Share this
Cost to Manufacture Broken Down Piece-By-Piece
by Shipfusion Team on Mar. 12, 2025
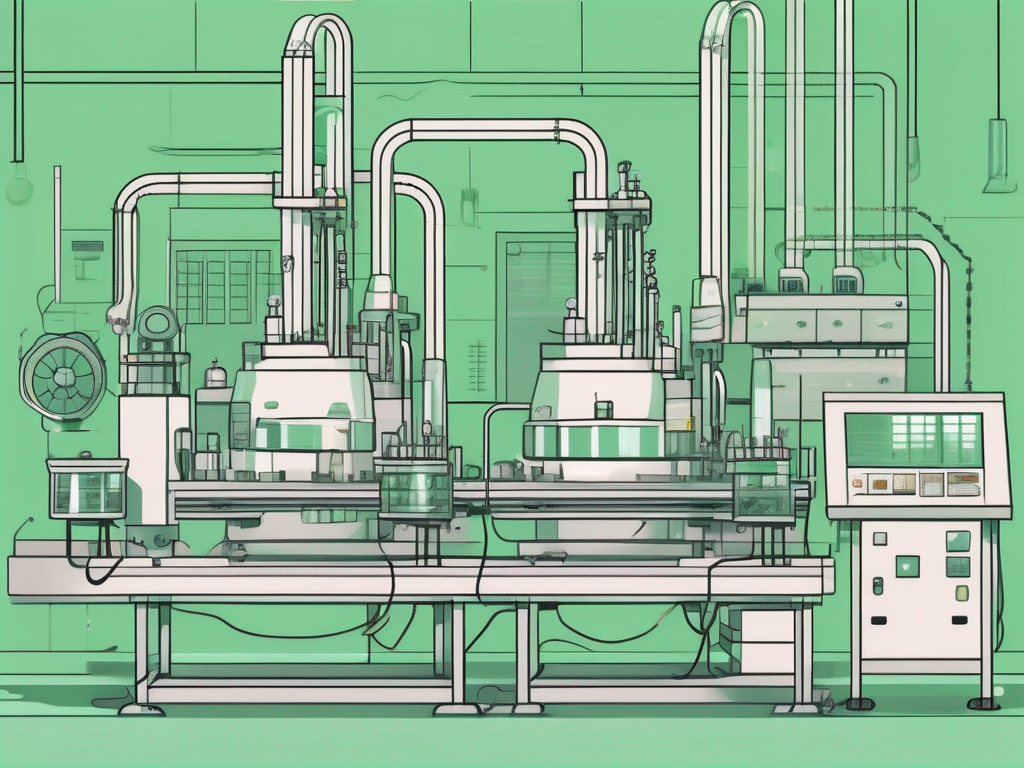
The manufacturing sector is a vital part of the global economy, influencing everything from employment rates to the price of goods. Understanding the costs associated with manufacturing is essential for organizations aiming to maintain profitability while delivering quality products. This guide provides an overview of cost to manufacture in 2024, covering essential areas from labor to technology.
What's Included In Cost to Manufacture?
Manufacturing costs can be broadly categorized into three primary types: direct materials, direct labor, and manufacturing overhead. Each type contributes to the overall expense of producing goods, affecting pricing strategies and profit margins. A clear understanding of these costs allows manufacturers to optimize their operations.
The Basics of Manufacturing Costs
At its core, the total manufacturing cost is the sum of all expenses incurred in the production process. These costs can fluctuate significantly based on factors like production volume, resource availability, and technological advancements. For example, a facility operating at limited capacity may face higher per-unit costs compared to one running at full capacity. This concept is crucial for businesses to grasp, as it can influence decisions on scaling production or investing in more efficient machinery.
Different industries may experience varying cost structures. For instance, electronics manufacturing typically involves higher material costs due to the necessity of specialized components, while textile production may have more significant labor costs associated with skilled workers. Understanding these nuances allows companies to tailor their financial strategies to meet the specific demands of their sector, ensuring they remain competitive in the marketplace.
While understanding manufacturing costs is crucial, addressing the issues that lead to inefficiencies can significantly enhance operations. Implementing a collaborative root cause analysis approach aids in systematically identifying underlying problems within production processes. Utilizing root cause analysis templates can streamline this problem-solving effort, leading to increased cost efficiency and improved productivity as teams work together to strategize innovative solutions.
Key Components of Manufacturing Costs
The breakdown of manufacturing costs reveals several key components. Direct materials refer to the raw inputs used to create a product, while direct labor encompasses wages paid to workers directly involved in the production process. Manufacturing overhead includes indirect costs such as utilities, rent, and equipment depreciation that are not directly attributable to the product but are essential for continuous operations. This overhead can often be a hidden drain on resources, making it critical for managers to monitor and manage these expenses effectively.
Additionally, fixed and variable costs play a significant role. Fixed costs remain constant regardless of production levels, such as lease agreements, whereas variable costs fluctuate based on the production volume, like raw materials used. This distinction is vital for budgeting and forecasting, as it helps businesses predict their financial performance under different production scenarios. Moreover, understanding the interplay between these costs can lead to more informed decisions about pricing, outsourcing, and inventory management, ultimately impacting the bottom line.
Another important aspect of manufacturing costs is the impact of supply chain dynamics. Fluctuations in supplier pricing, changes in shipping costs, and global economic conditions can all affect the cost of direct materials. For example, a sudden increase in oil prices can lead to higher transportation costs, which in turn raises the overall cost of materials. Manufacturers must stay vigilant and adaptable to these changes, often employing strategies such as bulk purchasing or diversifying suppliers to mitigate risks and maintain cost efficiency.
The Role of Labor In Cost to Manufacture
Labor is one of the most significant components of manufacturing costs. Understanding how labor expenses impact overall production is vital for effective financial management. Managing these costs effectively can lead to improved profitability and competitive advantage.
Labor Costs and Productivity
Labor costs comprise wages, benefits, and overtime payments. High labor costs can squeeze margins, particularly in industries with slim profit margins, such as food manufacturing. Conversely, a highly productive workforce can lead to lower per-unit labor costs through increased output, enabling companies to maintain price competitiveness.
Automation has transformed labor dynamics in many factories, allowing organizations to reduce reliance on manual labor while enhancing productivity. For instance, automotive manufacturers have implemented robotics in assembly lines to reduce time and human error, significantly decreasing labor costs over time. The integration of artificial intelligence and machine learning also plays a crucial role in optimizing labor allocation, predicting maintenance needs, and streamlining workflows, which further enhances productivity and reduces downtime.
Strategies for Managing Labor Costs
Organizations can adopt several strategies to manage labor costs effectively. Training programs that enhance employee skills may lead to increased efficiency and productivity. Instead of hiring more staff, businesses can invest in upskilling existing employees, maximizing workforce potential. This not only fosters a culture of continuous improvement but also boosts employee morale, as workers feel more valued and engaged in their roles.
Implementing flexible work arrangements can also lead to labor cost savings. For instance, companies may offer remote work options that reduce facility overhead while maintaining employee satisfaction. Such arrangements can result in lower operational costs without sacrificing productivity. Additionally, leveraging technology for remote collaboration can facilitate seamless communication and project management, ensuring that teams remain cohesive and focused on their objectives, regardless of their physical location. This adaptability can be particularly beneficial in times of economic uncertainty, allowing businesses to respond swiftly to changes in market demand while managing labor costs effectively.
Material Costs In Manufacturing
Material costs typically account for the largest share of total manufacturing expenses. Understanding the types of material costs and how to manage them is essential for achieving cost efficiency and maintaining healthy margins.
Types of Material Costs
Material costs can be divided into direct and indirect material costs. Direct material costs are the expenses associated with raw materials that are directly involved in producing a product, while indirect materials may include supplies used in the production process but not directly traceable to a specific product.
The volatility of raw material prices presents a significant challenge. For instance, fluctuations in steel prices can dramatically affect the manufacturing costs in the construction and automotive sectors. Manufacturers often need to anticipate these price changes and devise strategies to mitigate their impact. This unpredictability can also lead to a ripple effect in pricing across the supply chain, affecting everything from supplier contracts to end-consumer prices. Consequently, staying informed about global market trends and geopolitical factors that influence material availability is crucial for manufacturers aiming to maintain competitive pricing.
Reducing Material Costs
To effectively control material costs, companies can implement several cost-reduction strategies. One method involves negotiating long-term contracts with suppliers to secure favorable prices and mitigate the effects of market volatility. Additionally, investing in alternative materials or sustainable sourcing can lead to cost savings while promoting environmental responsibility. For example, some manufacturers are exploring biodegradable materials or recycled components, which not only reduce costs but also appeal to a growing consumer base that values sustainability.
Implementing just-in-time inventory systems can improve cash flow and reduce storage costs, which are both valuable in maintaining lower material costs. This approach ensures materials are only ordered as needed, reducing excess inventory and associated carrying costs. Furthermore, leveraging technology such as advanced analytics and artificial intelligence can enhance demand forecasting, allowing manufacturers to optimize their purchasing strategies. By accurately predicting material needs, companies can minimize waste and avoid the pitfalls of overstocking, ultimately leading to a more streamlined and cost-effective manufacturing process.
Overhead Costs In Manufacturing
Overhead costs are essential to understand because they can significantly affect the total cost of production. Identifying and controlling these costs is vital for maintaining a competitive edge in the marketplace.
Identifying Overhead Costs
Overhead costs can encompass a wide variety of expenses including utilities, maintenance, rent, insurance, and administrative salaries. Many businesses find that overhead costs can be disproportionately high compared to variable costs, thus requiring a thorough examination of all associated expenses.
Establishing a methodical approach to classify and track overhead costs can help organizations pinpoint unnecessary expenditures. By performing regular audits and reviewing expense reports, manufacturers can identify areas for potential savings. This includes reassessing service contracts and utility providers to identify more cost-effective options. Additionally, implementing a robust accounting software system can facilitate better tracking and analysis of overhead costs, allowing for real-time insights into spending patterns and trends.
Another effective tactic is to engage employees in the cost-reduction process. By fostering a culture of cost awareness, manufacturers can encourage staff to identify inefficiencies and suggest improvements. Workshops and training sessions can empower employees to take ownership of their roles in managing overhead, leading to innovative solutions that may not have been previously considered.
Controlling Overhead Costs
Control of overhead costs can involve streamlining operational processes to increase efficiency. Introducing energy-efficient technologies may significantly lower utility bills. For example, upgrading to LED lighting or investing in automated climate control systems can lead to substantial savings over time.
Another strategy for controlling overhead is consolidating spaces or relocating to areas with lower operational costs. Manufacturers may find it beneficial to explore alternative locations where expenses are reduced, thus enhancing overall profitability. Furthermore, negotiating long-term contracts with suppliers can also shield manufacturers from price fluctuations, providing more predictable budgeting for overhead expenses.
In addition to these strategies, manufacturers can also consider implementing a just-in-time inventory system. This approach minimizes storage costs and reduces waste, thereby lowering overhead expenses associated with inventory management. By synchronizing production schedules with demand, manufacturers can optimize their resources and further control costs. Emphasizing continuous improvement and regularly revisiting overhead management strategies can ensure that companies remain agile and responsive to changing market conditions.
Technology and Manufacturing Costs
In an era where technology rapidly advances, understanding its implications on manufacturing costs is crucial for businesses aiming to stay competitive. Technology can introduce efficiencies that lead to reduced operational expenses. As companies increasingly rely on digital solutions, the integration of technology into manufacturing processes is no longer a luxury but a necessity for survival in a global marketplace.
Impact of Technology on Manufacturing Costs
Technology can dramatically alter production processes, leading to improved efficiency and reduced costs. Automated systems, data analytics, and AI are transforming how manufacturers operate.
Such a proactive approach not only saves money but also extends the lifespan of machinery, allowing companies to maximize their return on investment.
Manufacturing Execution Systems (MES) are another technological innovation that enables real-time tracking of production processes, allowing for better resource management and cost control. By utilizing such technologies, businesses can gain greater visibility into operations and make informed decisions that enhance overall efficiency. Moreover, the integration of augmented reality (AR) in training and maintenance processes is becoming increasingly popular, enabling workers to visualize complex tasks and reduce errors, which further contributes to cost savings.
Future Trends In Manufacturing Technology
Looking forward, several trends in manufacturing technology are anticipated to further shake up cost structures. Increased adoption of IoT (Internet of Things) devices is expected, allowing organizations to gather extensive data on their production processes. This data can lead to enhanced decision-making capabilities and cost efficiencies. For instance, smart sensors can monitor equipment health in real-time, providing insights that can optimize energy consumption and reduce waste, thereby lowering operational costs significantly.
Additionally, more manufacturers are exploring the potential of additive manufacturing, commonly known as 3D printing. This technology allows for the creation of components on-demand, reducing inventory costs and waste. As these technologies develop, manufacturers will need to adapt to remaining competitive while managing their costs effectively. The rise of digital twins—virtual replicas of physical systems—also presents opportunities for manufacturers to simulate and analyze processes before implementation, leading to smarter investments and strategic planning. With these advancements, the landscape of manufacturing will continue to evolve, pushing companies to innovate while keeping a keen eye on their cost structures.
Understanding manufacturing costs is pivotal for successful operations. From labor and materials to overhead and technology, each component plays a significant role in the overall expense of production. By applying effective strategies for managing these costs, manufacturers can enhance profitability and future-proof their businesses against emerging challenges. As the industry embraces these technological advancements, the potential for growth and efficiency becomes boundless, paving the way for a new era of manufacturing excellence.
Make Your Cost to Manufacture and Ship Smarter In 2025
At Shipfusion, we understand the critical role ecommerce fulfillment plays in your cost management strategy. Our tailored solutions—such as advanced inventory management, real-time data analytics, and streamlined logistics—help businesses align their manufacturing efforts with efficient fulfillment processes. Whether you're scaling production or adapting to changing market demands, Shipfusion provides the expertise and infrastructure to reduce overhead, improve operational efficiency, and deliver exceptional customer experiences.
Ready to take your manufacturing and fulfillment strategies to the next level? Contact Shipfusion today and discover how we can help you get and stay ahead.
Share this
You May Also Like
These Related Articles
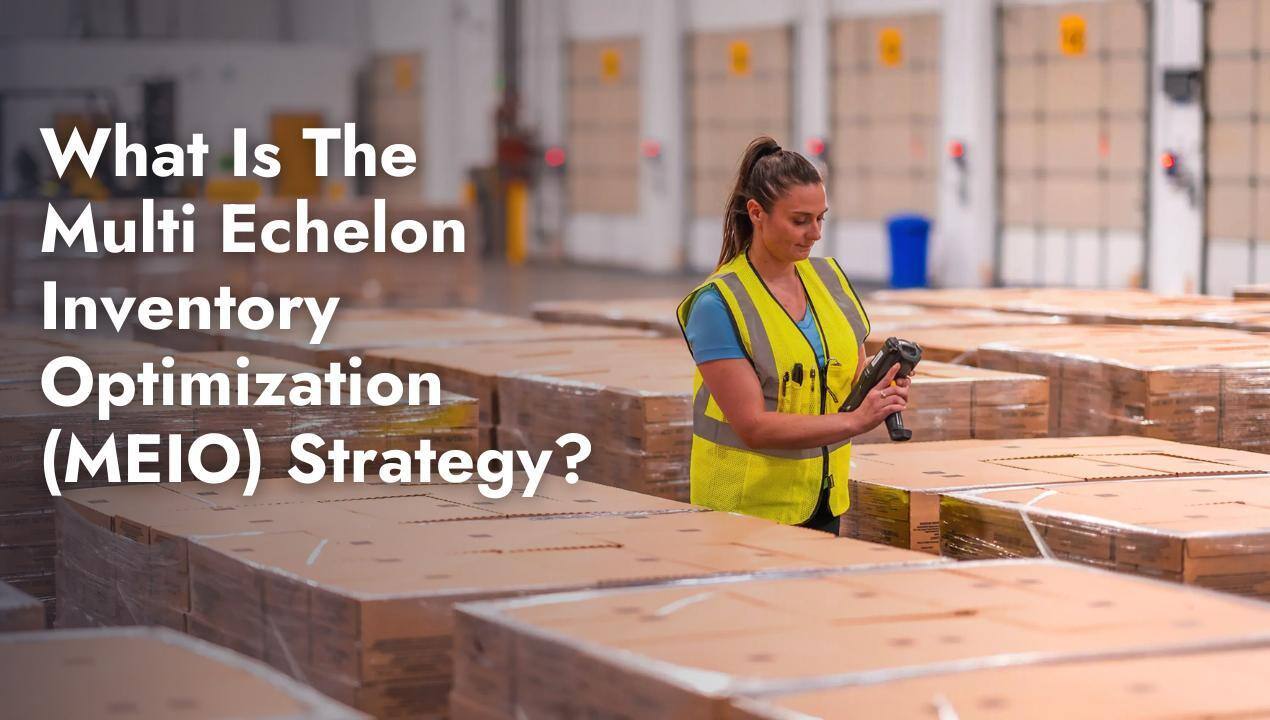
What Is the Multi Echelon Inventory Optimization (MEIO) Strategy?
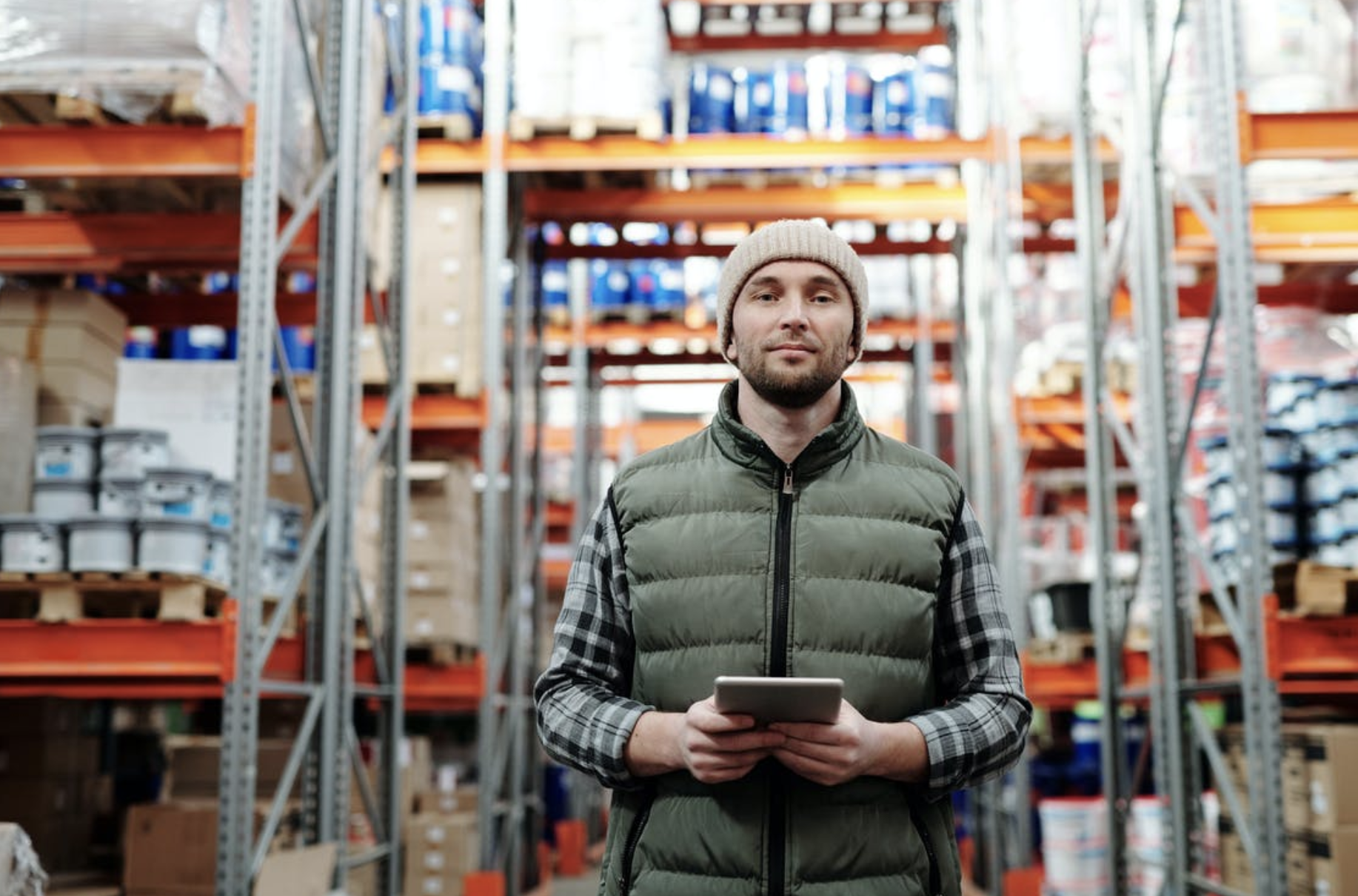
How to Utilize Supply Chain Analytics
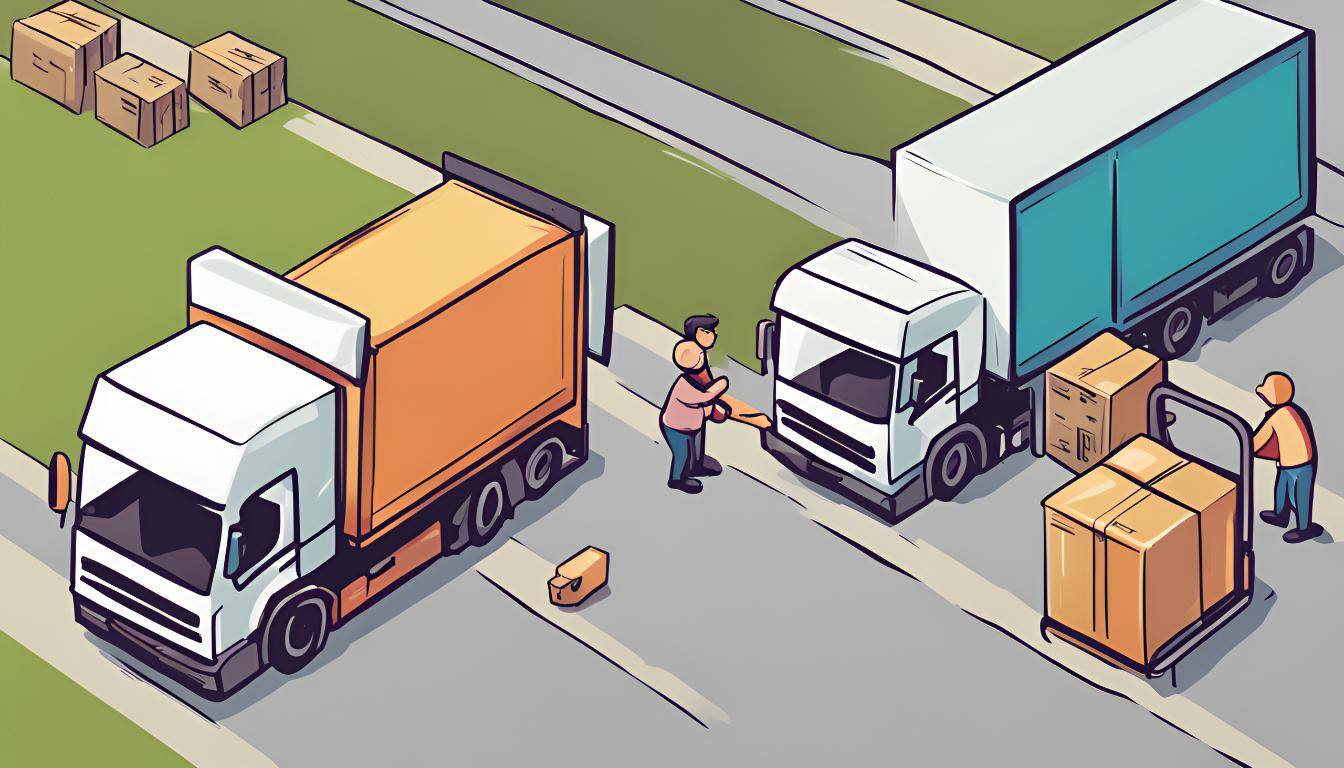
How to Nail Handover to a 3PL
- July 2025 (2)
- June 2025 (22)
- May 2025 (27)
- April 2025 (27)
- March 2025 (26)
- February 2025 (26)
- January 2025 (35)
- December 2024 (16)
- November 2024 (22)
- October 2024 (22)
- September 2024 (27)
- August 2024 (9)
- July 2024 (8)
- June 2024 (5)
- May 2024 (8)
- April 2024 (8)
- March 2024 (6)
- February 2024 (6)
- January 2024 (5)
- December 2023 (3)
- November 2023 (3)
- October 2023 (5)
- September 2023 (4)
- August 2023 (2)
- July 2023 (1)
- June 2023 (4)
- March 2023 (2)
- October 2022 (1)
- September 2022 (5)
- August 2022 (4)
- July 2022 (7)
- June 2022 (4)
- May 2022 (4)
- April 2022 (6)
- March 2022 (2)
- February 2022 (1)
- January 2022 (3)
- December 2021 (2)
- November 2021 (4)
- October 2021 (2)
- September 2021 (5)
- August 2021 (4)
- July 2021 (4)
- June 2021 (3)
- May 2021 (2)
- April 2021 (3)
- March 2021 (3)
- February 2021 (3)
- January 2021 (2)
- December 2020 (4)
- November 2020 (2)
- October 2020 (4)
- September 2020 (2)
- July 2020 (5)
- June 2020 (4)
- May 2020 (2)
- April 2020 (2)
- March 2020 (4)
- February 2020 (1)
- December 2019 (1)
- May 2018 (1)
- March 2018 (2)
- February 2018 (3)
- January 2018 (3)
- November 2017 (3)
- July 2017 (4)
- March 2017 (3)
- February 2017 (5)
- January 2017 (3)
- December 2016 (4)
- November 2016 (6)
- October 2016 (6)
- October 2015 (1)
- September 2015 (1)
- June 2015 (3)
- May 2015 (3)
- August 2014 (1)
- July 2014 (1)
- March 2014 (1)
- February 2014 (1)