Share this
Warehouse Management for Ecommerce: Strategies That Drive Real Results
by Shipfusion Team on Apr. 16, 2025
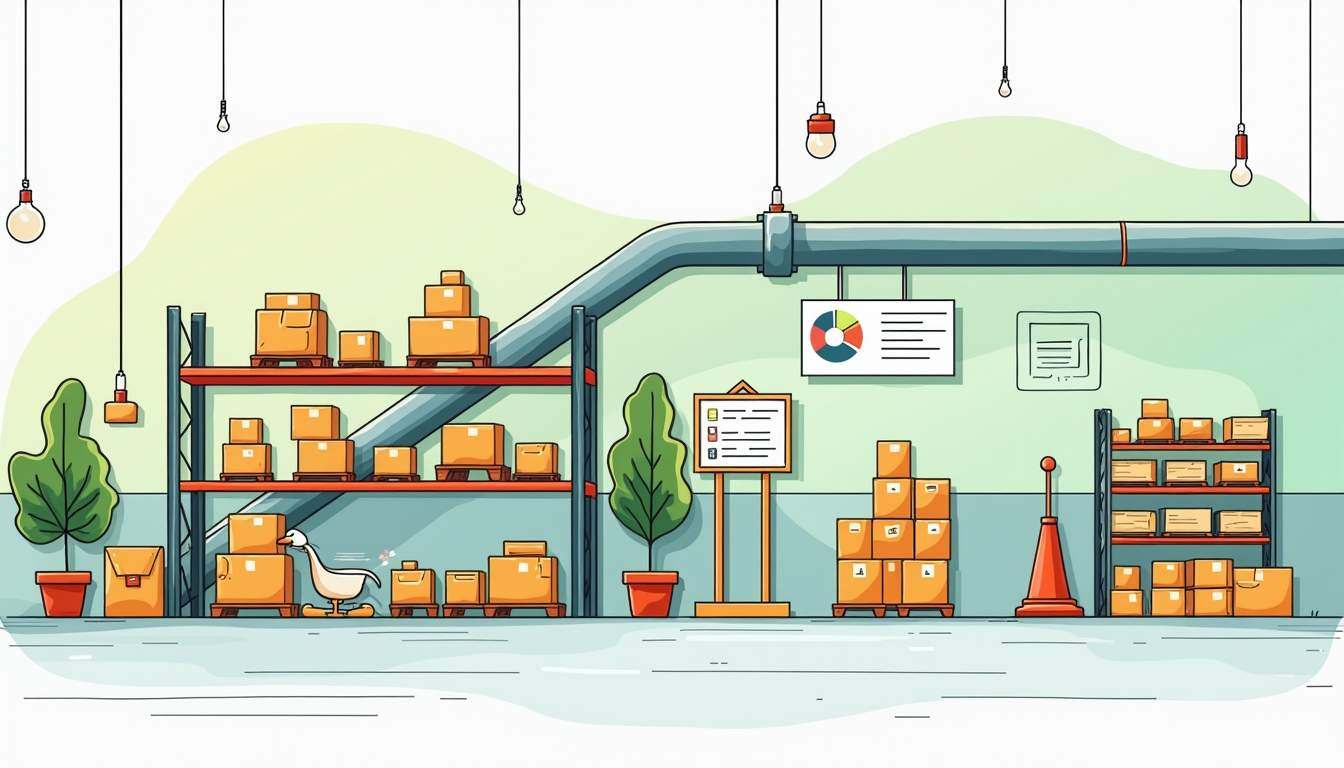
For growing ecommerce businesses, warehouse operations can either be a powerful asset or a hidden liability. As your order volume increases and customer expectations sharpen, managing fulfillment becomes more complex – and more critical. Efficient warehouse management for ecommerce directly impacts shipping speed, order accuracy, operating costs, and ultimately, your brand’s reputation.
This guide breaks down how ecommerce companies can implement scalable, tech-forward strategies that eliminate inefficiencies and support long-term growth. It’s not just about managing space or inventory – it’s about creating an ecommerce fulfillment engine built for speed, precision, and adaptability.
Why Warehouse Efficiency Is a Competitive Advantage
Efficient warehouse management isn’t a cost-cutting measure – it’s a performance multiplier. Ecommerce businesses operating without clear systems, real-time insights, or logical workflows often experience problems like delayed shipments, overselling, or excessive carrying costs. These issues scale quickly as order volumes grow.
The Hidden Costs of Inefficiency
-
Labor Overuse: Disorganized picking and packing leads to wasted labor hours. Without real-time inventory visibility, staff spend time hunting down SKUs or dealing with incorrect orders.
-
Lost Sales: Stockouts caused by inaccurate inventory tracking or slow replenishment mean missed revenue opportunities.
-
Excess Storage Fees: Poor layout planning or overstocking leads to inefficient use of space, driving up costs unnecessarily.
-
Customer Attrition: Long lead times and fulfillment errors frustrate customers, many of whom won’t return after a bad experience.
Conversely, improving warehouse efficiency boosts productivity, shortens lead times, and lowers error rates – all of which contribute to customer retention and profitability.
Building Blocks of Efficient Warehouse Management for Ecommerce
Operational efficiency begins with aligning three core pillars: technology, people, and process. Here's how each one contributes:
1. Implement a Scalable Warehouse Management System (WMS)
A WMS is not just a dashboard – it’s the digital brain of your warehouse. Modern systems do more than track inventory; they integrate with ecommerce platforms (like Shopify, WooCommerce, or Amazon), route orders automatically, and provide real-time data across SKUs and locations.
Key features to prioritize:
-
Real-time inventory tracking across multiple channels and warehouses
-
Barcode and RFID support for fast, accurate scanning
-
Pick-pack-ship workflows with built-in checks
-
Customizable reporting and KPI dashboards
-
Integration with returns and replenishment workflows
2. Design a Logical and Adaptable Warehouse Layout
An efficient layout supports flow – both of people and products. The goal is to minimize travel distance, reduce bottlenecks, and ensure that popular SKUs are easily accessible.
Tactics to consider:
-
SKU Slotting: Place high-volume or fast-moving items closer to the packing station.
-
Zoning: Group inventory by type, temperature sensitivity, or sales velocity.
-
Vertical Storage: Use stackable bins and multi-tier shelving to make full use of cubic space.
-
Clear Signage: Reduce cognitive load by labeling zones and pathways.
Conduct layout audits regularly. As product lines evolve, what worked six months ago may no longer be optimal.
Smart Inventory Management: Less Waste, More Agility
Inventory is a balancing act. Overstocking ties up capital and space. Understocking leads to backorders and lost sales. The key is to stay lean without running dry.
Techniques that support better inventory decisions:
Just-in-Time (JIT) Inventory
JIT minimizes storage needs by ordering goods only when needed. While it reduces holding costs, it requires tight coordination with suppliers and real-time data to avoid disruption.
ABC Analysis
Categorize inventory into three tiers:
-
A-items: High-value, high-frequency SKUs – require constant monitoring.
-
B-items: Moderate value or movement – less oversight but still important.
-
C-items: Low-value, slow-moving – can be stocked in lower quantities or discounted to clear space.
Safety Stock Calculation
Even with JIT, keep a calculated buffer for critical SKUs. Factor in lead time variability and demand fluctuations to prevent stockouts during peak sales periods.
Pro tip: Integrate your WMS with forecasting tools that analyze sales trends, seasonality, and marketing campaigns to predict inventory needs.
Staff Training: The Human Element of Efficiency
No tech investment can succeed without a well-trained team. Human error remains a leading cause of fulfillment issues. Training shouldn't be a one-time event – it should be continuous, contextual, and measured.
Focus areas for training programs:
-
System Proficiency: Ensure staff are fluent in your WMS and scanning tools.
-
Standard Operating Procedures (SOPs): Reinforce best practices for picking, packing, labeling, and returns.
-
Cross-Training: Build agility by training employees on multiple tasks, reducing downtime when order volumes spike.
-
Safety Protocols: Create a culture of safety to reduce accidents and associated costs.
Implementation Tip: Develop visual training guides and quick-reference checklists for new hires and seasonal workers.
Technology That Drives Operational Efficiency
Beyond a WMS, consider additional tools that further streamline operations:
Barcode and RFID Scanning
-
Reduces manual data entry and errors
-
Accelerates picking and receiving
-
Improves traceability for lot or batch tracking
Automated Picking Solutions
-
Pick-to-light systems guide employees with illuminated indicators
-
Voice-directed picking improves speed while keeping hands free
-
Mobile carts with tablets streamline multi-order batching
Robotics and Automation
Automation is no longer reserved for enterprise-scale warehouses. Modular solutions are available for mid-sized ecommerce businesses looking to reduce labor strain and scale efficiently.
Examples:
-
Autonomous mobile robots (AMRs) that transport bins to pack stations
-
Conveyor systems for high-volume SKU movement
-
Robotic arms for repetitive picking or sorting tasks
Remember, while automation has upfront costs, it delivers compounding returns through labor savings, uptime consistency, and throughput gains.
Performance Measurement: Data-Driven Improvement
Efficient warehouse management for ecommerce isn’t static. It requires continuous monitoring and iteration. Tracking the right metrics helps pinpoint inefficiencies and track progress over time.
Essential KPIs to track:
-
Order Cycle Time: Time from order placement to shipment. Shorter times mean faster cash cycles and happier customers.
-
Order Accuracy Rate: Percentage of error-free orders. Aim for 99.9% or higher.
-
Inventory Turnover Ratio: Indicates how quickly inventory is sold and replaced. High turnover suggests optimized stock levels.
-
Warehouse Capacity Utilization: Measures space efficiency. Underutilization wastes resources; overutilization leads to clutter and risk.
-
Cost per Order: Helps assess overall fulfillment efficiency, including labor, materials, and overhead.
Efficient Warehouse Management for Ecommerce: Scale with Confidence
Your warehouse is a critical engine behind your customer experience and brand promise. Efficient warehouse management for ecommerce enables ecommerce businesses to ship faster, reduce costs, and respond flexibly to demand shifts. But efficiency doesn’t happen by accident. It requires smart systems, proactive strategy, and a commitment to continuous improvement.
Whether you're fulfilling 100 orders a day or 10,000, Shipfusion can help you turn fulfillment into a growth driver. Our white-glove service model combines industry-leading technology, real-time data visibility, and an expert support team to make fulfillment seamless. With over 1,000,000 square feet of warehousing across North America and proprietary tools built for ecommerce, we handle everything from storage to shipping to returns so you can stay focused on scaling your brand.
Get pricing today and discover how efficient warehouse management can take your ecommerce business to the next level.
Share this
You May Also Like
These Related Articles
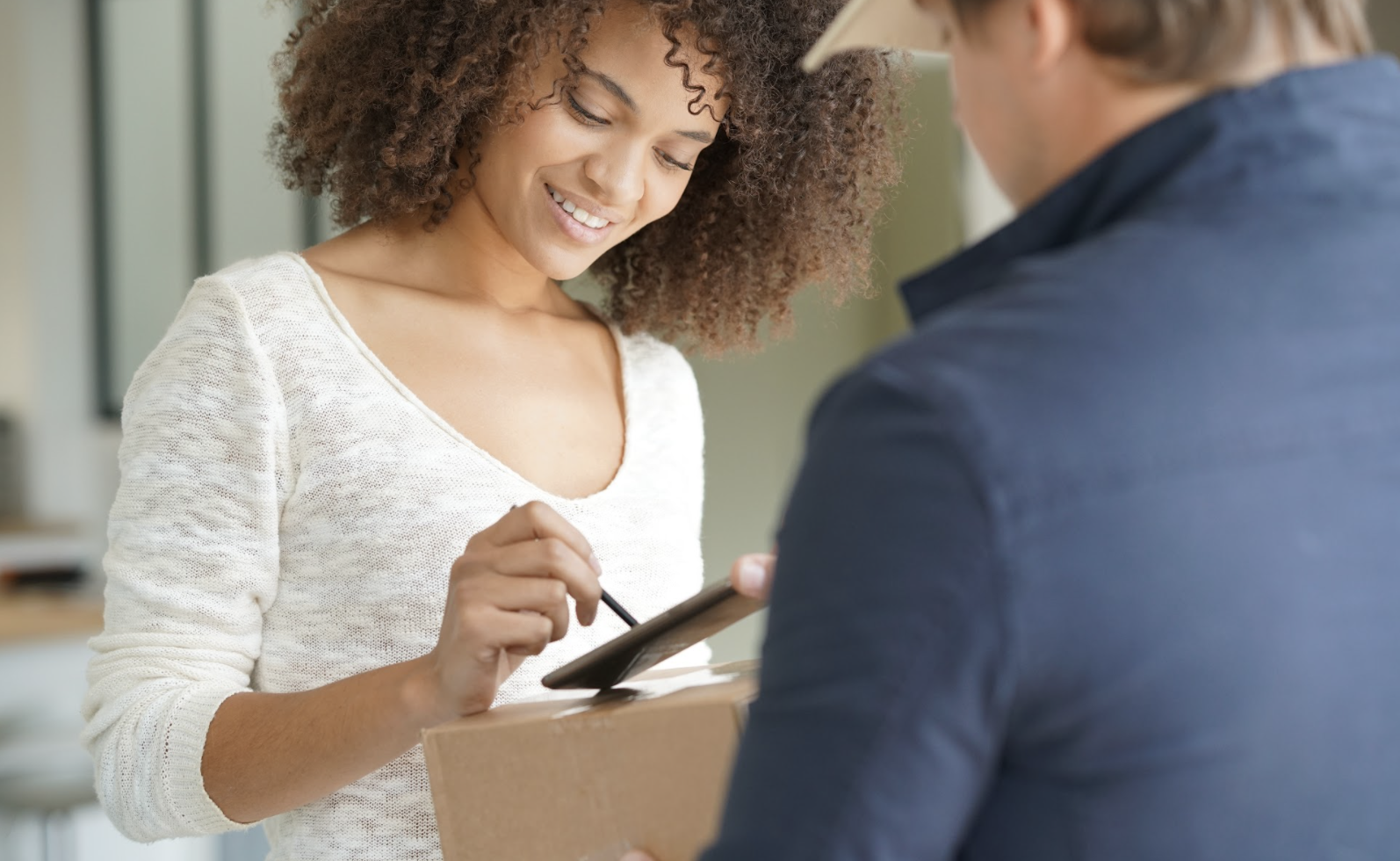
Importance of Product Delivery Options in Online Retail Environments
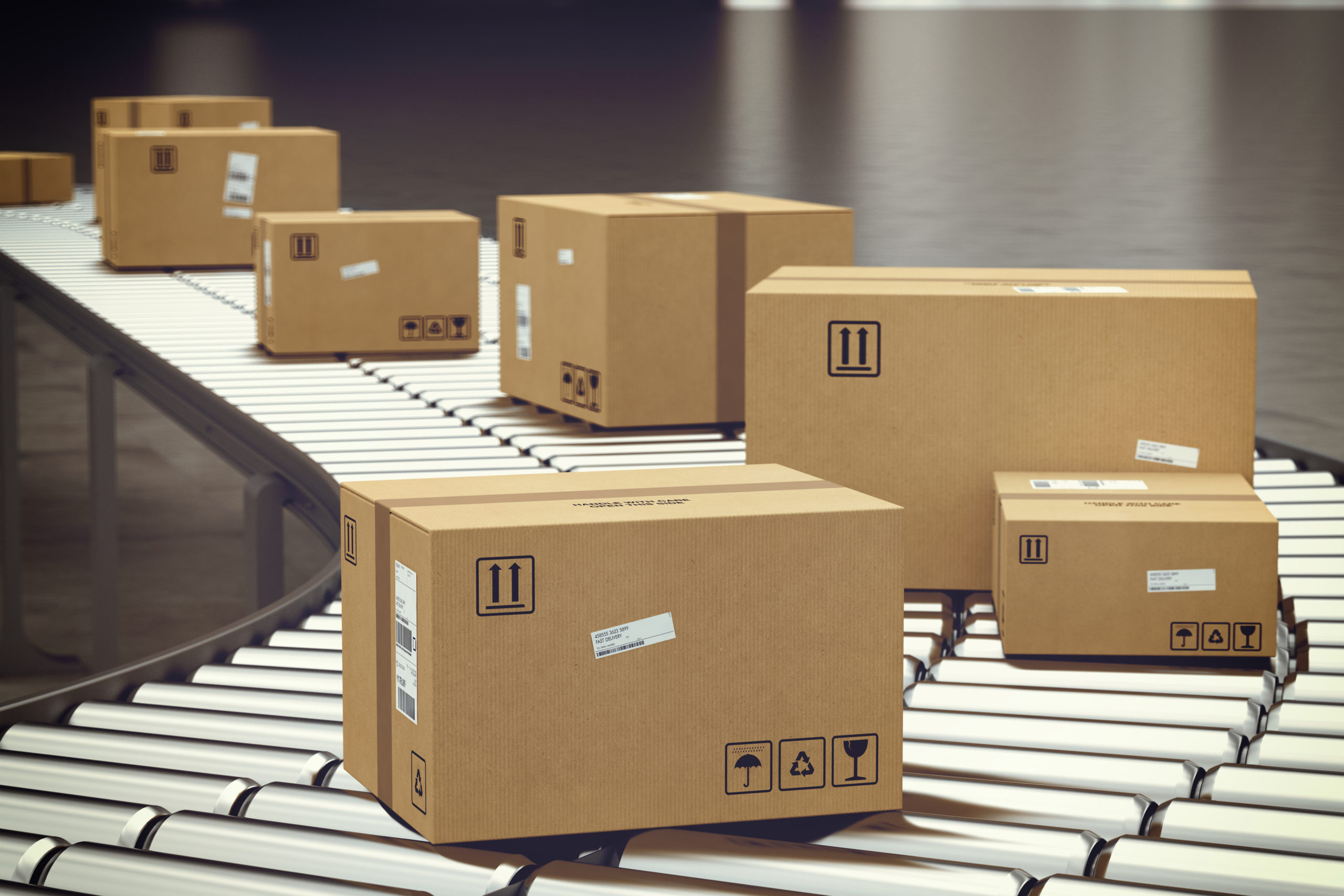
Reasons To Get The Order Fulfillment Center Edge
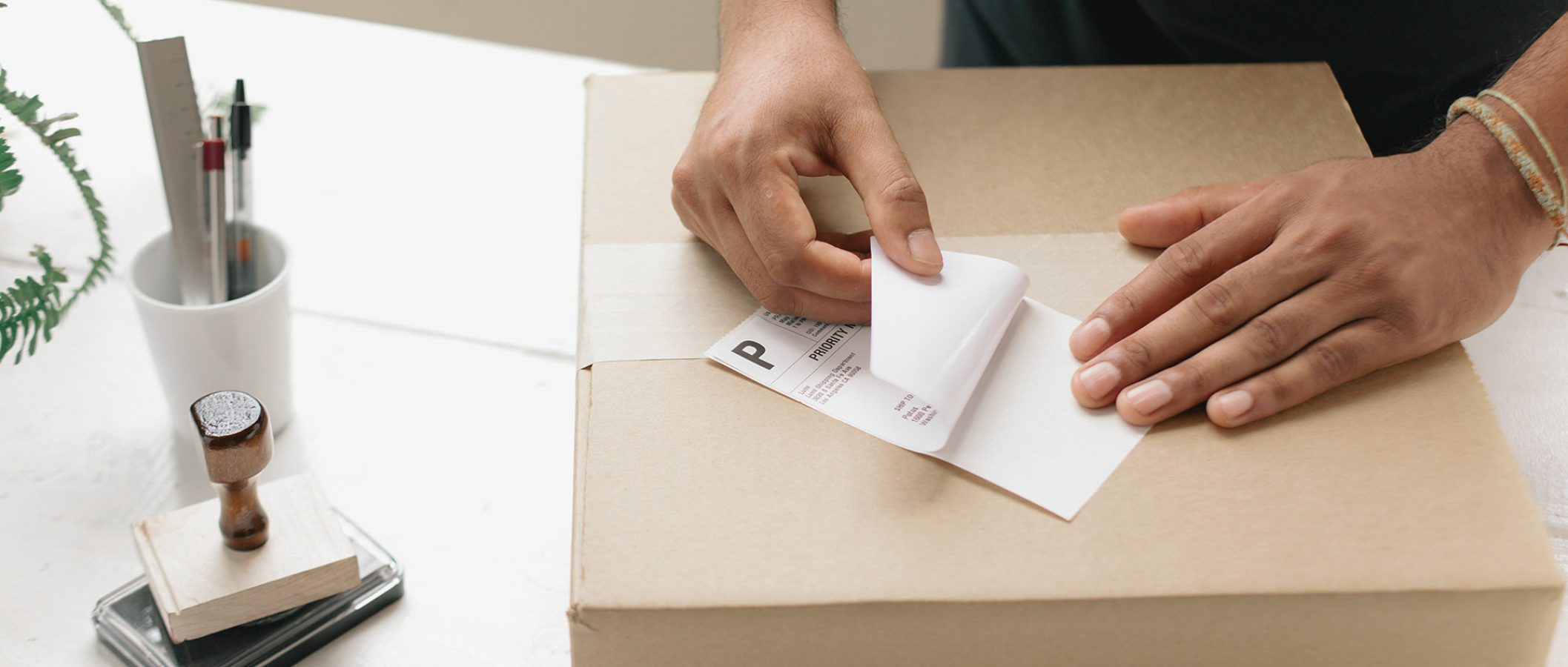
Here’s How You Create The Perfect eCommerce Returns Policy
- April 2025 (18)
- March 2025 (26)
- February 2025 (26)
- January 2025 (37)
- December 2024 (16)
- November 2024 (23)
- October 2024 (22)
- September 2024 (27)
- August 2024 (9)
- July 2024 (8)
- June 2024 (5)
- May 2024 (8)
- April 2024 (8)
- March 2024 (6)
- February 2024 (6)
- January 2024 (5)
- December 2023 (3)
- November 2023 (3)
- October 2023 (5)
- September 2023 (4)
- August 2023 (2)
- July 2023 (1)
- June 2023 (4)
- March 2023 (2)
- October 2022 (1)
- September 2022 (5)
- August 2022 (4)
- July 2022 (7)
- June 2022 (4)
- May 2022 (4)
- April 2022 (6)
- March 2022 (2)
- February 2022 (1)
- January 2022 (3)
- December 2021 (2)
- November 2021 (4)
- October 2021 (2)
- September 2021 (5)
- August 2021 (4)
- July 2021 (4)
- June 2021 (3)
- May 2021 (2)
- April 2021 (3)
- March 2021 (3)
- February 2021 (3)
- January 2021 (2)
- December 2020 (4)
- November 2020 (2)
- October 2020 (4)
- September 2020 (2)
- July 2020 (5)
- June 2020 (4)
- May 2020 (2)
- April 2020 (2)
- March 2020 (4)
- February 2020 (1)
- December 2019 (1)
- May 2018 (1)
- March 2018 (2)
- February 2018 (3)
- January 2018 (3)
- November 2017 (3)
- July 2017 (4)
- March 2017 (3)
- February 2017 (5)
- January 2017 (3)
- December 2016 (4)
- November 2016 (6)
- October 2016 (6)
- October 2015 (1)
- September 2015 (1)
- June 2015 (3)
- May 2015 (3)
- August 2014 (1)
- July 2014 (1)
- March 2014 (1)
- February 2014 (1)