Share this
9 Things Top WMS Systems Have In Common
by Shipfusion Team on Feb. 12, 2025
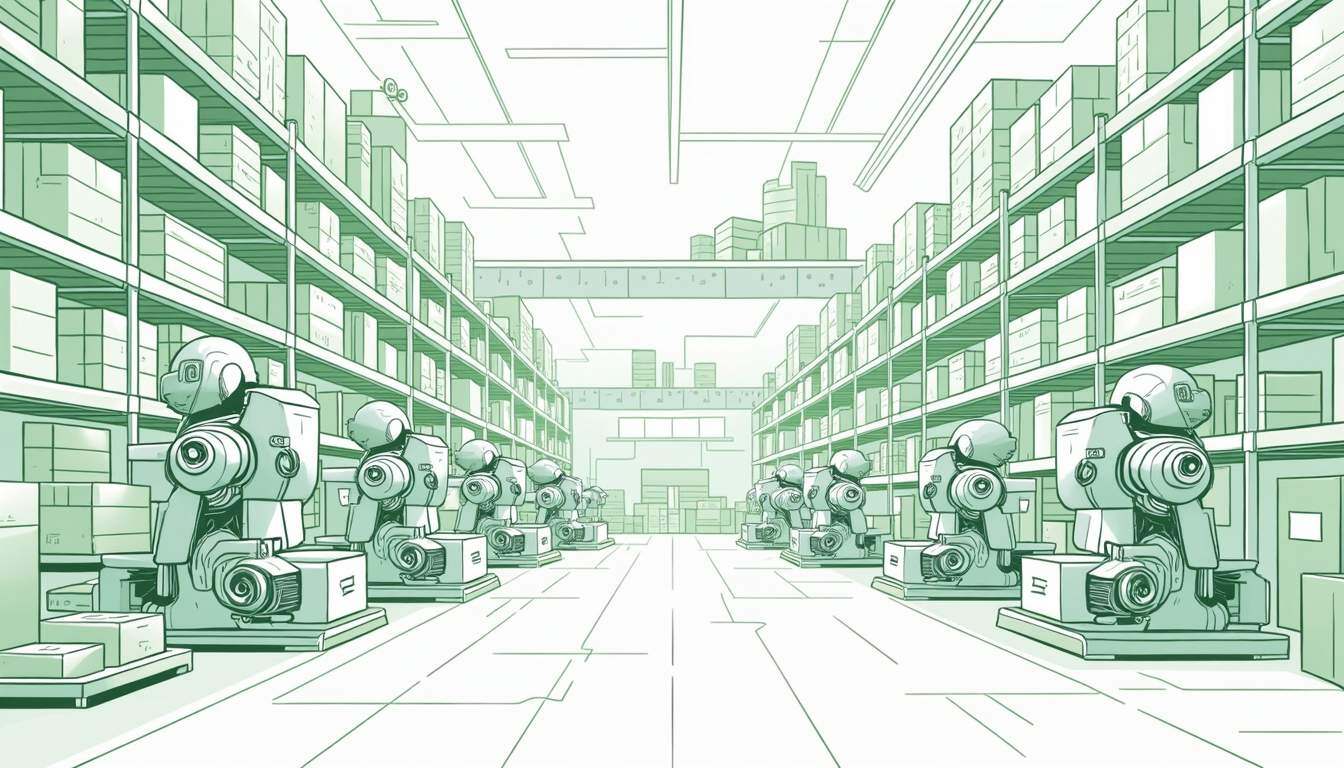
A Warehouse Management System (WMS) is the backbone of efficient ecommerce fulfillment. The best WMS platforms streamline inventory management, improve order accuracy, and enhance warehouse productivity. Whether you're managing a single warehouse or a global ecommerce fulfillment network, choosing the right WMS ensures smooth operations and business scalability. Here are nine key features all top WMS systems share.
1. Real-Time Inventory Visibility – Prevent Stockouts and Shrinkage
A top-tier WMS provides real-time inventory tracking, ensuring businesses always have an accurate stock count. This prevents stockouts, reduces shrinkage, and enables better demand forecasting. Instant visibility also helps maintain proper inventory levels across multiple fulfillment centers.
With real-time inventory tracking, businesses can avoid costly overstocking or understocking issues. Integrating with IoT sensors and RFID technology enhances accuracy by automatically updating stock levels as items move through the supply chain. Businesses that use real-time tracking see improved demand planning, reduced waste, and better customer satisfaction due to fewer backorders and order cancellations.
2. Automated Order Processing – Speed Up Fulfillment With Seamless Workflows
Automation is a game-changer in warehouse operations. Leading WMS platforms use automation to generate pick lists, optimize packing, and schedule shipments. This reduces manual intervention, minimizes errors, and accelerates fulfillment speed.
A well-implemented WMS reduces the need for manual data entry by integrating with order management systems (OMS) and enterprise resource planning (ERP) software. Automation also allows for intelligent wave picking, which groups orders by location or priority to reduce travel time within the warehouse. Additionally, automated exception handling ensures that damaged or missing inventory is flagged in real-time, preventing shipping delays.
3. Barcode and RFID Integration – Improve Accuracy In Tracking
Modern WMS systems integrate with barcode scanners and RFID technology to enhance tracking accuracy. These tools reduce human errors, speed up inventory audits, and improve order verification, ensuring each shipment is correct and accounted for.
RFID technology is particularly useful in high-volume warehouses where scanning barcodes manually can slow down operations. Unlike traditional barcodes, RFID tags can be read from a distance and in bulk, streamlining inventory movement tracking. By integrating with a WMS, businesses can gain real-time insights into stock levels and identify potential bottlenecks before they impact fulfillment.
4. Multi-Channel Support – Sync Inventory Across Platforms
Ecommerce businesses often sell on multiple platforms, including marketplaces, direct-to-consumer websites, and wholesale channels. A robust WMS synchronizes inventory data across all channels in real-time, preventing overselling and ensuring seamless operations.
Integrating with platforms like Shopify, Amazon, and Walmart ensures that inventory updates occur automatically, preventing discrepancies between warehouse stock and online listings. A WMS with strong multi-channel support also enables businesses to prioritize orders based on fulfillment location, reducing shipping costs and transit times.
5. Scalability – Adapt to Business Growth
A top WMS grows with your business. Whether expanding to new markets, adding warehouse locations, or increasing SKU counts, a scalable WMS accommodates these changes without disrupting operations. Flexible architecture ensures smooth scaling.
As ecommerce businesses grow, they often face the challenge of managing increasing order volumes and complex warehouse layouts. A scalable WMS provides features like dynamic slotting, which optimizes storage locations based on order frequency. Additionally, cloud-based WMS solutions allow businesses to scale their operations without requiring heavy upfront investment in infrastructure.
6. User-Friendly Interface – Reduce Learning Curves for Warehouse Teams
Ease of use is critical for warehouse efficiency. The best WMS platforms feature intuitive dashboards, customizable workflows, and simple navigation. This minimizes training time and ensures employees can quickly adapt to the system.
A cluttered or overly complex interface can slow down operations and lead to costly errors. A WMS with a user-friendly design provides real-time alerts, mobile compatibility, and quick access to reports. This enables employees to efficiently manage warehouse tasks without extensive training. Some platforms also offer role-based access, ensuring that workers only see the information relevant to their specific tasks.
7. Customizable Reporting – Track Performance With Tailored Analytics
Data-driven decision-making is essential for warehouse optimization. Leading WMS platforms provide customizable reporting tools, enabling businesses to track key metrics such as order accuracy, fulfillment speed, and inventory turnover. These insights help identify inefficiencies and improve performance.
A robust WMS allows users to create custom reports that analyze trends over time, helping businesses make informed decisions about staffing, inventory replenishment, and space utilization. Predictive analytics capabilities further enhance decision-making by using historical data to forecast demand and identify seasonal fluctuations.
8. Seamless Carrier Integration – Optimize Shipping and Reduce Costs
Shipping is a crucial component of ecommerce fulfillment. A high-performing WMS integrates with major carriers, providing real-time rate comparisons, automated label printing, and tracking updates. This ensures cost-effective and timely deliveries.
Carrier integrations allow warehouses to select the most efficient shipping options based on delivery speed, cost, and customer preferences. Advanced WMS solutions also support rate shopping, which automatically selects the best carrier based on predefined criteria. Integrating with third-party logistics (3PL) providers can further optimize fulfillment by enabling businesses to leverage external distribution networks for faster shipping.
9. Compliance and Security – Maintain Industry Standards and Data Protection
Compliance with industry regulations and data security standards is non-negotiable. Top WMS platforms offer robust security features, including role-based access controls, encryption, and audit trails. This protects sensitive data and ensures regulatory compliance.
Regulatory requirements vary by industry, and businesses handling regulated products like pharmaceuticals or food must ensure their WMS supports compliance with guidelines such as FDA regulations or GS1 standards. Cybersecurity measures like multi-factor authentication and data encryption protect against unauthorized access, ensuring warehouse operations remain secure.
Get Access to Top WMS Systems Through a 3PL
Choosing the right WMS can be complex, but working with a 3PL simplifies the process. Shipfusion’s proprietary WMS includes all these key features, offering real-time inventory tracking, automation, and seamless integration with ecommerce platforms and shipping carriers.
Beyond basic functionality, Shipfusion’s WMS is a fully integrated system that scales with business growth. If you're looking for a fulfillment partner with a top-tier WMS, explore Shipfusion’s solutions to enhance your supply chain today.
Share this
You May Also Like
These Related Articles
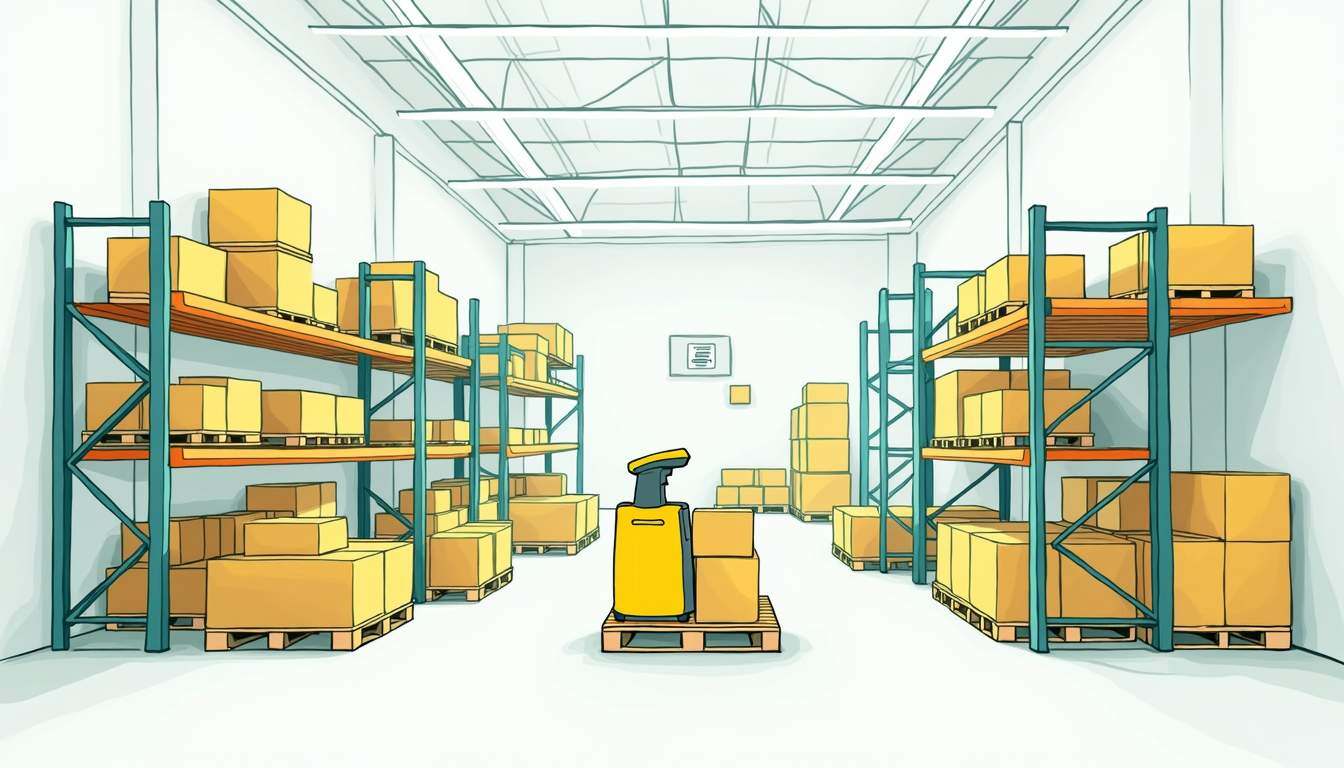
Set Up a Warehouse Barcode System Using This Ready-Made Roadmap
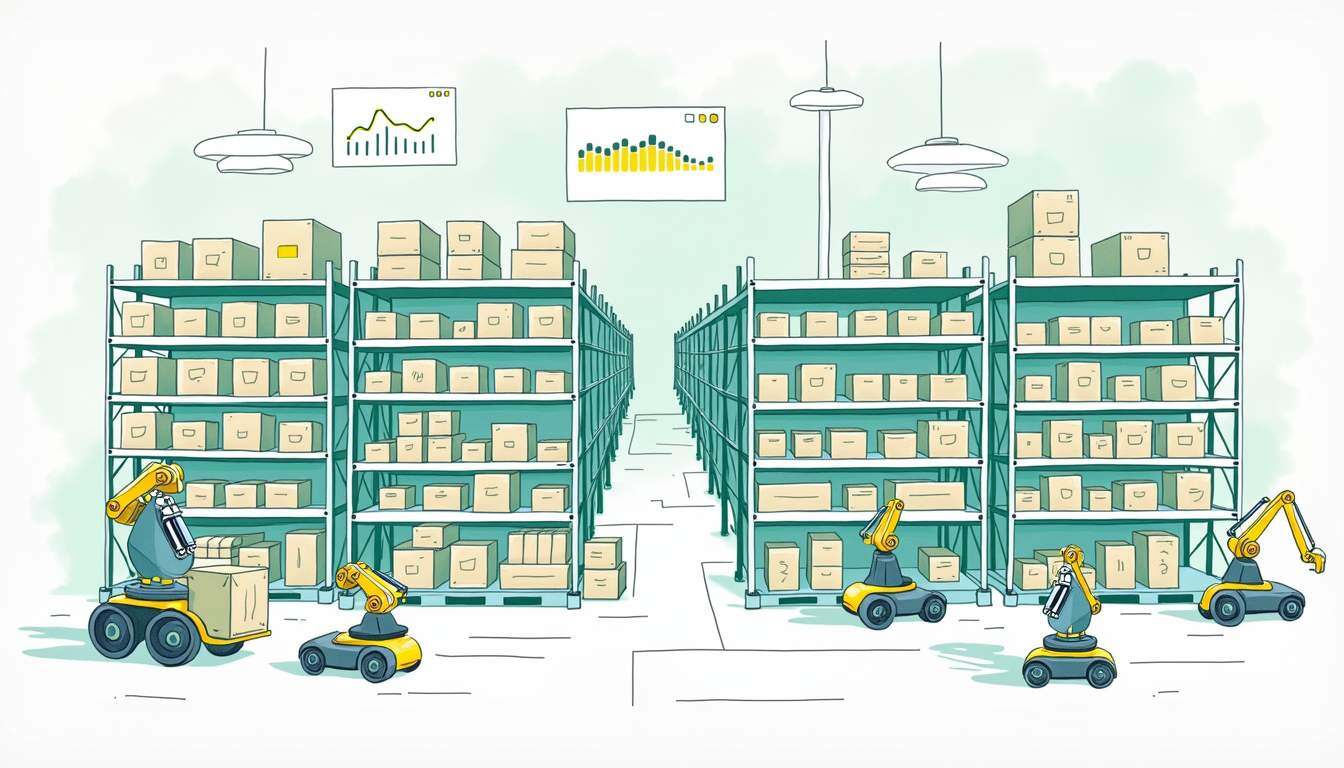
7 Ecommerce Warehouse Best Practices You Can Implement Right Now
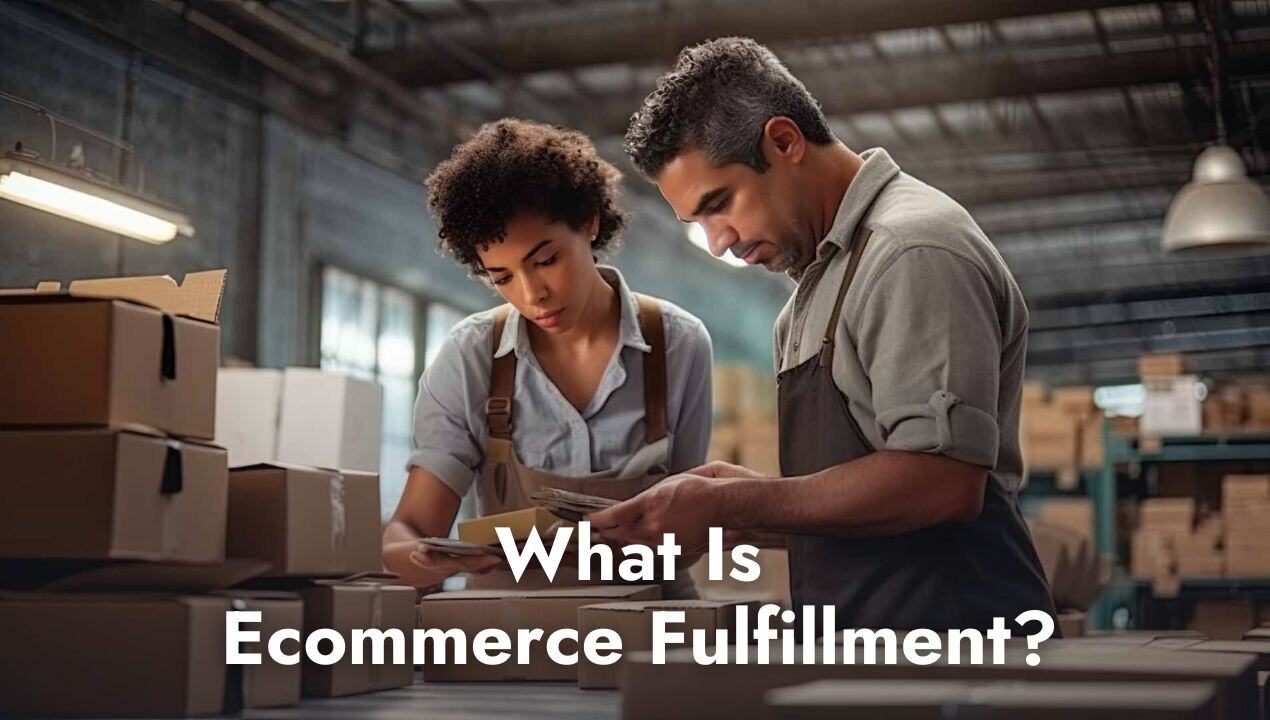
What Is Ecommerce Fulfillment?
- April 2025 (18)
- March 2025 (26)
- February 2025 (26)
- January 2025 (37)
- December 2024 (16)
- November 2024 (23)
- October 2024 (22)
- September 2024 (27)
- August 2024 (9)
- July 2024 (8)
- June 2024 (5)
- May 2024 (8)
- April 2024 (8)
- March 2024 (6)
- February 2024 (6)
- January 2024 (5)
- December 2023 (3)
- November 2023 (3)
- October 2023 (5)
- September 2023 (4)
- August 2023 (2)
- July 2023 (1)
- June 2023 (4)
- March 2023 (2)
- October 2022 (1)
- September 2022 (5)
- August 2022 (4)
- July 2022 (7)
- June 2022 (4)
- May 2022 (4)
- April 2022 (6)
- March 2022 (2)
- February 2022 (1)
- January 2022 (3)
- December 2021 (2)
- November 2021 (4)
- October 2021 (2)
- September 2021 (5)
- August 2021 (4)
- July 2021 (4)
- June 2021 (3)
- May 2021 (2)
- April 2021 (3)
- March 2021 (3)
- February 2021 (3)
- January 2021 (2)
- December 2020 (4)
- November 2020 (2)
- October 2020 (4)
- September 2020 (2)
- July 2020 (5)
- June 2020 (4)
- May 2020 (2)
- April 2020 (2)
- March 2020 (4)
- February 2020 (1)
- December 2019 (1)
- May 2018 (1)
- March 2018 (2)
- February 2018 (3)
- January 2018 (3)
- November 2017 (3)
- July 2017 (4)
- March 2017 (3)
- February 2017 (5)
- January 2017 (3)
- December 2016 (4)
- November 2016 (6)
- October 2016 (6)
- October 2015 (1)
- September 2015 (1)
- June 2015 (3)
- May 2015 (3)
- August 2014 (1)
- July 2014 (1)
- March 2014 (1)
- February 2014 (1)