consider the nature of your inventory. Perishable goods, high-value items, or products with multiple variations may require different barcode labeling strategies. Think about how frequently inventory turnover occurs and whether your warehouse layout can support barcode scanning without causing bottlenecks. Analyzing past operational inefficiencies can provide insight into where a barcode system can have the greatest impact.
Choose Barcode Types
Selecting the right barcode type depends on your inventory and scanning needs. Common options include:
- 1D Barcodes: Traditional linear barcodes, ideal for simple identification and widely used in retail and logistics. They are cost-effective and compatible with most scanning systems but may not store as much information as 2D barcodes.
- 2D Barcodes: QR codes and DataMatrix codes store more information, support omnidirectional scanning, and are more resistant to damage. These are beneficial for warehouses needing more complex product tracking.
- 3D Barcodes: Emerging technology that enables higher security and data density, suitable for high-tech and industrial applications. These can store a significant amount of data and may be integrated into future automation solutions.
Evaluate your inventory structure and scanning requirements to determine the best barcode type for your warehouse. If your warehouse handles multiple product types, you may need a combination of barcode types to optimize scanning efficiency.
Select Barcode Scanning Hardware
Reliable barcode scanning hardware is essential for efficiency. Options include:
- Handheld Scanners: Portable and flexible for fast-paced operations. Ideal for mobile workforce operations and order picking, allowing workers to scan items on the go.
- Fixed Scanners: Mounted at conveyor belts for automated tracking and high-speed scanning with minimal manual intervention. These scanners work well in high-volume warehouses and help streamline product movement.
- Mobile Computers: Combine scanning, processing, and communication in a single device, improving worker productivity. These devices allow workers to manage multiple tasks without needing separate equipment.
Ensure your scanning hardware integrates seamlessly with your inventory system and is durable enough for warehouse conditions. Consider environmental factors such as extreme temperatures, dust, or moisture, which may impact scanner performance. Wireless and Bluetooth-enabled scanners can further improve mobility and workflow efficiency.
Integrate With Your WMS
A barcode system works best when integrated with a Warehouse Management System (WMS). The WMS updates inventory data in real-time as items move through the warehouse.
Integration enables:
- Automated stock updates to prevent discrepancies and keep inventory counts accurate.
- Faster order fulfillment by streamlining pick, pack, and ship workflows.
- Fewer manual entry errors, reducing labor costs and improving data accuracy.
- Instant access to inventory reports for informed decision-making and better demand forecasting.
Ensure compatibility between your barcode scanners and WMS to create a seamless workflow. Integration should also allow for easy scalability as warehouse operations expand. Some WMS platforms offer cloud-based solutions for multi-location inventory management, which can further enhance operational efficiency.
Label Inventory and Locations
Proper labeling ensures accurate tracking and minimizes search time.
Apply barcodes to:
- Individual products for precise item tracking, ensuring each SKU is accounted for in real-time.
- Storage bins and shelves to improve inventory organization and streamline picking and replenishment processes.
- Receiving and shipping zones for seamless stock movement tracking, reducing misplacements and optimizing logistics.
Use durable, high-quality labels that withstand warehouse and fulfillment center conditions like temperature fluctuations, moisture, and frequent handling. Consider using color-coded labels to further enhance visibility and streamline picking operations. Labels should also be placed in consistent, easy-to-scan locations to maximize scanning efficiency.
Train Your Staff
Employees must understand how to use barcode scanners effectively.
Training should cover:
- Proper scanning techniques to minimize errors and avoid misreads, ensuring that items are accurately logged.
- Error identification and resolution to ensure inventory accuracy and prevent disruptions in order fulfillment.
- WMS integration for real-time tracking, enabling employees to see updated stock levels instantly.
- Best practices for handling damaged or unreadable barcodes, ensuring that workflow disruptions are minimal.
- Routine scanning drills to maintain efficiency and reinforce training over time.
Providing hands-on training ensures employees can use the system confidently and avoid mistakes. Regular refresher courses help reinforce barcode scanning protocols and keep warehouse staff updated on system enhancements. A well-trained team ensures barcode implementation remains effective long-term.
Test and Optimize
Before fully rolling out your barcode system, conduct pilot tests.
Check for:
- Scanning speed and accuracy to ensure quick and efficient workflows that do not slow down operations.
- Label readability under different lighting conditions and scanning angles, verifying that all labels can be reliably scanned.
- Seamless WMS integration to confirm real-time inventory updates and system compatibility, preventing potential software conflicts.
- Batch scanning tests to determine how efficiently the system handles high-volume operations.
Collect feedback from warehouse staff and make necessary adjustments to optimize performance. Analyze test results to identify potential bottlenecks or inefficiencies, and address any gaps in scanning accuracy. Implementing continuous monitoring mechanisms ensures long-term barcode system effectiveness and scalability.
Shipfusion Uses the Best Warehouse Barcode System In the Business
A robust barcode system is critical for streamlined warehouse operations. Shipfusion employs advanced barcode technology, integrating seamlessly with a proprietary WMS to ensure real-time inventory management and accurate order fulfillment. With high-speed scanning, durable labeling, and expert implementation, Shipfusion enhances efficiency and minimizes errors in ecommerce fulfillment.
Beyond barcode technology, Shipfusion’s fulfillment centers are equipped with industry-leading automation tools. This ensures fast, error-free order processing while reducing operational costs. Whether you're scaling your ecommerce business or looking for greater inventory control, Shipfusion’s barcode system and fulfillment solutions provide the reliability you need.
Explore how Shipfusion can streamline your warehouse operations and reach out today.
Share this
You May Also Like
These Related Articles
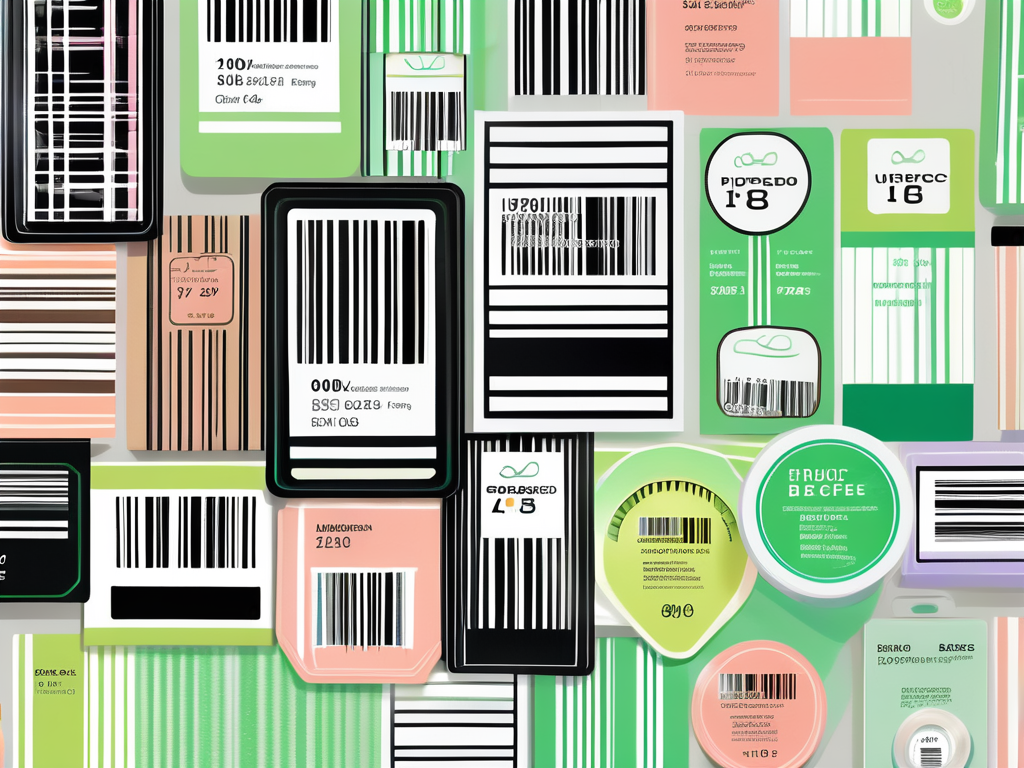
Product UPC Barcode: What It Is and Why It Matters In Ecommerce
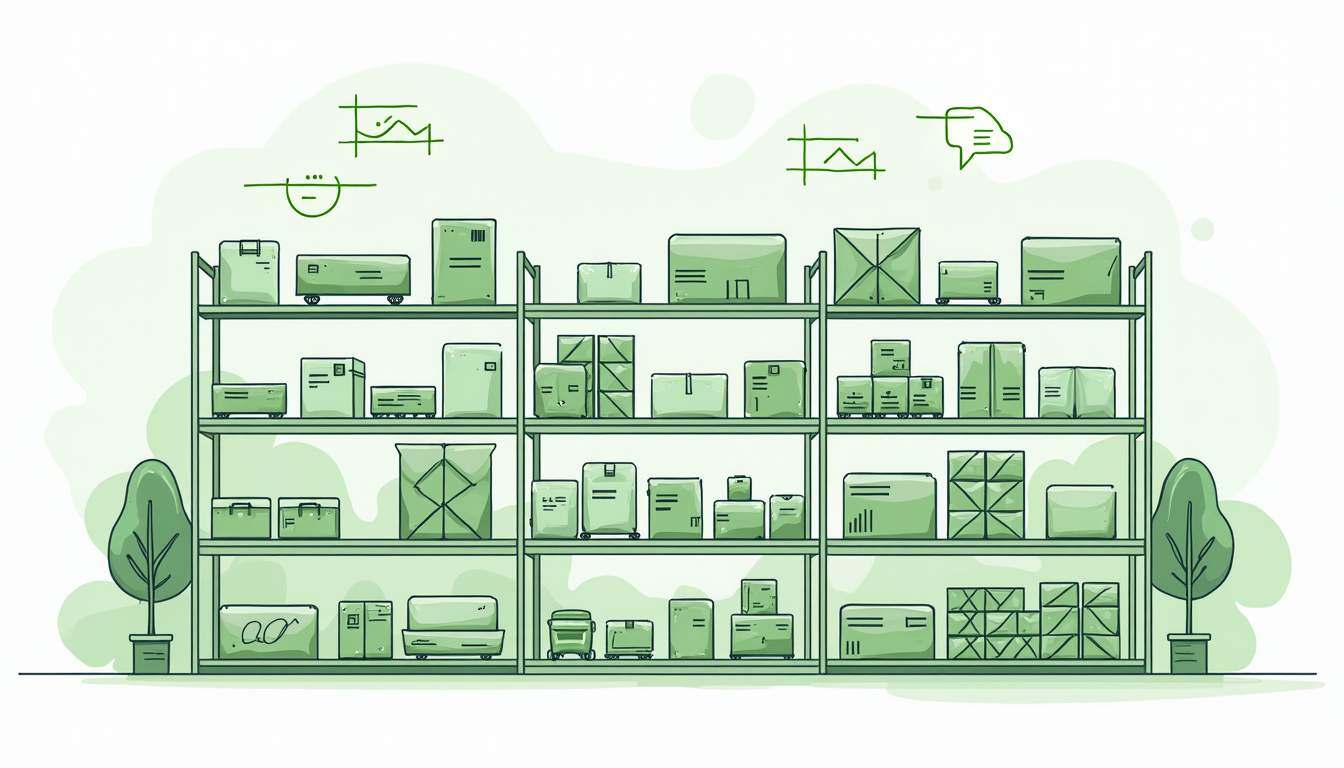
Become a Master of BigCommerce Inventory Management
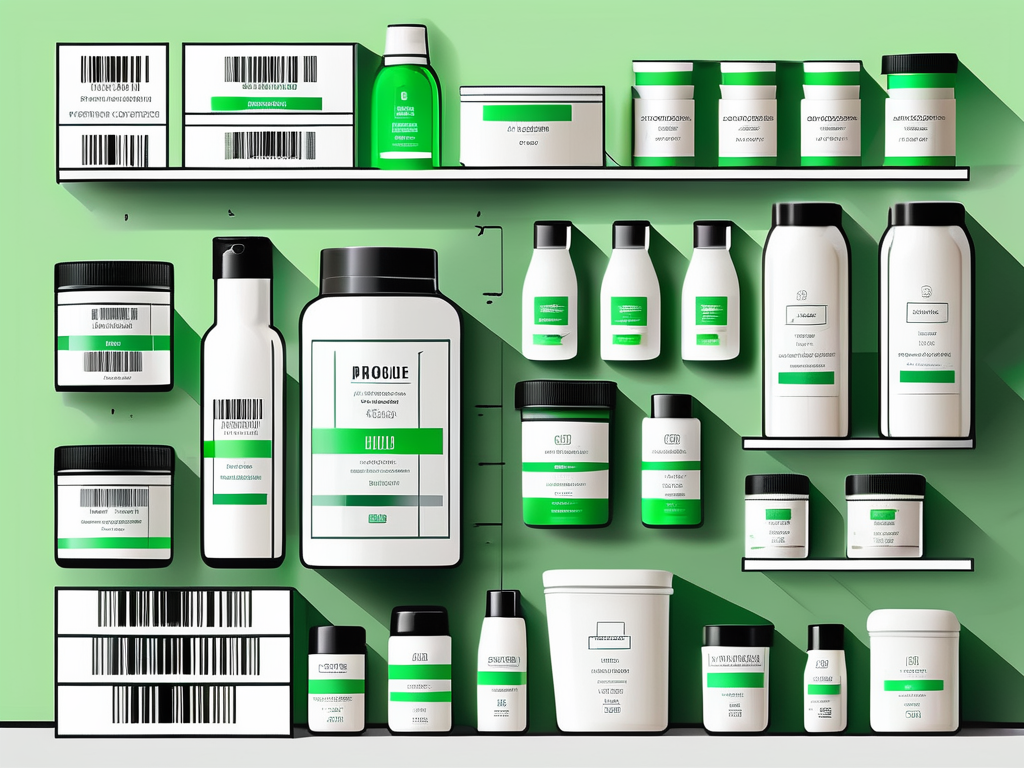
SKU vs UPC: Breaking Down the Differences
- April 2025 (18)
- March 2025 (26)
- February 2025 (26)
- January 2025 (37)
- December 2024 (16)
- November 2024 (23)
- October 2024 (22)
- September 2024 (27)
- August 2024 (9)
- July 2024 (8)
- June 2024 (5)
- May 2024 (8)
- April 2024 (8)
- March 2024 (6)
- February 2024 (6)
- January 2024 (5)
- December 2023 (3)
- November 2023 (3)
- October 2023 (5)
- September 2023 (4)
- August 2023 (2)
- July 2023 (1)
- June 2023 (4)
- March 2023 (2)
- October 2022 (1)
- September 2022 (5)
- August 2022 (4)
- July 2022 (7)
- June 2022 (4)
- May 2022 (4)
- April 2022 (6)
- March 2022 (2)
- February 2022 (1)
- January 2022 (3)
- December 2021 (2)
- November 2021 (4)
- October 2021 (2)
- September 2021 (5)
- August 2021 (4)
- July 2021 (4)
- June 2021 (3)
- May 2021 (2)
- April 2021 (3)
- March 2021 (3)
- February 2021 (3)
- January 2021 (2)
- December 2020 (4)
- November 2020 (2)
- October 2020 (4)
- September 2020 (2)
- July 2020 (5)
- June 2020 (4)
- May 2020 (2)
- April 2020 (2)
- March 2020 (4)
- February 2020 (1)
- December 2019 (1)
- May 2018 (1)
- March 2018 (2)
- February 2018 (3)
- January 2018 (3)
- November 2017 (3)
- July 2017 (4)
- March 2017 (3)
- February 2017 (5)
- January 2017 (3)
- December 2016 (4)
- November 2016 (6)
- October 2016 (6)
- October 2015 (1)
- September 2015 (1)
- June 2015 (3)
- May 2015 (3)
- August 2014 (1)
- July 2014 (1)
- March 2014 (1)
- February 2014 (1)