Share this
Defining 'Arrived to Facility' In Ecommerce Logistics
by Shipfusion Team on Apr. 11, 2025
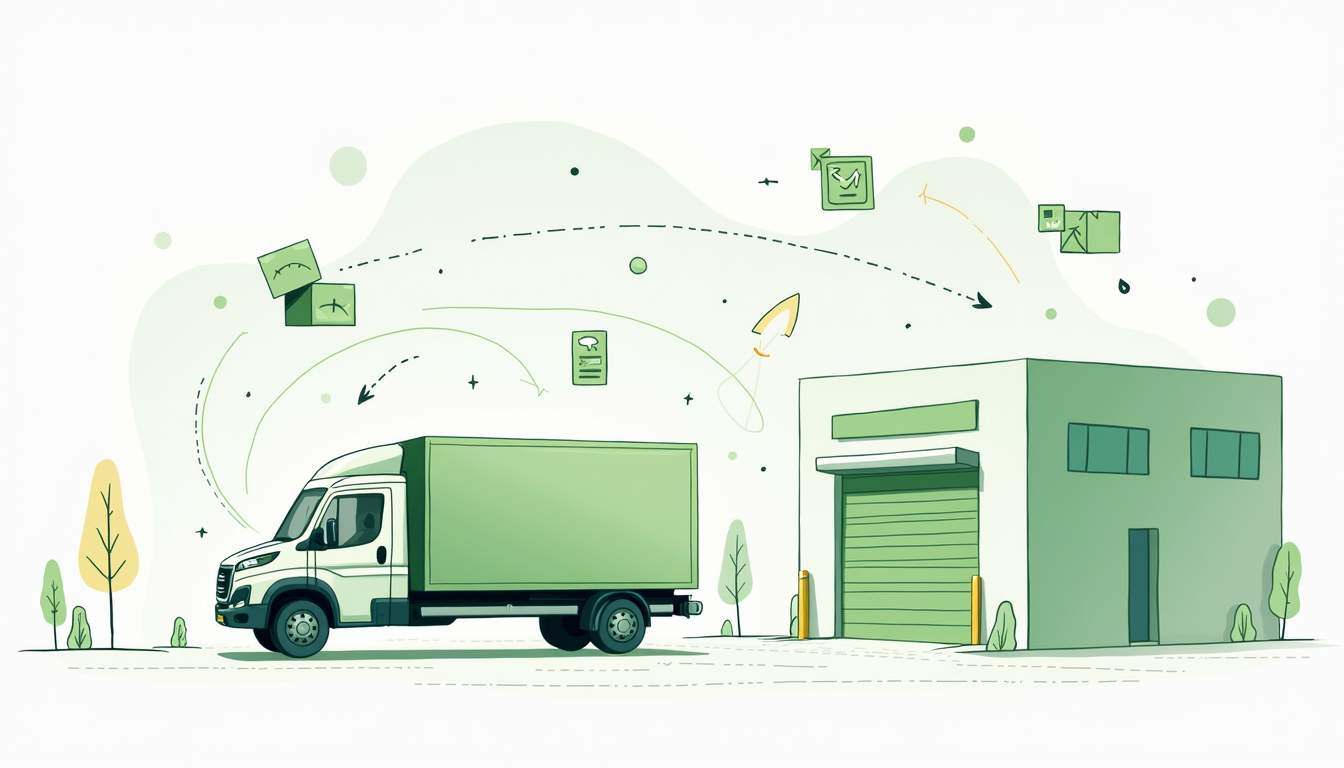
In ecommerce logistics, every status update has a purpose. One of the most pivotal updates in the order fulfillment process is the 'Arrived to Facility' notification. This simple message signals more than the physical arrival of goods — it’s a key operational checkpoint that affects inventory accuracy, order fulfillment speed, and overall customer satisfaction. Whether you're managing inbound shipments from suppliers or overseeing returns from customers, understanding the impact of this status can help you tighten your supply chain and avoid common bottlenecks.
What Does ‘Arrived to Facility’ Mean?
When a shipment is marked as ‘Arrived to Facility,’ it indicates that the goods have successfully reached a designated warehouse, distribution center, or fulfillment facility. This is the moment when control over the shipment is officially transferred from the carrier or supplier to the warehouse operator. From here, the focus shifts from transportation to inventory processing and order readiness. For ecommerce brands, this status triggers essential next steps like inventory intake, quality control checks, and storage allocation — all of which have a direct impact on order fulfillment timelines.
Why the ‘Arrived to Facility’ Status Is Important
This logistics milestone isn’t just an informational update; it plays a direct role in how efficiently your business can operate.
Here’s why it matters:
1. Inventory Accuracy and Visibility
Once goods arrive at a fulfillment facility, they can’t be shipped to customers until they’re properly received and logged into the warehouse management system (WMS).
The ‘Arrived to Facility’ status sets off this process:
- Stock Updates: The arrival triggers inventory adjustments in real time, providing your team with accurate stock counts.
- Lot Tracking and Quality Control: Quality control teams like Shipfusion's perform inspection protocols at this stage to verify product condition and lot details.
- Storage Allocation: Storage allocation is about knowing what’s arrived allows warehouse teams to assign optimal storage locations, reducing mispicks and ensuring fast retrieval.
2. Fulfillment Speed and Order Readiness
For ecommerce businesses, fulfillment delays are often linked to gaps in inbound visibility. The moment a product arrives at the facility, the clock starts ticking.
Effective handling of this status leads to:
- Faster Order Turnarounds: Goods that are promptly received and logged can move quickly into active inventory, ready for order picking and packing.
- Clear Customer Communication: Real-time status updates allow customer service teams to provide accurate delivery timelines.
- Efficient Returns Processing: For returned items, 'Arrived to Facility' signals the start of return inspections and restocking procedures.
3. Operational Planning
Inbound arrival updates aren’t just for warehouse teams.
Accurate ‘Arrived to Facility’ data helps businesses:
- Forecast Inventory Levels: By tracking arrival times and quantities, brands can adjust marketing and sales campaigns to match inventory availability.
- Schedule Labor Efficiently: Knowing when large shipments will arrive allows fulfillment centers to allocate staff without over- or under-scheduling.
- Manage Vendor Performance: Timely arrivals provide a metric for evaluating vendor reliability and carrier performance.
Common Challenges Associated with ‘Arrived to Facility’
Despite its benefits, this milestone can introduce logistical challenges if not managed properly. Here are some of the most frequent issues ecommerce businesses face:
Unexpected Delays
Shipment arrival times aren’t always predictable.
Delays can result from:
- Weather Disruptions: Severe conditions can halt transportation routes.
- Customs Clearance: International shipments may face hold-ups at customs.
- Documentation Errors: Incorrect shipping paperwork can delay processing.
Our recommended solution? Implement real-time tracking tools and proactive communication with suppliers and carriers. Shipfusion, for instance, uses integrated software to monitor inbound shipments and flag delays early.
Damaged or Incomplete Shipments
Products can arrive damaged, or shipments may be missing items. If unchecked, this can lead to inaccurate inventory counts and order delays.
We suggest establishing a standardized inspection process upon arrival. Fulfillment providers like Shipfusion conduct thorough inbound inspections to identify damages or discrepancies immediately.
Data Disconnects Between Systems
If your ecommerce platform, supplier, and fulfillment provider aren’t aligned, the ‘Arrived to Facility’ status may not update in real time — leaving you and your customers in the dark. Ensure that your WMS and ecommerce systems are integrated to automatically reflect status changes and inventory updates.
Best Practices for Managing the ‘Arrived to Facility’ Process
To maximize efficiency and avoid delays at this critical stage, consider implementing these best practices:
Leverage Advanced Technology
Modern fulfillment centers and warehouses rely on WMS integrations and tracking tools to streamline arrival updates.
Here’s how technology supports smoother operations:
- Real-Time Tracking: GPS, RFID, and barcode scanning tools improve inbound visibility.
- Automated Notifications: Internal teams and ecommerce platforms can receive instant alerts when shipments arrive.
- Data Analytics: Tracking inbound arrival patterns helps identify bottlenecks and improve supply chain planning.
Establish Clear Receiving Procedures
Create standardized protocols for warehouse teams to follow upon arrival of goods:
- Verification Checks: Match received goods against purchase orders and packing lists.
- Condition Inspections: Ensure products are damage-free and meet quality standards.
- System Updates: Promptly log received inventory into the WMS to make it available for order fulfillment.
Train and Cross-Train Warehouse Staff
A well-trained team ensures the arrival process is handled efficiently. Provide clear training on inspection protocols, storage procedures, and system updates. Cross-train team members to maintain flexibility during peak seasons or unexpected delays. Encourage feedback from warehouse staff to improve processes over time.
How Shipfusion Handles the ‘Arrived to Facility’ Process
At Shipfusion, the 'Arrived to Facility' status isn’t a passive update — it’s a trigger for action. Our fulfillment centers leverage real-time technology and standardized procedures to ensure that every inbound shipment is:
- Received and Inspected Promptly: Our warehouse teams verify product condition, quantities, and compliance with purchase orders.
- Integrated into Inventory Systems Instantly: Once inspected, products are logged into our proprietary WMS, making them immediately available for order fulfillment.
- Communicated to Clients In Real Time: Our clients gain instant visibility into their inbound inventory through our platform.
This disciplined approach allows Shipfusion to maintain industry-leading order accuracy and on-time fulfillment rates — even during peak seasons.
Optimize Your Ecommerce Operations with Shipfusion
Every step in your ecommerce supply chain matters, and the ‘Arrived to Facility’ status is no exception. When managed effectively, it sets the tone for streamlined fulfillment, accurate inventory management, and superior customer service. If you're ready to eliminate inefficiencies and improve visibility across your entire logistics process, Shipfusion’s end-to-end ecommerce fulfillment solutions are built to help you scale. Our technology-driven approach ensures that every shipment is received, processed, and shipped with precision.
Learn how Shipfusion can help you streamline your inbound logistics — Get a quote today and experience the difference a dedicated fulfillment partner makes.
Share this
You May Also Like
These Related Articles
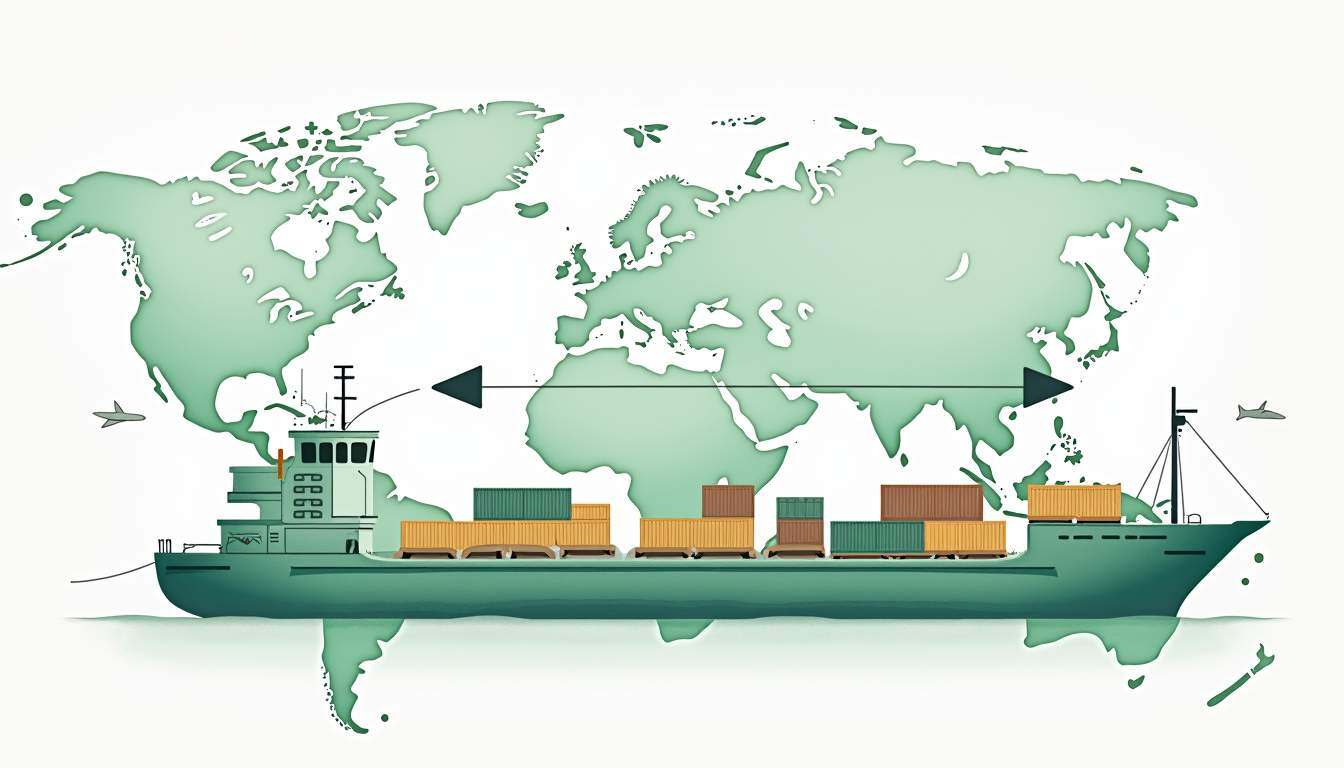
Understanding ASN Shipping Meaning: A Comprehensive Guide
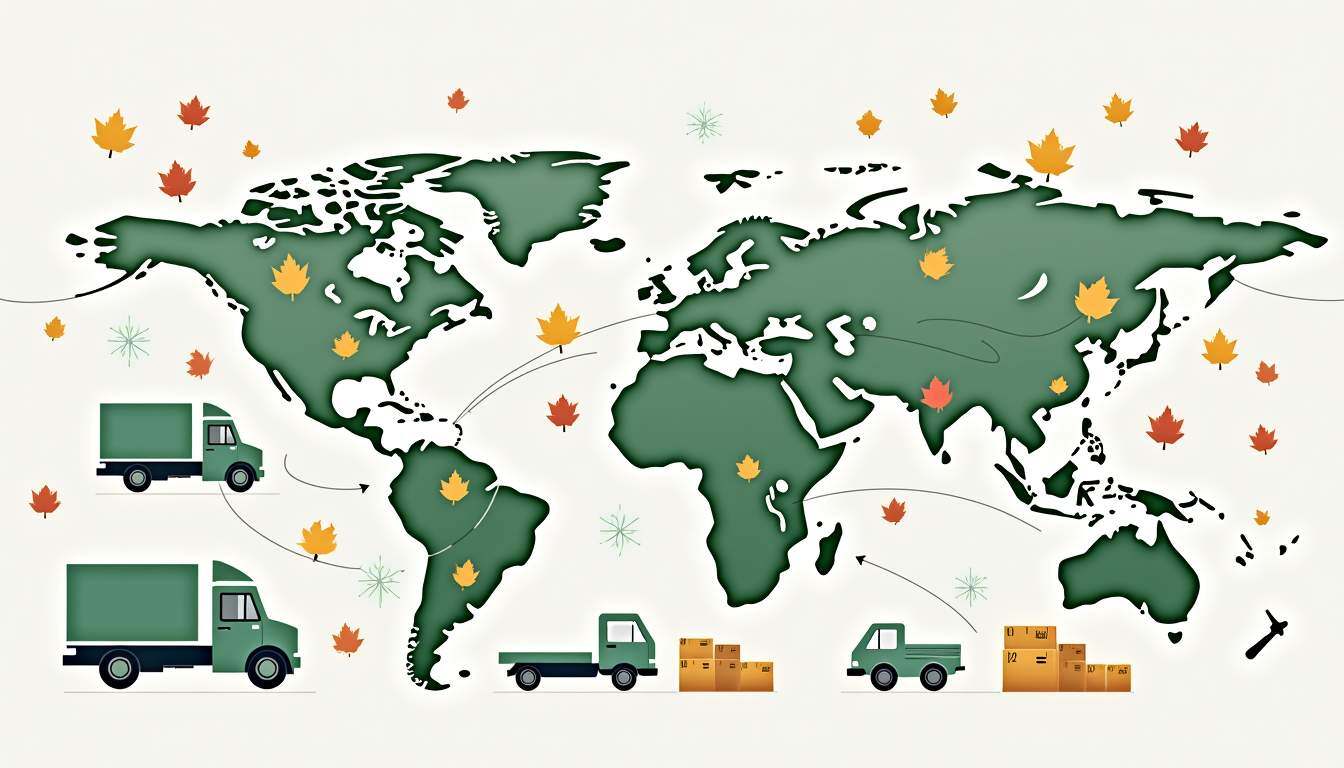
How to Handle Peak Season Logistics Like a Boss
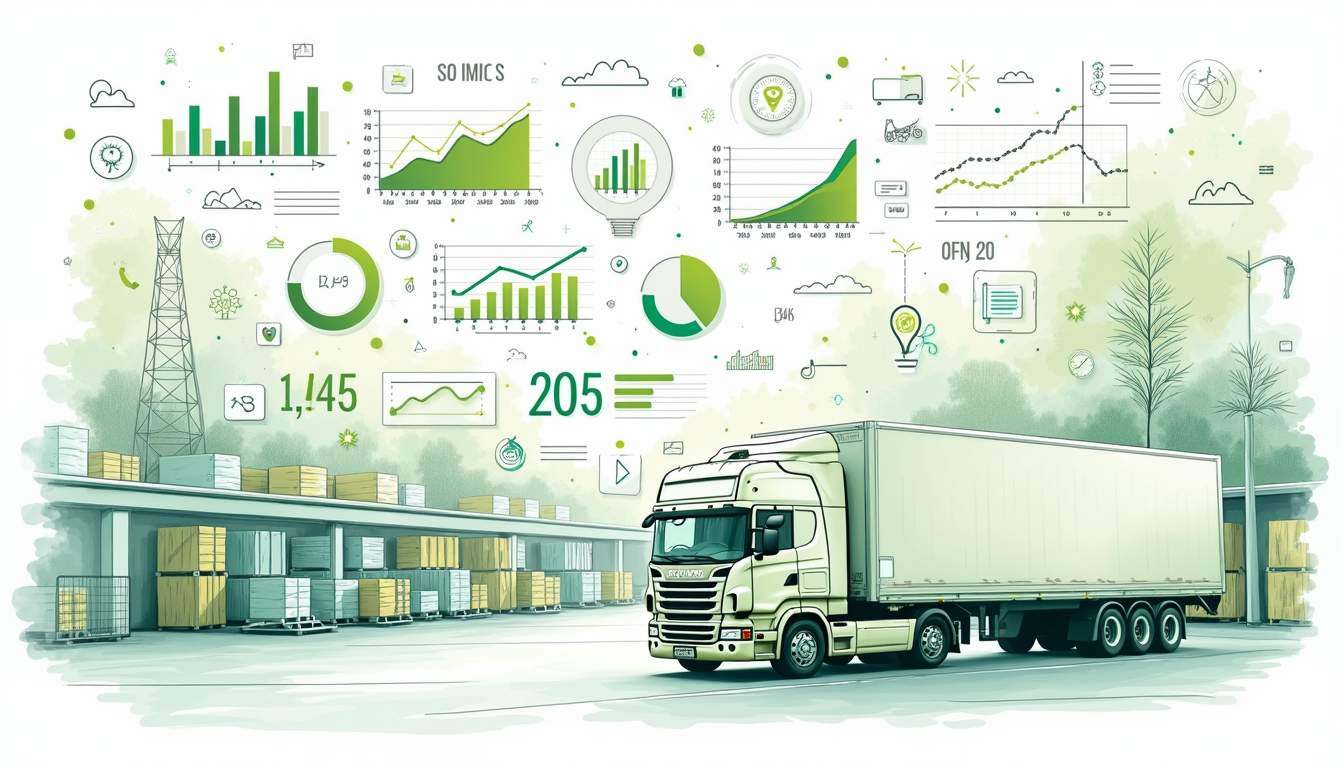
9 Logistics Performance Metrics Your 3PL Should Be Tracking
- April 2025 (12)
- March 2025 (26)
- February 2025 (26)
- January 2025 (37)
- December 2024 (16)
- November 2024 (23)
- October 2024 (22)
- September 2024 (27)
- August 2024 (9)
- July 2024 (8)
- June 2024 (5)
- May 2024 (8)
- April 2024 (8)
- March 2024 (6)
- February 2024 (6)
- January 2024 (5)
- December 2023 (3)
- November 2023 (3)
- October 2023 (5)
- September 2023 (4)
- August 2023 (2)
- July 2023 (1)
- June 2023 (4)
- March 2023 (2)
- October 2022 (1)
- September 2022 (5)
- August 2022 (4)
- July 2022 (7)
- June 2022 (4)
- May 2022 (4)
- April 2022 (6)
- March 2022 (2)
- February 2022 (1)
- January 2022 (3)
- December 2021 (2)
- November 2021 (4)
- October 2021 (2)
- September 2021 (5)
- August 2021 (4)
- July 2021 (4)
- June 2021 (3)
- May 2021 (2)
- April 2021 (3)
- March 2021 (3)
- February 2021 (3)
- January 2021 (2)
- December 2020 (4)
- November 2020 (2)
- October 2020 (4)
- September 2020 (2)
- July 2020 (5)
- June 2020 (4)
- May 2020 (2)
- April 2020 (2)
- March 2020 (4)
- February 2020 (1)
- December 2019 (1)
- May 2018 (1)
- March 2018 (2)
- February 2018 (3)
- January 2018 (3)
- November 2017 (3)
- July 2017 (4)
- March 2017 (3)
- February 2017 (5)
- January 2017 (3)
- December 2016 (4)
- November 2016 (6)
- October 2016 (6)
- October 2015 (1)
- September 2015 (1)
- June 2015 (3)
- May 2015 (3)
- August 2014 (1)
- July 2014 (1)
- March 2014 (1)
- February 2014 (1)