Share this
What Is an RFID Warehouse Management System, and Do You Need One?
by Shipfusion Team on Feb. 13, 2025
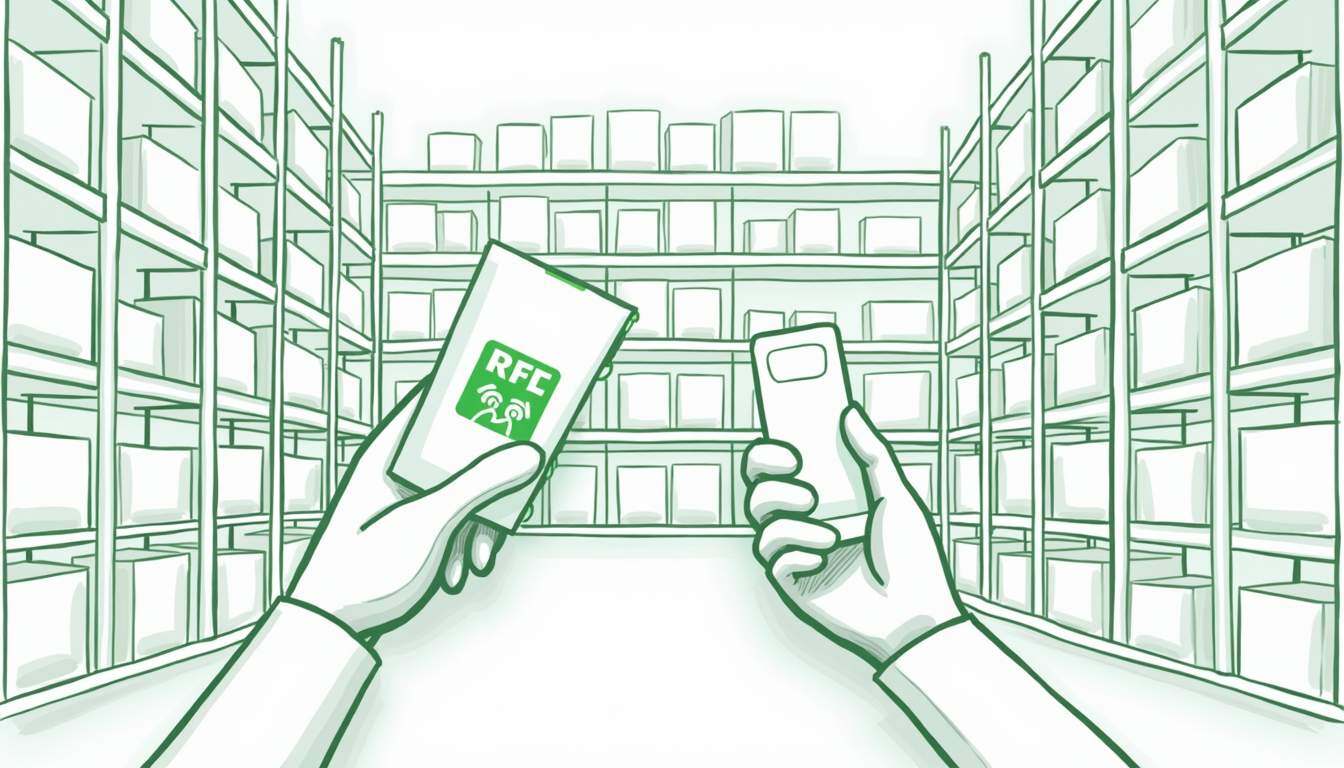
RFID (Radio Frequency Identification) technology is transforming warehouse management by providing faster, more accurate inventory tracking. But is it the right solution for your business? Here’s a breakdown of how RFID warehouse management systems work, their benefits, and potential challenges.
RFID vs. Barcode – What’s the Difference?
While both RFID and barcodes are used for inventory tracking, they function differently:
- Barcodes require line-of-sight scanning, meaning each item must be individually scanned. This makes the process slower and dependent on clear visibility of the barcode.
- RFID tags use radio waves, allowing multiple items to be scanned simultaneously, even from a distance. This significantly reduces scanning time and improves efficiency in high-volume warehouses.
RFID offers a faster, more automated approach to warehouse tracking compared to traditional barcoding. With the ability to track inventory movement in real-time, RFID provides businesses with a more dynamic way to manage inventory levels and optimize warehouse operations.
How RFID Works In a Warehouse
RFID systems consist of three key components:
- RFID Tags – Placed on inventory items, these tags store data that can be read wirelessly. They come in two forms: passive tags, which are powered by the RFID reader’s signal, and active tags, which have their own power source for longer-range scanning.
- RFID Readers – Fixed or handheld devices that scan RFID tags without requiring direct contact. Fixed readers are installed at key points in the warehouse, such as entry and exit points, while handheld readers allow for on-the-go scanning.
- RFID Software – Integrates with a warehouse management system (WMS) to update inventory in real-time. This software captures data from RFID readers and translates it into actionable insights for inventory control and order fulfillment.
With RFID, businesses can track inventory movement, automate stock counts, and reduce the time spent on manual scanning. Unlike barcode scanning, which requires a worker to manually scan each item, RFID allows multiple items to be scanned in a fraction of the time, increasing warehouse efficiency.
Use Cases for RFID In Warehouse Management
RFID technology enhances warehouse operations in several ways:
- Automated Inventory Audits – Eliminates the need for manual stock-taking, reducing labor costs and human errors. Warehouses can conduct cycle counts in real-time without disrupting daily operations.
- Faster Order Picking – Helps locate items quickly, reducing fulfillment times. With RFID, workers can be guided to product locations more efficiently, ensuring higher accuracy in picking orders.
- Enhanced Accuracy – Reduces human errors in inventory tracking. Since RFID eliminates the need for manual scanning, the risk of incorrect data entry or missed scans is significantly reduced.
- Real-Time Asset Tracking – Improves visibility of high-value or perishable goods. Businesses can monitor stock movement across multiple warehouse locations, preventing losses and improving security.
- Seamless Returns Processing – Speeds up restocking and returns management. RFID helps warehouses track returned items instantly, reducing turnaround times for resale or redistribution.
- Improved Supply Chain Visibility – Businesses can track goods from suppliers to customers, ensuring transparency and compliance with industry regulations.
- Temperature and Condition Monitoring – Some RFID tags come with sensors that can monitor temperature-sensitive products, ensuring compliance with storage requirements.
Cost and Implementation Considerations
Despite its advantages, RFID requires an upfront investment. Key costs include:
- RFID Tags – More expensive than barcodes, but reusable in some cases. Passive RFID tags are more affordable, while active RFID tags offer extended range but at a higher cost.
- RFID Readers – Higher initial cost compared to barcode scanners. Businesses need to decide between fixed and handheld readers based on warehouse layout and operational needs.
- Software Integration – Requires a compatible WMS for full functionality. Integration with existing warehouse systems can be complex and may require customization.
- Training & Setup – Employees must be trained on using RFID effectively. Training programs should cover best practices in scanning, system troubleshooting, and data analysis.
- Infrastructure Upgrades – Some warehouses may require additional networking capabilities to support RFID technology, adding to implementation costs.
For businesses with high inventory turnover or complex tracking needs, the long-term savings and efficiency improvements can outweigh the initial investment. Additionally, automation reduces reliance on manual labor, leading to long-term cost reductions.
Challenges and Limitations
While RFID offers many benefits, there are some challenges:
- Signal Interference – Metal and liquid items can disrupt RFID signals. Warehouses handling such products may need specialized RFID solutions.
- Implementation Complexity – Requires careful planning and integration. Poorly implemented RFID systems can lead to tracking inconsistencies.
- Compatibility Issues – Not all WMS platforms support RFID natively. Businesses may need middleware to integrate RFID data with their existing systems.
- Tag Costs – Can be prohibitive for businesses with low-margin products. Cost-benefit analysis is essential before implementation.
- Data Overload – RFID systems generate vast amounts of data, requiring businesses to invest in analytics tools to extract meaningful insights.
Understanding these challenges helps determine whether RFID is the right fit for your warehouse. Businesses should conduct pilot testing before full-scale deployment to assess feasibility.
RFID vs. Traditional Warehouse Management
Traditional warehouse management relies on barcoding and manual stock tracking. While effective, these methods can be time-consuming and prone to errors. RFID enhances automation, reduces labor costs, and improves accuracy. However, barcodes may still be preferable for businesses with lower inventory volumes or cost constraints.
Compared to barcode-based systems, RFID significantly reduces the time spent on stock counts, improves order accuracy, and enhances warehouse security. However, barcodes remain a cost-effective alternative for smaller warehouses or those operating with limited budgets.
Shipfusion’s RFID Warehouse Management System
For ecommerce businesses seeking high-speed, error-free fulfillment, Shipfusion’s RFID-enabled warehouse management system offers real-time tracking, automated inventory updates, and seamless integration with ecommerce platforms.
Beyond tracking, Shipfusion’s RFID technology enables:
- Automated reorder alerts based on real-time stock levels.
- Streamlined warehouse navigation for faster picking and packing.
- Intelligent demand forecasting powered by RFID-collected data.
- Seamless multi-location warehouse management, ensuring optimized stock distribution across facilities.
- Enhanced security measures, reducing theft and misplaced inventory.
If you’re considering RFID for your warehouse, Shipfusion provides the technology and expertise to optimize your supply chain and improve operational efficiency. Learn more about how Shipfusion can benefit your business by contacting us today.
Share this
You May Also Like
These Related Articles
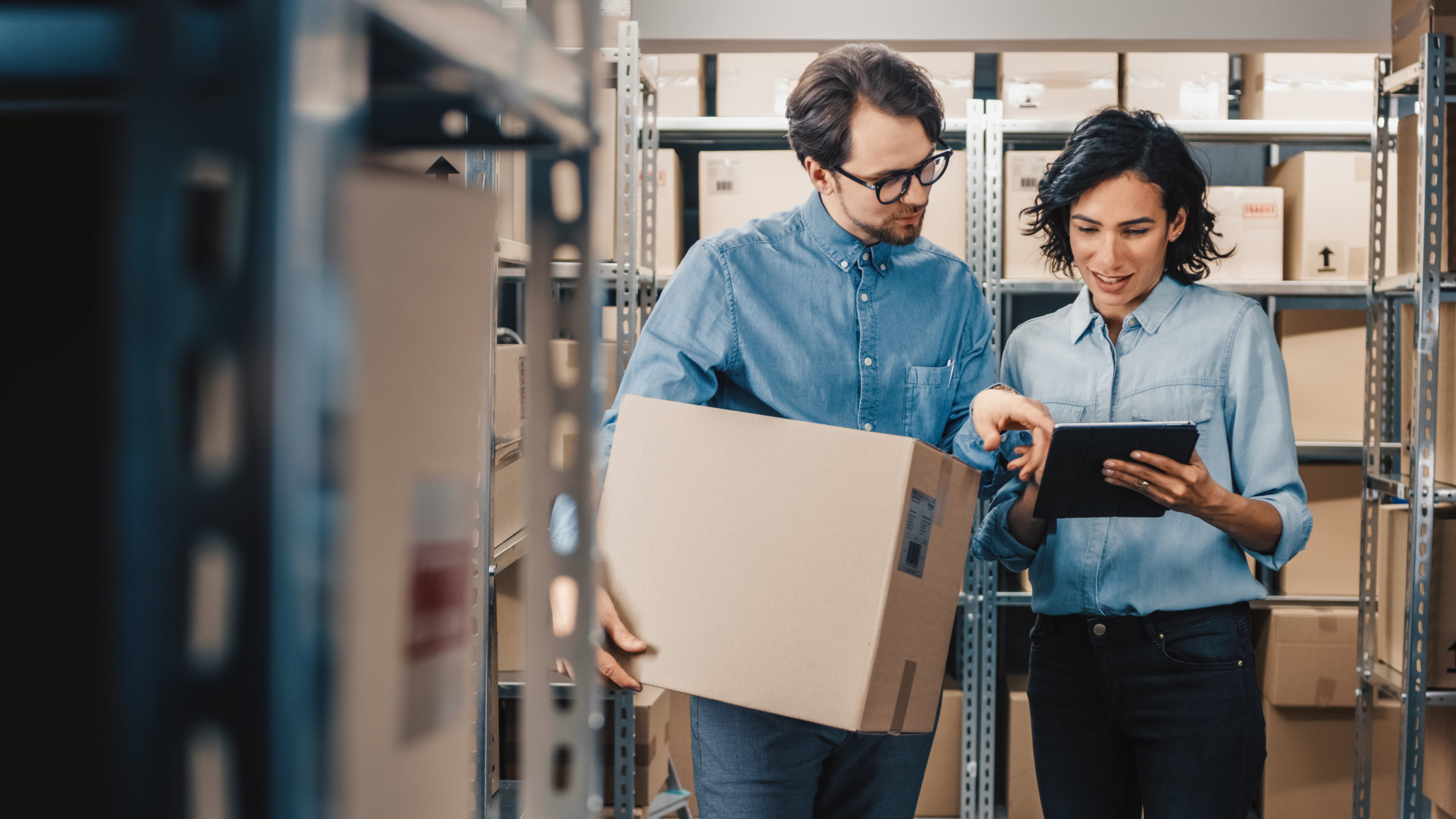
Fulfillment Inventory Management: Everything You Need To Know In 2024
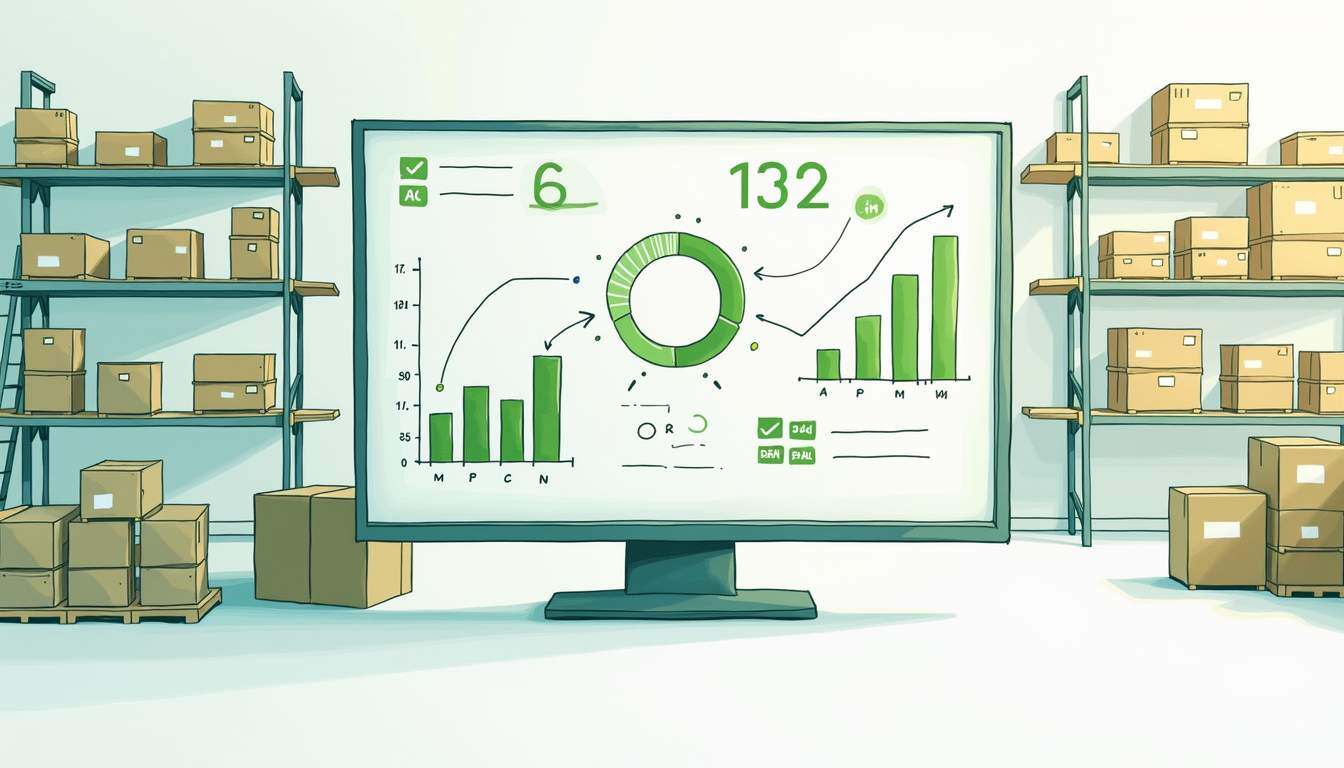
The ROI of an Inventory Management System for Warehouse Operations
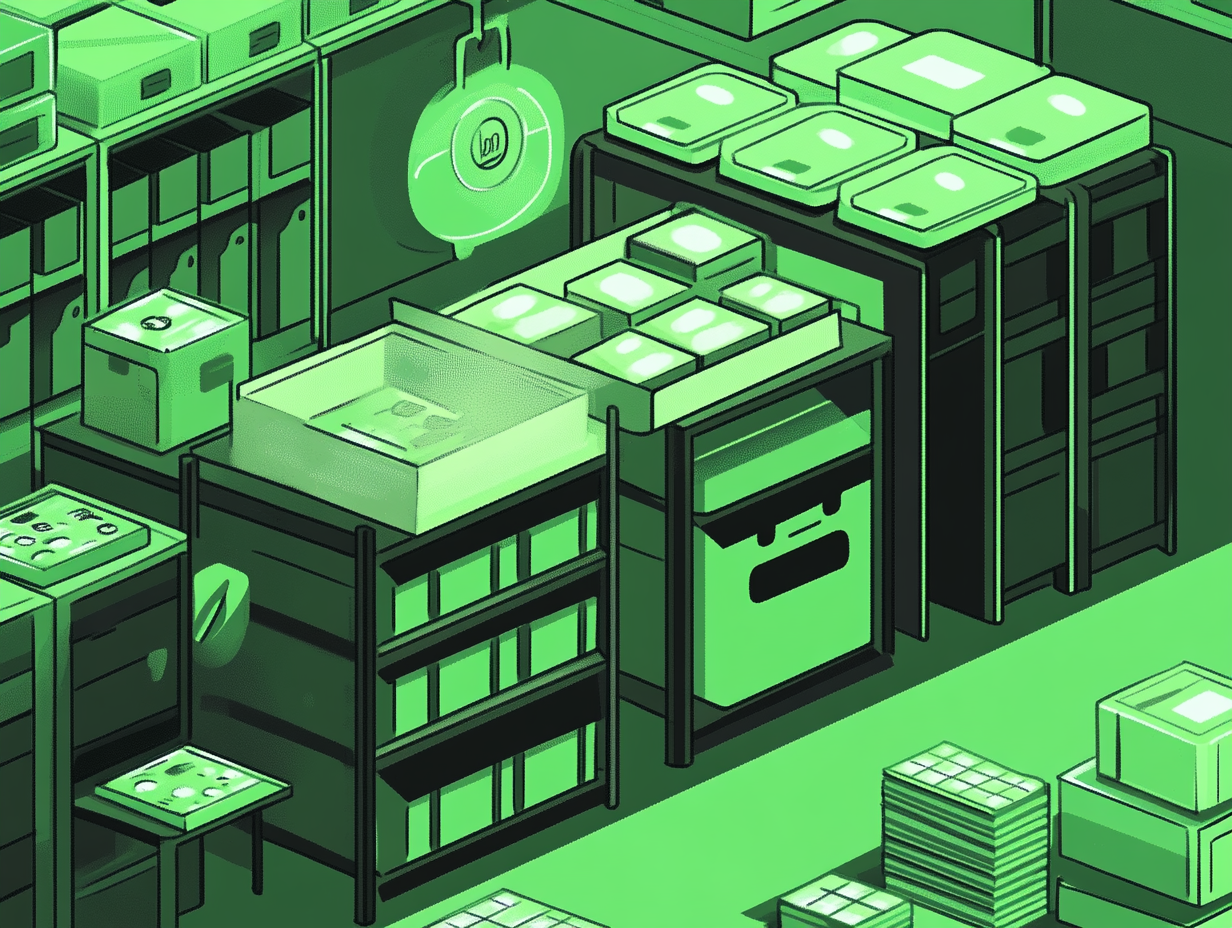
What Is LIFO Reserve In Ecommerce Inventory Management?
- April 2025 (18)
- March 2025 (26)
- February 2025 (26)
- January 2025 (37)
- December 2024 (16)
- November 2024 (23)
- October 2024 (22)
- September 2024 (27)
- August 2024 (9)
- July 2024 (8)
- June 2024 (5)
- May 2024 (8)
- April 2024 (8)
- March 2024 (6)
- February 2024 (6)
- January 2024 (5)
- December 2023 (3)
- November 2023 (3)
- October 2023 (5)
- September 2023 (4)
- August 2023 (2)
- July 2023 (1)
- June 2023 (4)
- March 2023 (2)
- October 2022 (1)
- September 2022 (5)
- August 2022 (4)
- July 2022 (7)
- June 2022 (4)
- May 2022 (4)
- April 2022 (6)
- March 2022 (2)
- February 2022 (1)
- January 2022 (3)
- December 2021 (2)
- November 2021 (4)
- October 2021 (2)
- September 2021 (5)
- August 2021 (4)
- July 2021 (4)
- June 2021 (3)
- May 2021 (2)
- April 2021 (3)
- March 2021 (3)
- February 2021 (3)
- January 2021 (2)
- December 2020 (4)
- November 2020 (2)
- October 2020 (4)
- September 2020 (2)
- July 2020 (5)
- June 2020 (4)
- May 2020 (2)
- April 2020 (2)
- March 2020 (4)
- February 2020 (1)
- December 2019 (1)
- May 2018 (1)
- March 2018 (2)
- February 2018 (3)
- January 2018 (3)
- November 2017 (3)
- July 2017 (4)
- March 2017 (3)
- February 2017 (5)
- January 2017 (3)
- December 2016 (4)
- November 2016 (6)
- October 2016 (6)
- October 2015 (1)
- September 2015 (1)
- June 2015 (3)
- May 2015 (3)
- August 2014 (1)
- July 2014 (1)
- March 2014 (1)
- February 2014 (1)