Share this
What Does It Take to Become an FDA Approved Warehouse?
by Shipfusion Team on Oct. 22, 2024
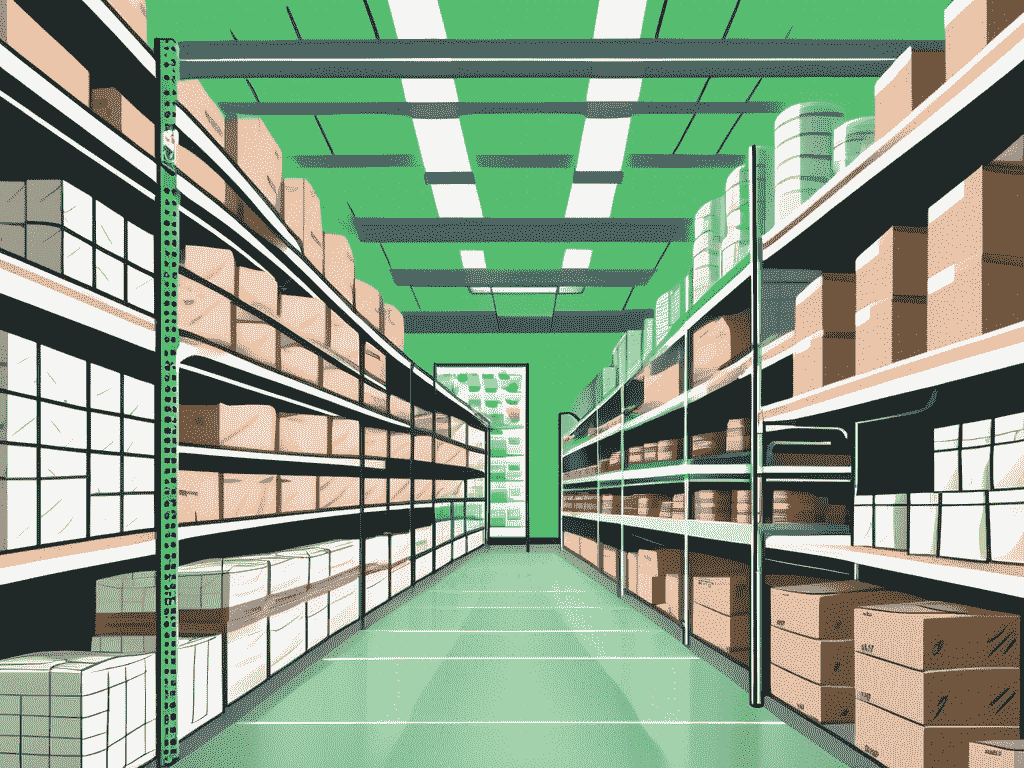
When it comes to storing FDA-regulated products like food and beverages, health supplements, or medical devices, not all warehouses are created equal. For ecommerce businesses handling sensitive goods, partnering with an FDA approved warehouse can be the difference between seamless operations and compliance headaches. In this article, we’ll explore what it takes to achieve FDA approval and why it’s essential for businesses operating in industries where safety, quality, and regulatory adherence are non-negotiable.
A Primer on FDA Warehouse Approval - What It Is and When It's Necessary
FDA warehouse approval pertains to the certification process that ensures a facility complies with established safety and quality standards. This approval is primarily relevant for warehouses that store items intended for human consumption, such as food products, pharmaceuticals, and medical devices. Compliance with the FDA's regulations protects public health by ensuring that the products distributed from these warehouses meet safety standards.
When is FDA approval necessary? Typically, any warehouse engaged in the storage of FDA-regulated goods must seek this certification. Without it, these warehouses cannot legally operate within the United States. Depending on the type of products stored, certain facilities might be subject to more specific requirements. For example, warehouses storing controlled substances face additional regulations due to the nature of their products.
Understanding the Approval Process
The FDA approval process is multifaceted, encompassing assessments of the facility’s design, the processes used for product handling, and the training of employees. Initially, a thorough inspection of the warehouse is conducted to evaluate factors such as cleanliness, organization, and adherence to safety protocols. Record-keeping practices are also scrutinized to ensure they are up to the FDA’s standards.
After the inspection, the FDA provides feedback and guidance on any areas requiring improvement. It is essential for warehouse operators to address these issues promptly to secure final approval. The entire process can take several months, making it vital for businesses to plan adequately. Additionally, warehouses must implement a robust quality management system to ensure ongoing compliance, which may include regular internal audits, employee training sessions, and updates to standard operating procedures. These proactive measures not only help in maintaining FDA approval but also enhance the overall efficiency and reliability of warehouse operations.
The implications of FDA warehouse approval extend beyond mere compliance; they can significantly impact a company's reputation and marketability. Consumers today are increasingly aware of safety standards and regulatory compliance, often preferring products from companies that demonstrate a commitment to quality and safety. As such, obtaining FDA approval can serve as a valuable marketing tool, instilling confidence in consumers and partners alike.
Additionally, warehouses that maintain FDA compliance may also find it easier to establish partnerships with suppliers and retailers who prioritize safety and regulatory adherence, further enhancing their business opportunities in a competitive marketplace.
What's Required of an FDA Approved Warehouse?
Meeting the FDA guidelines for warehouses involves several requirements, which aim to foster an environment conducive to maintaining product integrity. Begin with proper facility design: warehouses must have well-defined areas for the storage of different product types.
Defined zones help mitigate cross-contamination risks, especially when storing allergens or medications. This zoning should also extend to the layout of the warehouse, ensuring that high-risk products are stored away from lower-risk items. Additionally, the use of appropriate shelving and storage containers can further enhance organization and safety, making it easier to track inventory and manage recalls if necessary.
Temperature regulation is another key requirement. Many food and drug products necessitate specific storage conditions that must be consistently maintained to preserve product quality. For instance, pharmaceuticals often require cool and dry storage environments to maintain their effectiveness. Monitoring systems should be in place to track temperature and humidity levels continuously, with alarms set to alert staff of any deviations from the established parameters. This proactive approach not only safeguards the products but also ensures compliance with FDA regulations, as documented evidence of environmental conditions may be required during inspections.
Employee Training and Hygiene Practices
An essential aspect of FDA warehouse compliance is employee training. Staff must undergo comprehensive training programs designed to educate them on safety protocols, product handling procedures, and hygiene standards. Proper hygiene is vital in preventing contamination. Employees should adhere to strict sanitation practices, including regular hand washing and the wearing of protective gear when necessary. Furthermore, training should also cover the importance of personal hygiene, including guidelines on appropriate attire and grooming, to minimize the risk of introducing contaminants into the warehouse environment.
Regular training sessions will reinforce these practices. The development of Standard Operating Procedures (SOPs) is also pivotal. SOPs provide clear guidelines for actions in routine operations and emergencies, including product recalls, ensuring preparedness in case of unforeseen issues. These procedures should be easily accessible to all employees and regularly reviewed to incorporate any changes in regulations or best practices.
Additionally, conducting mock drills for emergency scenarios can help staff become familiar with the protocols, reducing response times and enhancing overall safety during actual incidents. By fostering a culture of compliance and awareness, warehouses can better protect both their products and the consumers who rely on them.
How Your Ecommerce Business Can Benefit from an FDA Approved Warehouse
For eCommerce businesses, having access to an FDA approved warehouse brings multiple advantages. First and foremost, it builds trust with consumers. Businesses that are transparent about their compliance with regulations can enhance their brand image and reputation. Customers are increasingly concerned about product safety, so having FDA approval validates a business's commitment to quality.
Additionally, working with an FDA approved warehouse can streamline logistics and distribution processes. When products are stored in a certified facility, it simplifies the compliance aspect when distributing products. Shippers and retailers are more likely to partner with businesses that can demonstrate adherence to regulatory standards, which can lead to broader market access.
Expanded Market Opportunities
Moreover, FDA approval opens doors to various markets that require certified suppliers. For example, retail chains often mandate their distributors meet specific regulatory standards before they will collaborate. By establishing partnerships with FDA approved warehouses, eCommerce businesses can increase their competitiveness within the industry.
As eCommerce continues to grow, aligning with FDA regulations can also facilitate international trade. Many countries have stringent import standards influenced by FDA regulations, making compliance essential for businesses hoping to expand globally. This can be particularly beneficial for companies looking to enter markets in Europe or Asia, where regulatory scrutiny is high. By leveraging FDA compliance, businesses can not only ensure smoother entry into these markets but also potentially reduce the time and costs associated with navigating complex regulatory landscapes.
Furthermore, utilizing an FDA approved warehouse can enhance operational efficiency. These facilities often come equipped with advanced inventory management systems and quality control processes that ensure products are stored and handled according to the highest standards. This not only minimizes the risk of contamination or spoilage but also allows for better tracking of product batches, which is crucial in case of recalls or safety alerts. As a result, businesses can maintain a more reliable supply chain, ultimately leading to improved customer satisfaction and loyalty.
How to Get Access to an FDA Approved Warehouse
Accessing an FDA approved warehouse requires proactive measures. The first step is to conduct thorough research to identify certified facilities that meet your product requirements. The FDA provides a comprehensive list of approved warehouses, making it easier for businesses to find suitable partners. This list can be an invaluable resource, as it not only highlights the facilities that have met stringent safety and quality standards but also provides insights into their specific capabilities, such as temperature control, security features, and inventory management systems.
After identifying potential facilities, the next phase involves outreach and potential partnerships. Establishing a working relationship with an approved warehouse allows access not only to compliant storage solutions but also to expertise in handling FDA-regulated products. As a business owner, it is beneficial to ask about their operational protocols, quality control measures, and how they deal with potential issues related to compliance. Additionally, inquiring about their experience with similar products can provide further assurance that they understand the unique challenges associated with your specific inventory, whether it be pharmaceuticals, food products, or medical devices.
Contractual Agreements and Compliance Monitoring
Once a partnership is established, it is crucial to formalize the arrangement through contractual agreements that outline roles, responsibilities, and compliance expectations. Regular audits and compliance monitoring will help maintain adherence to regulatory standards over time. These agreements should also include provisions for addressing any discrepancies or non-compliance issues that may arise, ensuring that both parties are clear on the steps to take should a problem occur.
Businesses should also be prepared to conduct periodic reviews of their warehouse partner’s compliance status to ensure ongoing adherence to FDA regulations. This proactive approach can help identify potential issues before they become significant problems. Furthermore, it may be advantageous to establish a communication channel for ongoing dialogue about regulatory updates, industry best practices, and any changes in operational procedures that could affect compliance. Engaging in such discussions not only strengthens the partnership but also fosters a culture of continuous improvement and vigilance in maintaining FDA standards.
Shipfusion Has More Than Just FDA Approved Warehouse Space
Securing an FDA approved warehouse keeps your products compliant while opening doors for your ecommerce business. With the right storage partner, you’re setting up a streamlined, worry-free process that keeps your goods safe and your business growing.
Whether you're shipping sensitive medical devices or temperature-controlled food products, Shipfusion is equipped to serve your inventory management and order fulfillment needs at scale. Our third-party logistics (3PL) solutions are administered in certified warehouses to ensure both you and your customers consistently get the quality you expect.
Talk with an expert today to learn more about what Shipfusion’s industry-leading suite of services can do for you.
Share this
You May Also Like
These Related Articles
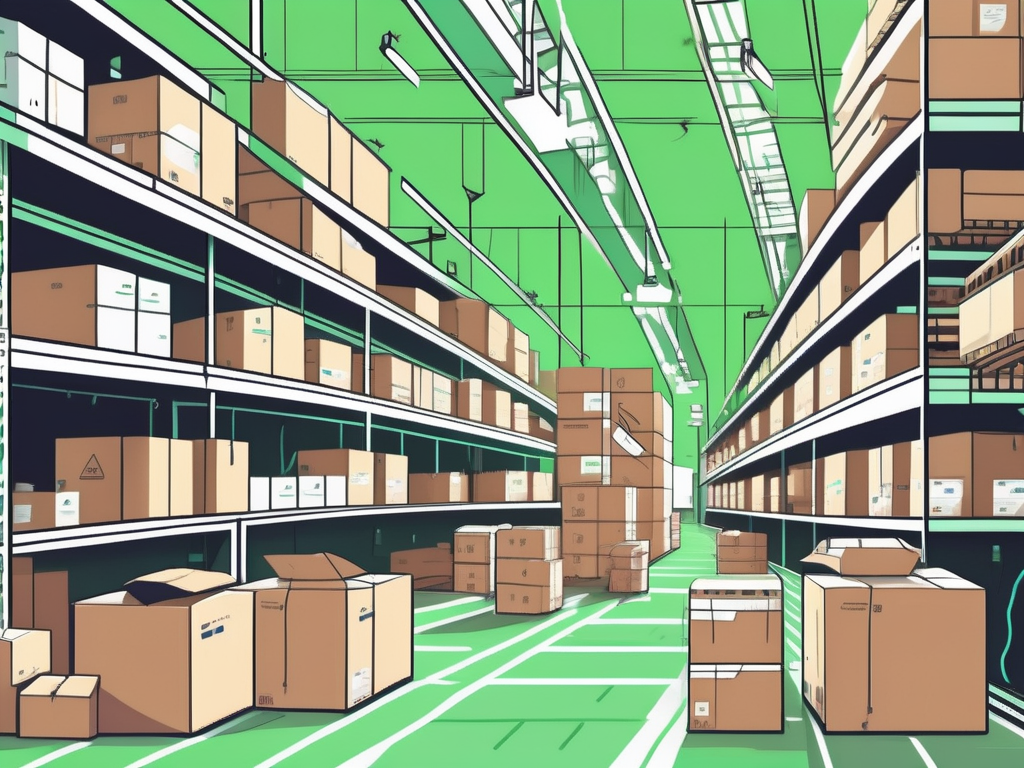
What 'Package Being Processed at Carrier Facility' Means
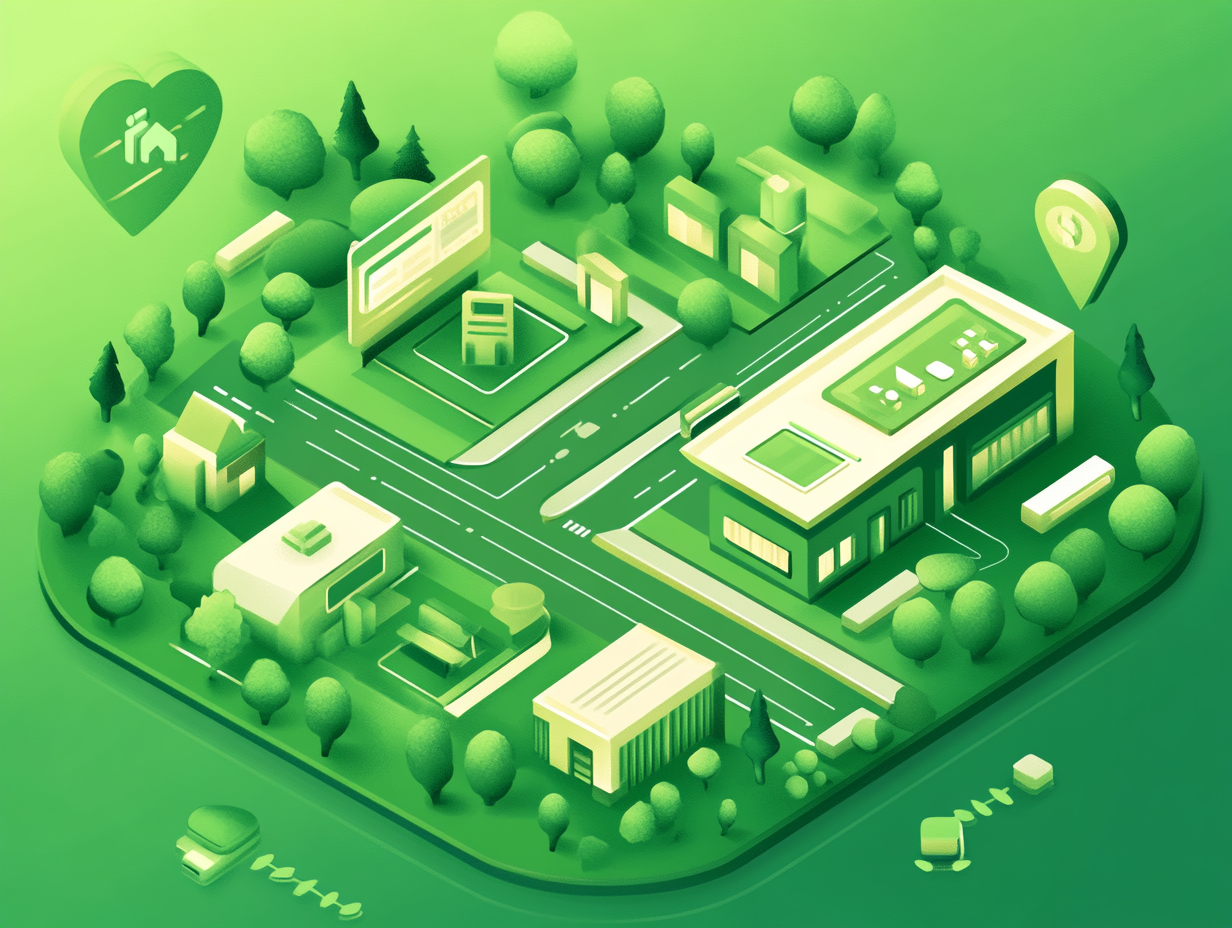
How to Navigate Your Local Carrier Center Efficiently
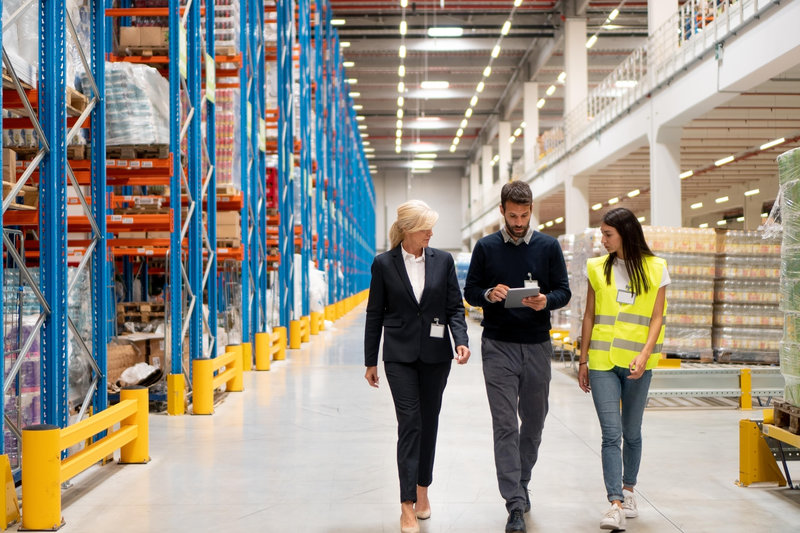
Understanding Warehouse Receiving: Best Practices
- April 2025 (18)
- March 2025 (26)
- February 2025 (26)
- January 2025 (37)
- December 2024 (16)
- November 2024 (23)
- October 2024 (22)
- September 2024 (27)
- August 2024 (9)
- July 2024 (8)
- June 2024 (5)
- May 2024 (8)
- April 2024 (8)
- March 2024 (6)
- February 2024 (6)
- January 2024 (5)
- December 2023 (3)
- November 2023 (3)
- October 2023 (5)
- September 2023 (4)
- August 2023 (2)
- July 2023 (1)
- June 2023 (4)
- March 2023 (2)
- October 2022 (1)
- September 2022 (5)
- August 2022 (4)
- July 2022 (7)
- June 2022 (4)
- May 2022 (4)
- April 2022 (6)
- March 2022 (2)
- February 2022 (1)
- January 2022 (3)
- December 2021 (2)
- November 2021 (4)
- October 2021 (2)
- September 2021 (5)
- August 2021 (4)
- July 2021 (4)
- June 2021 (3)
- May 2021 (2)
- April 2021 (3)
- March 2021 (3)
- February 2021 (3)
- January 2021 (2)
- December 2020 (4)
- November 2020 (2)
- October 2020 (4)
- September 2020 (2)
- July 2020 (5)
- June 2020 (4)
- May 2020 (2)
- April 2020 (2)
- March 2020 (4)
- February 2020 (1)
- December 2019 (1)
- May 2018 (1)
- March 2018 (2)
- February 2018 (3)
- January 2018 (3)
- November 2017 (3)
- July 2017 (4)
- March 2017 (3)
- February 2017 (5)
- January 2017 (3)
- December 2016 (4)
- November 2016 (6)
- October 2016 (6)
- October 2015 (1)
- September 2015 (1)
- June 2015 (3)
- May 2015 (3)
- August 2014 (1)
- July 2014 (1)
- March 2014 (1)
- February 2014 (1)