Share this
Understanding Warehouse Receiving: Best Practices
by Christie McLeod on Jul. 20, 2021
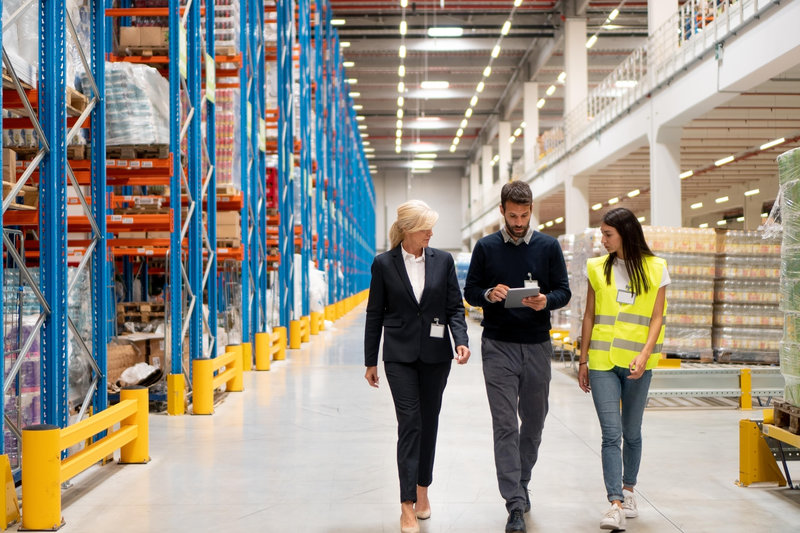
Receiving and storing inventory in ecommerce warehouses can be a lot more complicated than most people realize. It’s not a simple process by any means, and warehouse receiving goes far beyond just purchasing inventory and having it delivered to your warehouse.
Warehouse receiving involves several comprehensive key steps that must be done correctly to ensure that the right items and quantities are being delivered and stored properly.
Moreover, how a business receives its inventory at a warehouse can and will impact the other segments of the supply chain, including packing, picking, shipping, and even inventory management.
The process becomes even more complicated as your business expands, which generally means increasing your inventory and making sure that you’re shipping a larger number of your products within a reasonable time.
If your warehouse receiving process isn’t up to par, it can lead to stock control issues and greater operational costs. That’s why in this article, we’re going to talk about how to optimize your warehouse receiving with best practices—so you don’t fall behind as your business expands.
Identifying Warehouse Receiving Issues
When we talk about warehouse receiving, we’re talking about the first step in the ecommerce fulfillment process. In other words, the processes that include delivery, unloading, and storing your inventory in the warehouse fulfillment center of your choosing.
The purpose of warehouse receiving procedures is to take on the responsibilities of receiving the inventory, examining it, and sorting it. This helps to determine the condition of each shipment and whether they should be marked as “damaged goods,” while also maintaining accurate inventory numbers and records for each delivery.
Incidentally, these are the very things that make up for the majority of all warehouse inventory issues, as multiple people and parties often handle inventory before they even get to their designated shelf.
Let’s take a closer look at the typical warehouse distribution center and all of its moving parts to get a better understanding of where things can go wrong:
Receiving
Upon receiving inventory, it’s the duty of the receiving staff to inspect all deliveries to ensure the incoming goods match what’s on the order form and that there are no damaged products.
This also typically includes scanning the incoming shipments for inventory tracking.
Put-Away
Once the inventory is received, the warehouse staff are responsible for moving the products to a safe and secure storage location where they’ll remain until purchased by a customer.
Storage
The warehouse workers also keep track of all the inventory to ensure that all products remain secure for as long as they’re on the warehouse shelves. Temperature-sensitive items especially must be checked to make sure they don’t go bad and are removed from the shelves when and if they do.
They also relocate products when necessary, for example, the more popular products are often moved to a location for easier access.
Picking
This is the first step in the pick, pack, and ship process. Pickers are responsible for physically picking up the products from the warehouse storage shelves and moving them to the packing location once a customer has placed an order.
Packing
Packers are responsible for boxing and labeling the customer orders that are queued up to ship.
Restocking
When a product is returned, the warehouse workers are responsible for inspecting the item to ensure that it’s still intact or hasn’t expired. Once it passes a specific quality control, the product is restocked.
Auditing
Warehouse audits are conducted rather frequently to assess the overall effectiveness and efficiency of the warehouse distribution center. Auditing also gives insight to management in terms of how their teams are performing.
This is why it’s crucial to have a well-established warehouse receiving process. A well-established receiving process will make inventory management much more efficient, cost-effective, and all of the above less stressful.
Warehouse Shipping and Receiving Best Practices
To ensure that shipping and receiving in the warehouse runs smoothly and efficiently, follow these best practices:
Implement Inventory Management Systems
Warehouse receiving and distribution involves a ton of moving parts. The best thing you can do to optimize the entire process is by taking advantage of today’s technology and implementing an inventory management system, such as the inventory management software offered by Shipfusion.
This type of software enables you to automate virtually all tasks while analyzing data in real-time for a more accurate inventory count. All you have to do is load your existing inventory into the program, and you’ll be able to view accurate stock counts, set automatic reorder points, get inventory forecasting, and more.
Track Your Metrics
Tracking your inventory and logistics costs is essential to your process, especially if you’re using multiple warehouses for your inventory.
The metrics you’ll want to monitor specifically include:
● The average cost of storage per unit or item
● The total number of shelves, pallets, or bins currently in use for your products
● How much inventory is needed and ordered per location
By monitoring these metrics, you’ll be able to make smarter business decisions in terms of ordering, discontinuing, and more—transforming data into an advantage over the competition.
Implement a Document-Checking System
It may seem like a minor detail, but double-checking documents and verifying that the receiving order matches your inventory will save you a lot of time and money in the long run.
That’s why it’s necessary to implement a system for the receiving and shipping of all documents, in which each document has a numbering system and all associated forms are labeled in a sequential order.
This will make it easier for your teams to identify missing inventory in mislabeled items as part of your fulfillment services.
Conduct More Thorough Warehouse Audits
Warehouse audits may already be a part of your normal operations—which is a good start. However, if you want to optimize your processes and procedures, you’ll need to double down on your audits and conduct them more frequently.
Warehouse audits allow you to assess and analyze your entire team, processes, inventory, machinery, systems, and even your warehouse layout.
They take time, but it’s a way to see what’s working and what’s not working, so you can better manage your warehouse receiving processes and implement ways to make your fulfillment center more efficient.
As we’ve mentioned throughout this article, there are a lot of moving parts involved in a fulfillment center, which means that there’s a lot that can go wrong. Understanding the warehouse receiving best practices is your first step to streamlining your entire system for a more efficient and cost-effective tomorrow.
Shipfusion sets your business on autopilot and combines flexible, reliable fulfillment with powerful, real-time technology. Shipfusion has multiple fulfillment centers across the US and Canada– making it easy to manage your eCommerce business. For more information on how to set your business on autopilot, contact one of our fulfillment specialists today.
Share this
You May Also Like
These Related Articles
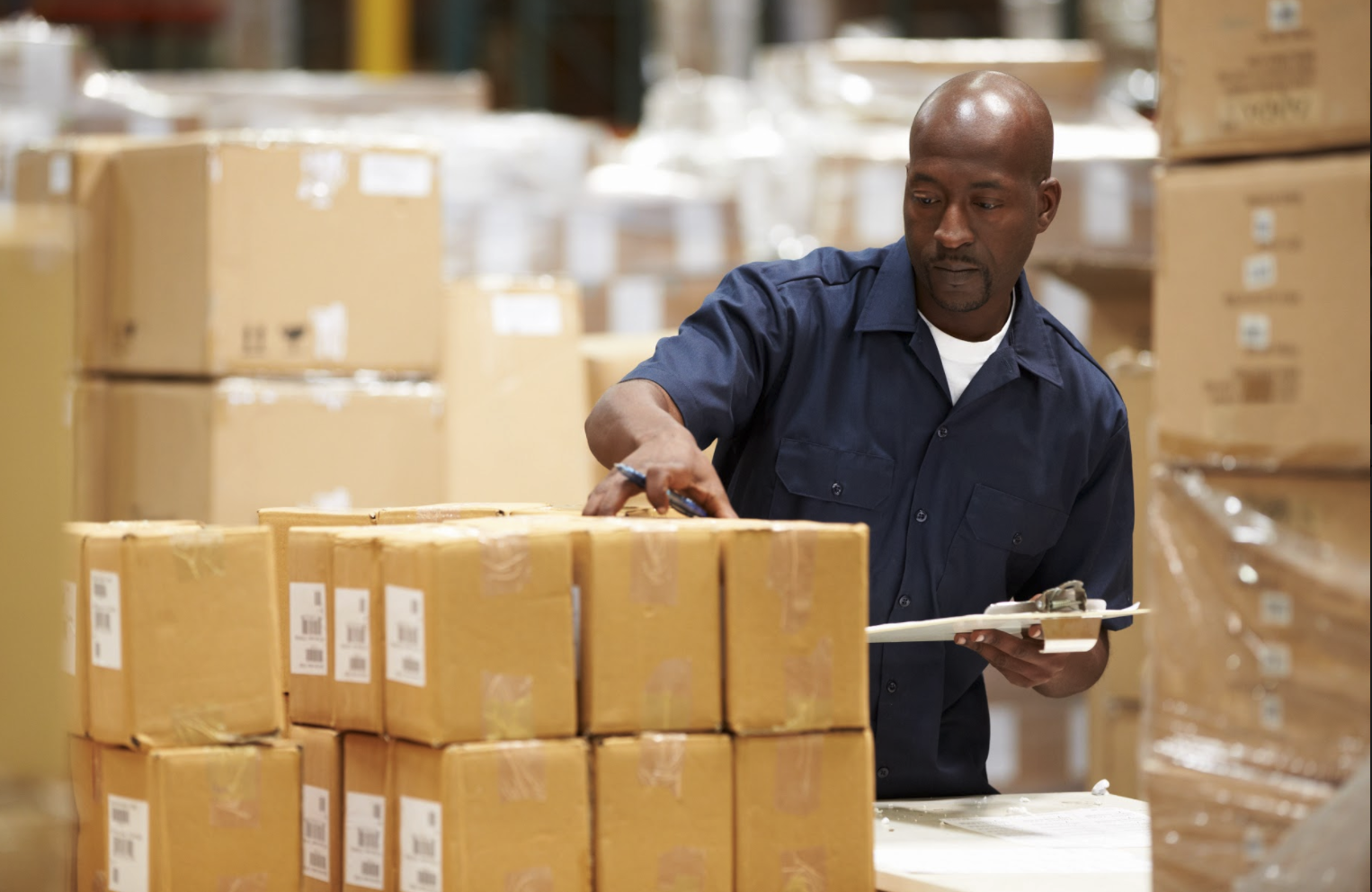
Navigating Common Order Fulfillment Issues
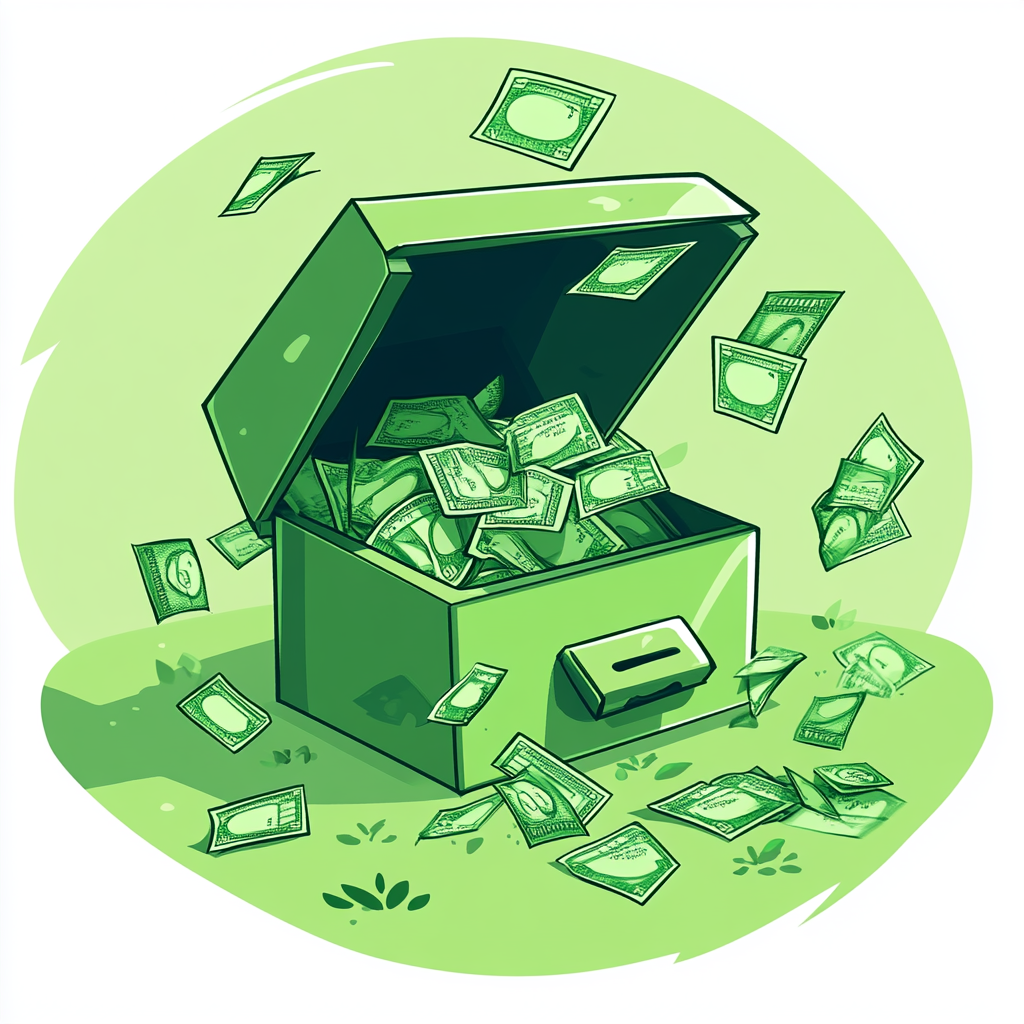
Should Freight Be Included In Inventory Cost?
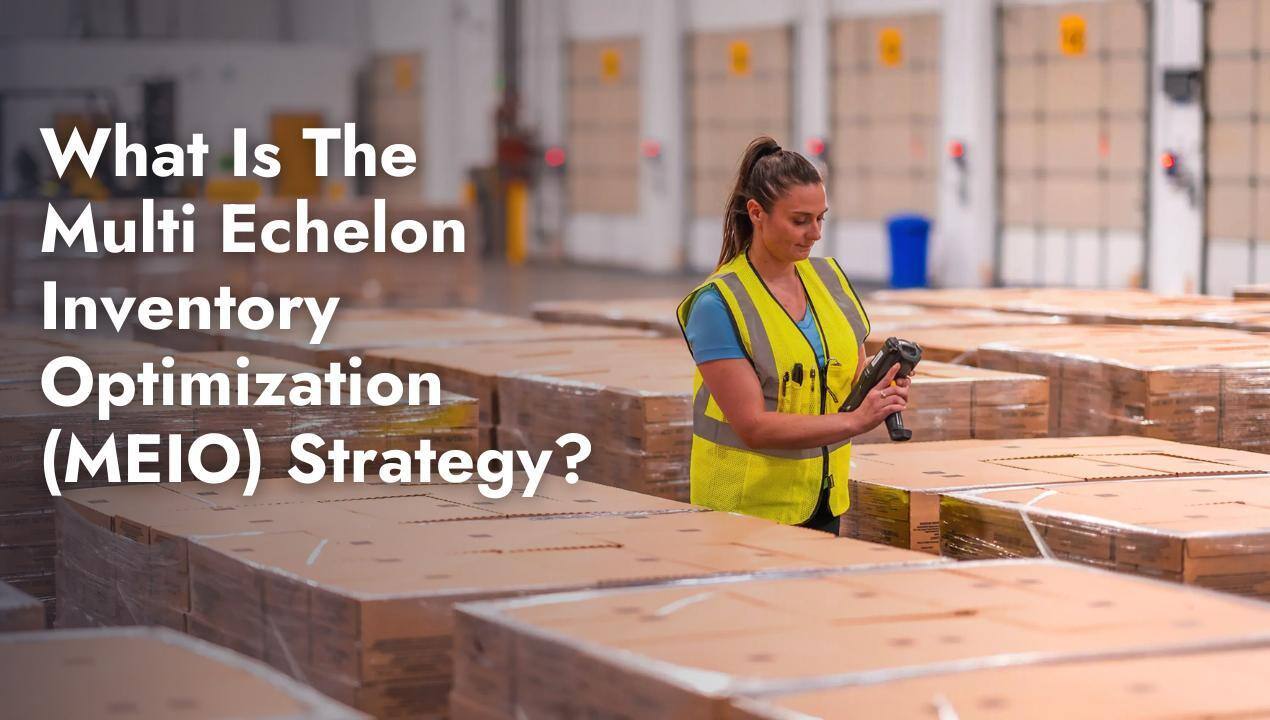
What Is the Multi Echelon Inventory Optimization (MEIO) Strategy?
- April 2025 (18)
- March 2025 (26)
- February 2025 (26)
- January 2025 (37)
- December 2024 (16)
- November 2024 (23)
- October 2024 (22)
- September 2024 (27)
- August 2024 (9)
- July 2024 (8)
- June 2024 (5)
- May 2024 (8)
- April 2024 (8)
- March 2024 (6)
- February 2024 (6)
- January 2024 (5)
- December 2023 (3)
- November 2023 (3)
- October 2023 (5)
- September 2023 (4)
- August 2023 (2)
- July 2023 (1)
- June 2023 (4)
- March 2023 (2)
- October 2022 (1)
- September 2022 (5)
- August 2022 (4)
- July 2022 (7)
- June 2022 (4)
- May 2022 (4)
- April 2022 (6)
- March 2022 (2)
- February 2022 (1)
- January 2022 (3)
- December 2021 (2)
- November 2021 (4)
- October 2021 (2)
- September 2021 (5)
- August 2021 (4)
- July 2021 (4)
- June 2021 (3)
- May 2021 (2)
- April 2021 (3)
- March 2021 (3)
- February 2021 (3)
- January 2021 (2)
- December 2020 (4)
- November 2020 (2)
- October 2020 (4)
- September 2020 (2)
- July 2020 (5)
- June 2020 (4)
- May 2020 (2)
- April 2020 (2)
- March 2020 (4)
- February 2020 (1)
- December 2019 (1)
- May 2018 (1)
- March 2018 (2)
- February 2018 (3)
- January 2018 (3)
- November 2017 (3)
- July 2017 (4)
- March 2017 (3)
- February 2017 (5)
- January 2017 (3)
- December 2016 (4)
- November 2016 (6)
- October 2016 (6)
- October 2015 (1)
- September 2015 (1)
- June 2015 (3)
- May 2015 (3)
- August 2014 (1)
- July 2014 (1)
- March 2014 (1)
- February 2014 (1)